锂离子电池石墨类负极材料检测的重要性
随着锂离子电池在新能源汽车、消费电子及储能领域的广泛应用,石墨类负极材料作为电池核心组件的关键材料,其性能直接决定了电池的能量密度、循环寿命和安全性。近年来,市场对高容量、快充型电池的需求持续增长,对石墨材料的质量控制提出了更高要求。通过系统化的检测项目,可有效评估材料的理化特性、电化学性能及安全性,从而优化生产工艺、降低失效风险,并为电池制造商提供可靠的材料筛选依据。
理化性能检测
石墨类负极材料的物理化学性质直接影响其与电解液的兼容性和锂离子嵌入/脱出效率。主要检测项目包括: 粒度分布(激光粒度仪分析,依据GB/T 19077-2016),确保颗粒均匀性以避免局部极化; 比表面积(BET法,参照ISO 9277:2022),高比表面积可能增加副反应风险; 振实密度(振实密度仪测试,标准GB/T 24533-2019),影响电极涂布均匀性; 水分含量(卡尔费休法,GB/T 6283-2008),超标水分会引发电解液分解。
电化学性能检测
通过模拟电池实际工况,评估材料的储能与循环稳定性: 首次充放电效率(扣式半电池测试,0.1C倍率下效率需>90%); 循环性能(长周期充放电测试,500次循环后容量保持率≥80%); 倍率性能(不同电流密度下的容量衰减率,如1C/5C对比); 阻抗分析(EIS测试),揭示锂离子扩散阻力及SEI膜稳定性。
结构表征分析
