挤奶器检测:守护乳品安全的第一道防线
在现代畜牧业中,挤奶器作为奶牛养殖的核心设备,其性能直接关系到牛奶品质、动物福利及牧场经济效益。随着GB 16798-2020《食品机械安全要求》和ISO 6690:2007国际标准的实施,挤奶器检测已成为乳制品产业链质量管控的关键环节。专业检测不仅涉及设备机械性能验证,更包含微生物控制、材料安全等21项关键指标的系统评估,通过科学检测可有效降低乳房炎发生率,确保每毫升牛奶的菌落总数控制在行业标准要求的10万CFU/ml以内。
核心检测项目体系
1. 基础性能检测
采用激光流量计和压力传感器进行脉动频率测试,验证设备在50-60次/分钟标准范围内的稳定性。真空度检测需保证工作负压维持在38-42kPa之间,波动值不超过±2kPa。通过模拟挤奶流程测试集乳系统密封性,要求30分钟真空泄漏率低于5%。
2. 卫生安全检测
依据GB 4806.7食品接触材料标准,对橡胶衬垫、不锈钢管道等部件进行重金属迁移试验。微生物检测采用ATP生物荧光法,要求清洗后设备表面RLU值≤30。CIP清洗系统验证需确保清洗液残留量低于0.5mg/m²,酸碱浓度误差控制在±0.3%以内。
3. 结构安全评估
使用三维坐标测量仪检测奶爪平衡度,各奶杯重量差需<15g。电气安全测试包括IP65防护等级验证和接地电阻≤0.1Ω检测。关键部件疲劳试验模拟10万次挤奶动作,要求橡胶件无裂纹、金属件无变形。
