金属器皿检测的重要性与核心关注点
在食品加工、化工生产、日用品制造等领域,金属器皿作为直接接触物料或人体的关键载体,其质量安全直接影响产品性能与使用者健康。金属器皿检测通过系统性质量评估,可有效发现材料缺陷、工艺隐患及潜在安全风险,避免因重金属迁移、结构失效等问题导致的食品安全事故或工业事故。根据GB 4806.9-2016《食品安全国家标准 食品接触用金属材料及制品》等法规要求,金属器皿需通过理化性能、机械强度、耐腐蚀性等十余项专业检测方可投入使用。
核心检测项目体系解析
1. 材质成分与有害物质检测
采用X射线荧光光谱仪(XRF)或电感耦合等离子体质谱(ICP-MS)对器皿基材进行元素定量分析,重点监测铅、镉、砷、汞等重金属迁移量是否符合GB 31604.49-2020限量标准。对电镀层、涂层等表面处理工艺,需额外检测六价铬、双酚A等化学物质残留。
2. 表面质量与结构完整性检测
通过目视检查结合3D轮廓仪评估器皿表面光洁度、划痕、凹陷等缺陷;使用划格试验法(ASTM D3359)测试涂层附着力;运用金相显微镜分析焊接部位微观结构,排查虚焊、气孔等隐患。压力容器类产品还需进行水压爆破试验验证承压能力。
3. 力学性能与耐久性测试
依据ISO 6507标准进行维氏硬度测定,评估材料抗变形能力;通过万能材料试验机开展拉伸、压缩、弯曲等力学试验,获取屈服强度、弹性模量等关键参数。循环载荷测试可模拟实际使用中的疲劳损伤,预测产品使用寿命。
