机床轴线精度检测的重要性及技术要点
机床作为现代制造业的核心装备,其轴线精度直接决定了加工零件的尺寸精度、表面质量和工艺稳定性。据统计,60%以上的机床加工误差源于轴线运动精度的偏差。无论是数控机床的X/Y/Z直线轴,还是旋转工作台的A/B/C回转轴,其几何精度、定位精度和重复定位精度的检测与校准都是保证机床性能的核心环节。随着精密加工需求的提升,轴线检测已成为ISO 230、GB/T 17421等国际国内标准强制要求的关键质量管控项目。
机床轴线精度检测的主要项目及方法
1. 直线运动轴线几何精度检测
检测内容:导轨直线度、轴线与基准面的平行度、轴线间垂直度
检测工具:激光干涉仪、电子水平仪、大理石平尺(精度可达0.002mm/m)
执行标准:ISO 230-1:2012第5.3条款规定,直线度允差应≤0.01mm/1000mm
数据处理:通过最小二乘法计算拟合直线,对比理论轨迹的最大偏差值
2. 定位精度与重复定位精度检测
检测原理:采用激光干涉仪进行双向定位测量(Bidirectional Measurement)
关键参数:
- 定位误差:目标位置与实际位置的最大偏差(典型值±0.005mm)
- 重复定位精度:连续7次测量的3σ值(高端机床要求≤0.003mm)
3. 反向间隙检测与补偿
误差来源:传动系统齿轮间隙/丝杠螺母间隙(通常0.005-0.02mm)