4. 智能系统验证
对电子脉动器的控制精度进行校验,流量传感器误差需<±1.5%。数据采集系统需通过72小时连续运行测试,数据丢失率应低于0.01%。异常报警系统响应时间检测要求从故障发生到报警提示不超过500ms。
检测流程与技术手段
专业检测机构采用模块化检测平台,集成激光干涉仪(精度0.1μm)、微生物快速检测仪(检出限10CFU/ml)等齐全设备。执行检测时需模拟-5℃至40℃环境温度变化,检测报告应包含设备性能曲线图、材料成分分析谱图等可视化数据。
质量改进与风险防控
通过检测数据可精准定位设备缺陷,如真空泵效率衰减、脉动器相位偏差等潜在问题。统计显示规范检测可使设备故障率降低62%,同时提升15%的挤奶效率。检测机构出具的整改建议书应包含材料升级方案、维护周期优化等具体措施。
在乳制品行业竞争日益激烈的当下,挤奶器检测已超越简单的设备验收范畴,成为构建食品安全追溯体系的重要基石。权威检测机构出具的 认证报告,不仅为设备制造商提供技术改进方向,更为牧场主选择设备、保险公司评估风险提供科学依据,最终确保从牧场到餐桌的全链条质量可控。
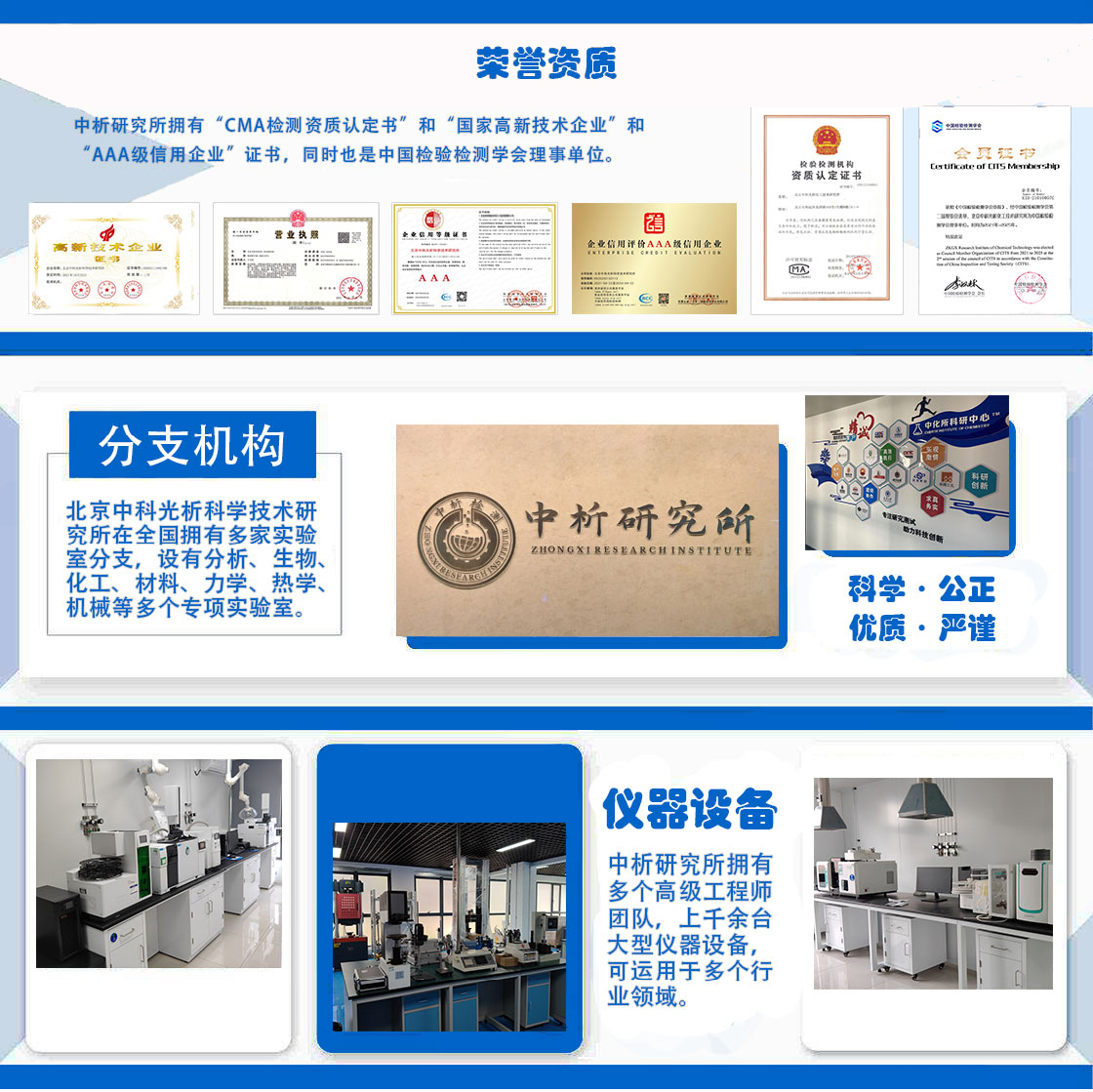
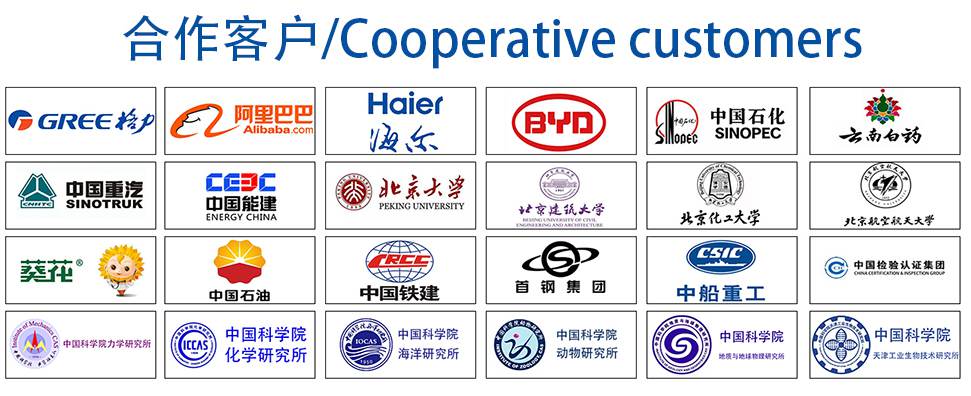