原料气压缩机与空气压缩机检测的重要性
在石油化工、天然气处理及工业制造领域,原料气压缩机和空气压缩机作为核心动力设备,承担着气体增压输送的关键职能。随着设备运行时间的累积,压缩机内部组件磨损、密封性能下降等问题日益凸显,定期开展系统性检测成为保障设备安全稳定运行、延长使用寿命的必要手段。通过科学规范的检测流程,可精准定位潜在故障隐患,优化设备运行参数,实现能耗降低15%-30%,同时避免因设备突发故障导致的全线停工风险。
核心检测项目分类体系
压缩机检测体系可分为结构完整性检测、运行性能检测、安全防护检测三大模块。结构检测涵盖壳体应力分析、转子动平衡测试;性能检测包括容积效率测算、温升曲线监测;安全检测则涉及防爆系统验证、紧急停机响应测试等关键指标。
原料气压缩机专项检测内容
1. 气体成分适应性检测:测定H2S、CO2等腐蚀性介质浓度,评估叶轮材质耐蚀等级
2. 级间密封效能测试:采用氦质谱检漏仪检测密封间隙泄漏率,控制值≤0.5%
3. 振动频谱分析:通过加速度传感器捕捉0-10kHz频段振动特征,识别轴承早期缺陷
4. 冷却系统效率验证:计算换热器端差,确保温升不超过设计值5℃
空气压缩机关键检测指标
1. 排气压力稳定性测试:连续监测48小时压力波动范围,偏差值需<±2%
2. 润滑油污染度分析:采用颗粒计数仪检测油液NAS等级,控制值≤8级
3. 气阀动态响应测试:高速摄影机捕捉阀片运动轨迹,开启延迟应<0.3ms