检测方法:千分表配合标准量块进行反向冲击测试
补偿策略:通过数控系统参数(如FANUC的1851参数)进行反向间隙补偿
注意事项:检测需在机床预热1小时后进行,温度变化对间隙影响可达0.003mm/℃
4. 轴线垂直度检测
检测设备:直角尺+电子水平仪组合(精度0.005°)或激光准直仪
检测流程:
- 在XY平面安装直角检具
- 沿X轴移动测量Y向偏差曲线
- 计算各点偏离理论垂直度的最大值
5. 动态精度检测(可选)
检测项目:圆度测试(NAS979标准试件切削)、球杆仪检测
设备配置:雷尼绍QC20球杆仪(检测半径300mm圆轨迹误差)
分析指标:反向尖峰、椭圆度、象限突起等动态特性参数
优化方向:伺服增益调整、加速度前馈参数优化
检测结果处理与修正措施
检测数据需通过专业软件(如ML10激光系统配套软件)进行补偿量计算。当轴线误差超过许用值时,应采取:
1. 机械调整:导轨镶条间隙调节(0.02mm塞尺检测)
2. 数控补偿:螺距误差补偿表(通常支持500点补偿)
3. 部件更换:丝杠/导轨磨损量超过0.05mm时建议更换
建议每2000工作小时或重要加工任务前进行系统性检测,确保机床处于最佳精度状态。
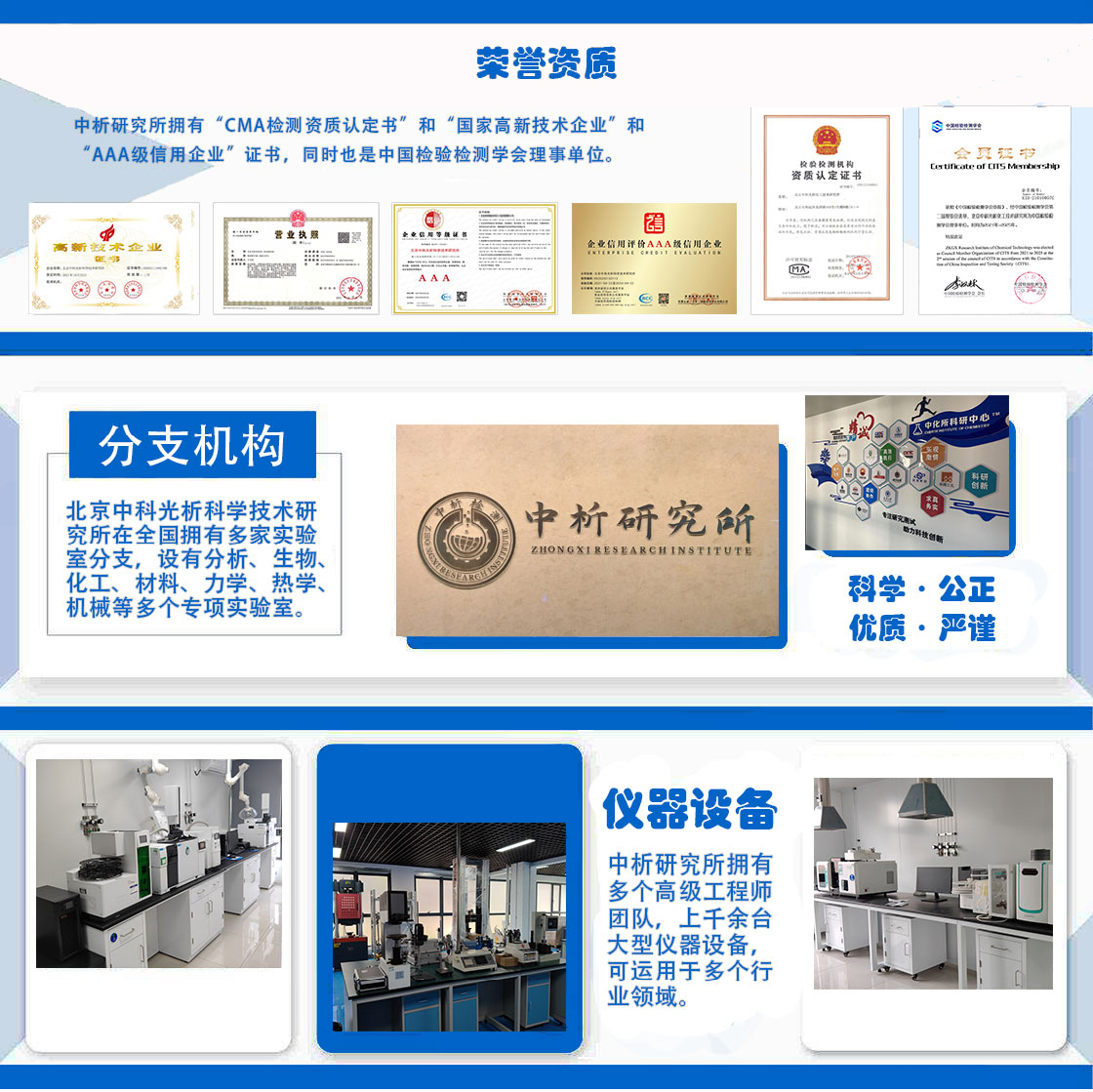
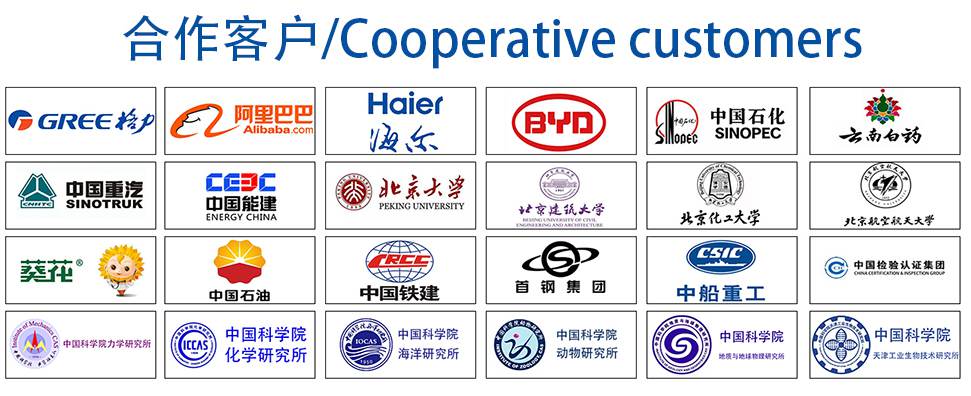