材料的微观结构与其电化学行为密切相关: X射线衍射(XRD):分析石墨化程度(峰强度比R值)及层间距(d002值); 扫描电镜(SEM):观察颗粒形貌、裂纹及表面包覆完整性; 拉曼光谱(Raman):检测缺陷密度(ID/IG比值),理想值应低于0.2; 透射电镜(TEM):揭示纳米级包覆层厚度及结晶状态。
杂质及有害元素分析
严格控制杂质含量可避免电池自放电或热失控: 金属杂质(ICP-MS检测Fe、Cu、Ni等,要求总量<50ppm); 硫/磷元素(燃烧法检测,避免生成有害气体); 磁性异物(磁性物质测定仪,防止微短路)。
安全性能测试
通过极端条件模拟验证材料可靠性: 热稳定性(TGA-DSC联用,评估材料在高温下的分解温度及放热量); 过充/过放测试(电压超限至5V/0V,观察是否析锂或结构坍塌); 热滥用测试(150℃高温存储后检查产气及形变); 针刺测试(模拟内短路,监测温升速率是否超标)。
总结
锂离子电池石墨负极材料的检测体系需覆盖从微观结构到宏观性能的多维度指标。随着硅碳复合、硬碳等新型负极材料的开发,检测项目将向更高精度、多参数耦合的方向发展。通过建立标准化的检测流程,可为材料研发、生产及电池应用提供全链条质量保障。
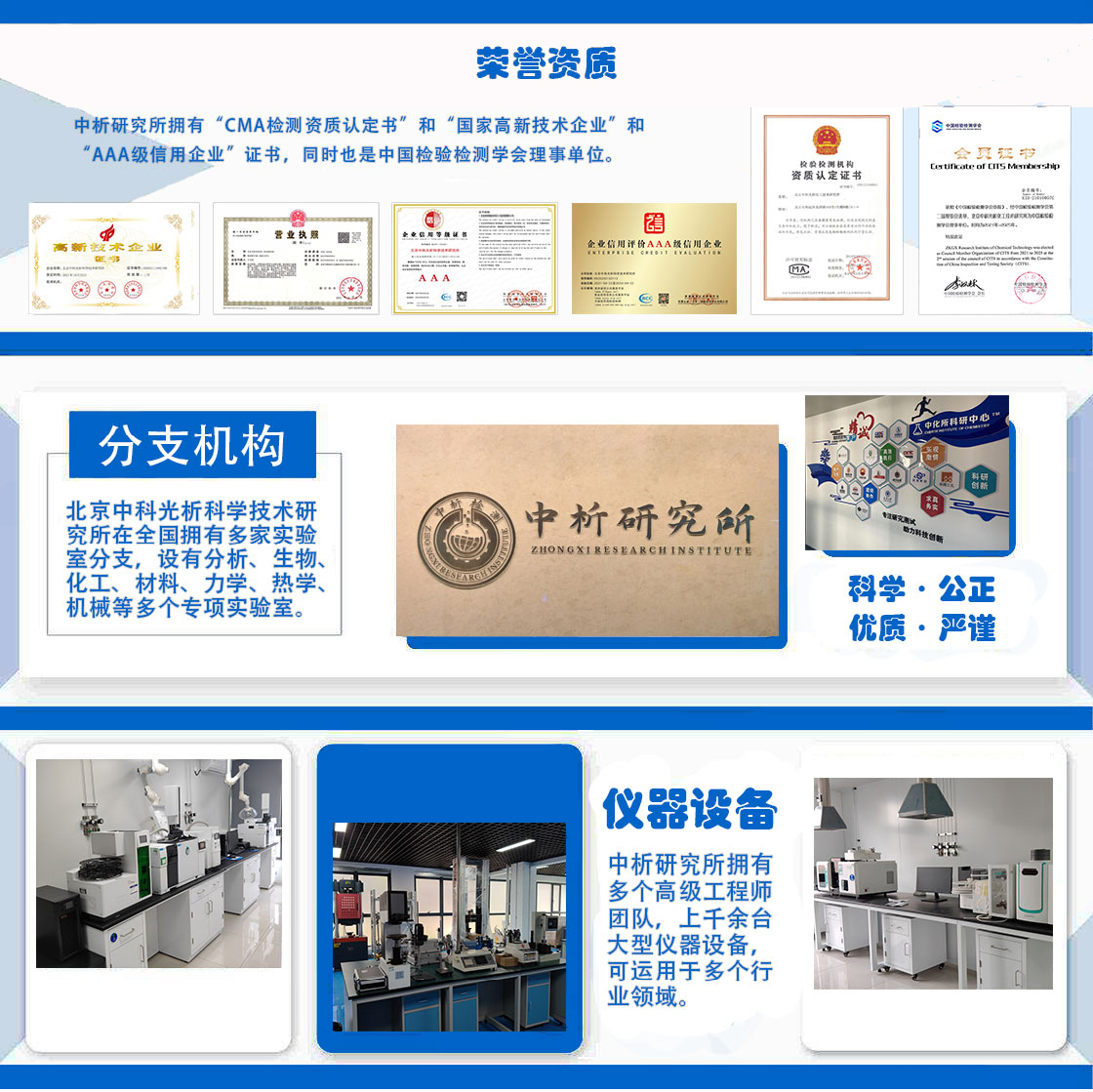
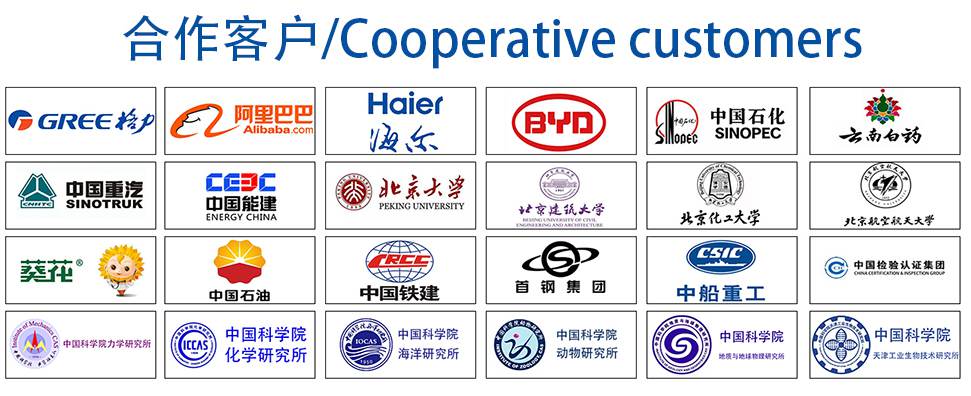