4. 耐腐蚀与耐候性评估
采用中性盐雾试验(GB/T 10125)模拟海洋大气环境腐蚀,湿热试验(GB/T 2423.3)验证高温高湿环境耐受性。针对食品接触场景,需进行酸性/碱性介质浸泡实验,检测金属离子析出量及器皿表面腐蚀等级。
5. 功能性专项检测
对密封容器实施氦质谱检漏仪气密性测试,确保泄漏率≤1×10⁻⁶ Pa·m³/s;导热器具需测定热传导系数(ASTM D5470);电磁炉适用炊具需通过涡流检测验证磁导率与发热效率的匹配度。
检测技术发展趋势
随着AI视觉检测、太赫兹成像等新技术应用,金属器皿缺陷识别精度已提升至微米级。2023年新实施的ISO 22000:2023体系更强调全过程质量追溯,推动检测机构建立数字化检测平台,实现检测数据与生产线的实时交互反馈。
通过上述多维度的检测体系,可全面把控金属器皿从原材料到成品的质量风险点。生产企业应建立涵盖来料检验、过程监控、成品抽检的全生命周期检测方案,确保产品符合GB、ISO、FDA等国内外标准要求,为市场提供安全可靠的金属器皿制品。
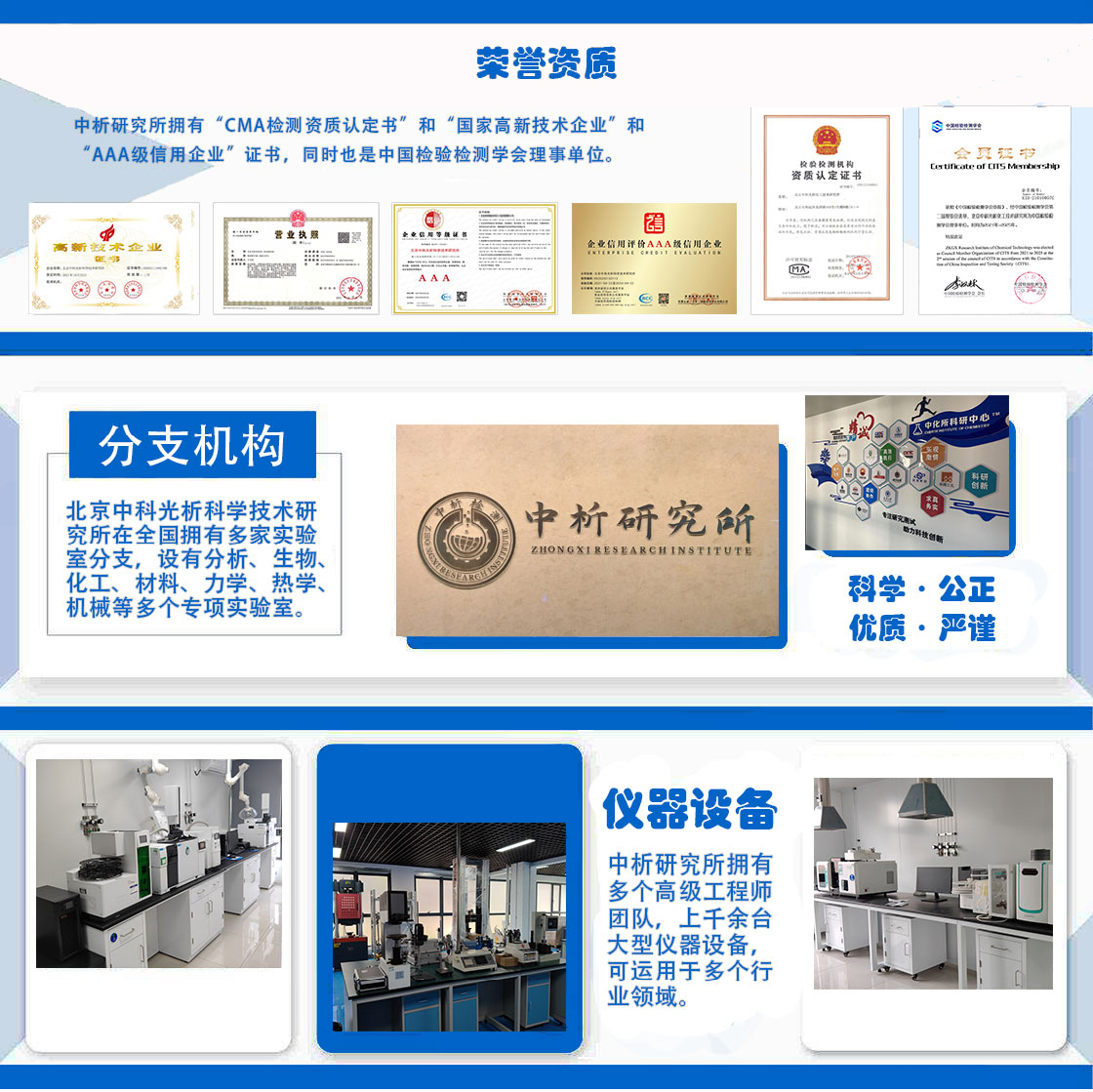
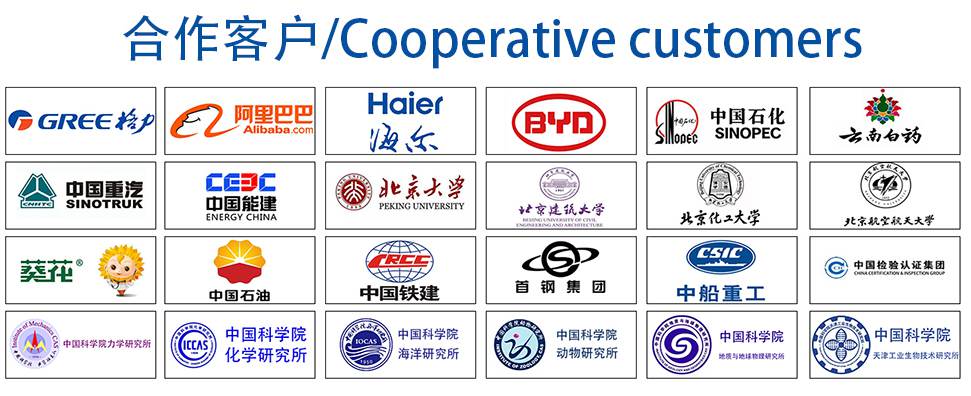