4. 能效比测算:基于ISO1217标准计算比功率,优化后应达2级能效标准
智能化检测技术应用
现代检测体系融合物联网与大数据技术,配置在线监测系统实现:
- 实时采集16类运行参数,数据更新频率达10Hz
- 智能诊断系统自动比对3000+故障特征数据库
- 生成三维热力学仿真模型,预测剩余使用寿命误差<5%
该技术使故障预警准确率提升至98%,维修响应时间缩短70%。
检测标准与周期规范
严格遵循API 618(往复式)、API 617(离心式)标准要求,制定分级检测方案:
- 日常巡检:每班次进行外观检查及基础参数记录
- 月度检测:开展振动分析和润滑油检测
- 年度大检:实施全面解体检测与性能标定
- 特殊检测:累计运行20000小时后的转子探伤检测
检测结果应用价值
科学系统的检测数据可指导企业:
1. 优化维保策略,降低维护成本30%以上
2. 建立备件寿命预测模型,库存周转率提升40%
3. 实现能效动态管理,年节电量可达15-25万kWh
4. 形成设备健康档案,为技改决策提供数据支撑
通过构建全生命周期的压缩机检测管理体系,企业可有效控制运营风险,据行业统计数据显示,实施系统检测的企业设备故障率下降65%,综合运营效率提升22%,在安全生产和经济效益方面取得显著成效。
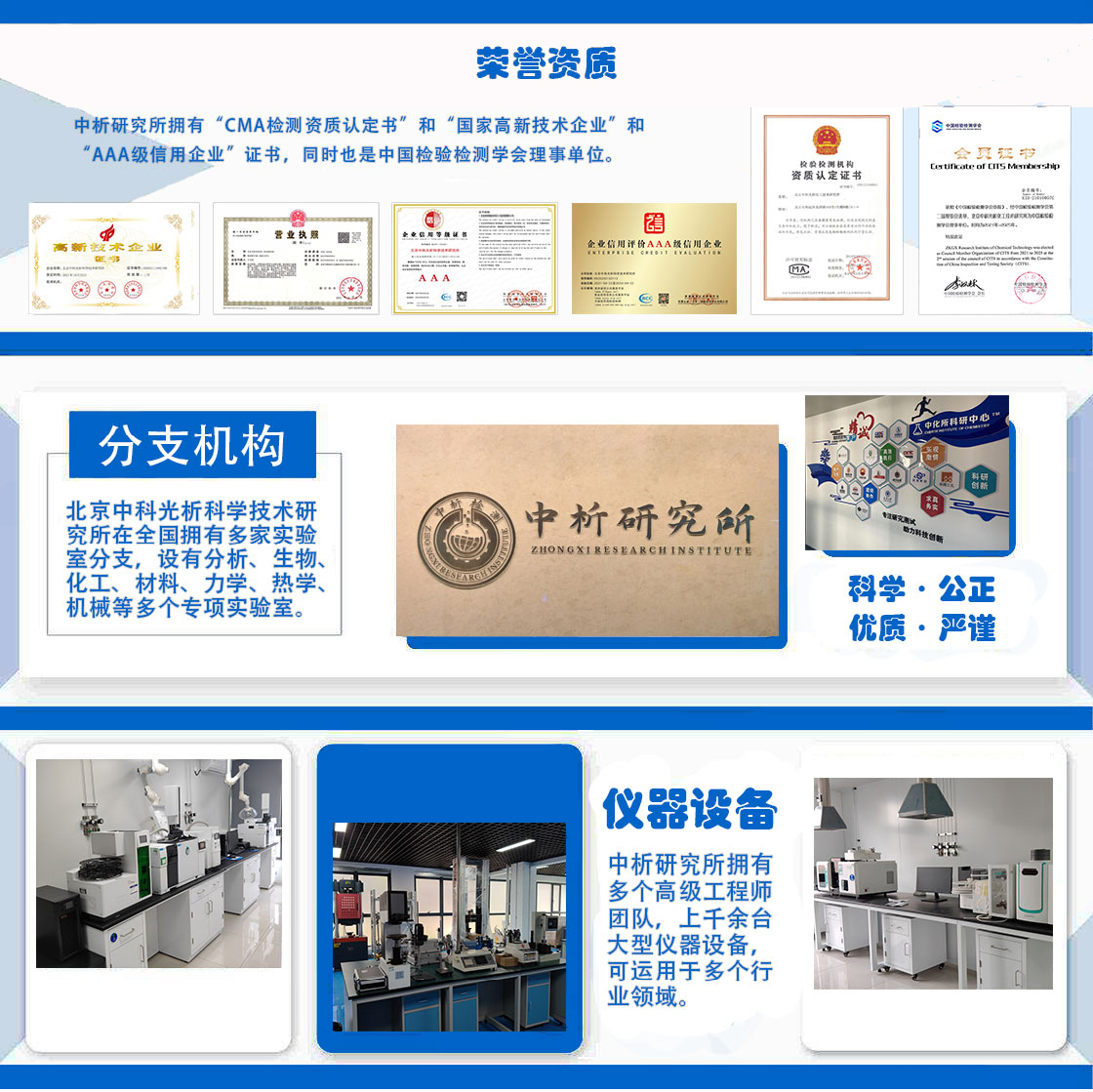
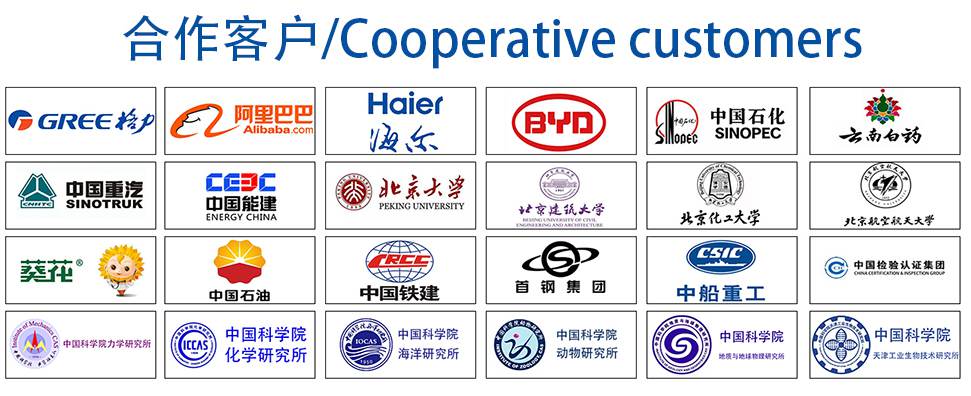