电动汽车动力系统检测:保障安全与性能的关键环节
随着新能源汽车市场的快速发展,电动汽车动力系统作为整车的"心脏",其性能表现直接决定了车辆的续航里程、动力输出和使用寿命。由动力电池组、驱动电机、电控系统(BMS/MCU)构成的三电系统,通过精密协同实现了电能到机械能的高效转换。为确保动力系统在复杂工况下的稳定运行,涵盖"机械-电气-热管理"三位一体的专业检测体系已成为行业标准要求。
核心检测项目体系
1. 电池系统综合检测
采用电池模拟器与专业诊断设备,进行单体电芯电压一致性(±20mV容差)、内阻变化(精度达0.1mΩ)、容量衰减(循环测试≥2000次)、热失控预警(温度梯度≤5℃)等关键指标检测。通过HPPC脉冲测试评估动态特性,利用EIS电化学阻抗谱分析老化程度。
2. 驱动电机性能验证
在电机测试台架上模拟0-6000rpm全工况测试,检测效率MAP图(峰值≥95%)、转矩脉动(≤3%)、NVH特性(1/3倍频程分析)。采用红外热成像仪监控绕组温升,配合振动传感器采集轴向/径向振动数据(分辨率0.1μm)。
3. 电控系统功能测试
基于ISO 26262标准构建故障注入测试平台,验证BMS过压/欠压保护(响应时间<50ms)、绝缘监测(精度±5%)、SOC估算误差(≤3%)。通过CANoe工具模拟200+种异常工况,确保控制系统鲁棒性。
4. 热管理系统效能评估
在环境仓内开展-30℃至55℃温区测试,监测液冷回路压降(ΔP≤15kPa)、PTC加热速率(≥3℃/min)、制冷剂充注量偏差(±10g)。运用CFD仿真优化散热流道设计,确保系统温差<8℃。
5. 高压电气安全检测
使用2500V耐压测试仪验证绝缘电阻(≥500MΩ),通过局部放电检测定位潜在击穿点。对接插件进行机械振动测试(20-2000Hz/3h),接触电阻变化率控制在±5%以内。
6. 充电兼容性测试
依据GB/T 27930协议,模拟不同充电桩(CCS/CHAdeMO/GB)交互测试。检测充电握手协议兼容性、功率阶跃响应(500ms内完成)、紧急停机功能可靠性。
创新检测技术应用
行业前沿实验室已引入数字孪生技术,通过搭建1:1虚拟动力系统模型,实现故障预测准确率提升40%。结合大数据分析平台,对海量运行数据(采样率10kHz)进行特征提取,建立寿命预测模型(R²≥0.95)。
检测标准与法规要求
检测体系严格遵循UN R100、GB/T 31467.3、ISO 19453等国际标准,针对不同气候带(湿热/干热/寒带)制定差异化测试方案。最新修订标准新增涉水测试(300mm/30min)、盐雾腐蚀(1000h)等严苛工况验证。
随着800V高压平台、SiC功率器件等新技术的普及,检测项目正向更高精度(μV级测量)、更快响应(ns级采样)、更复杂场景(V2X交互)演进。建立全生命周期检测数据库,将成为提升产品可靠性和市场竞争力的核心要素。
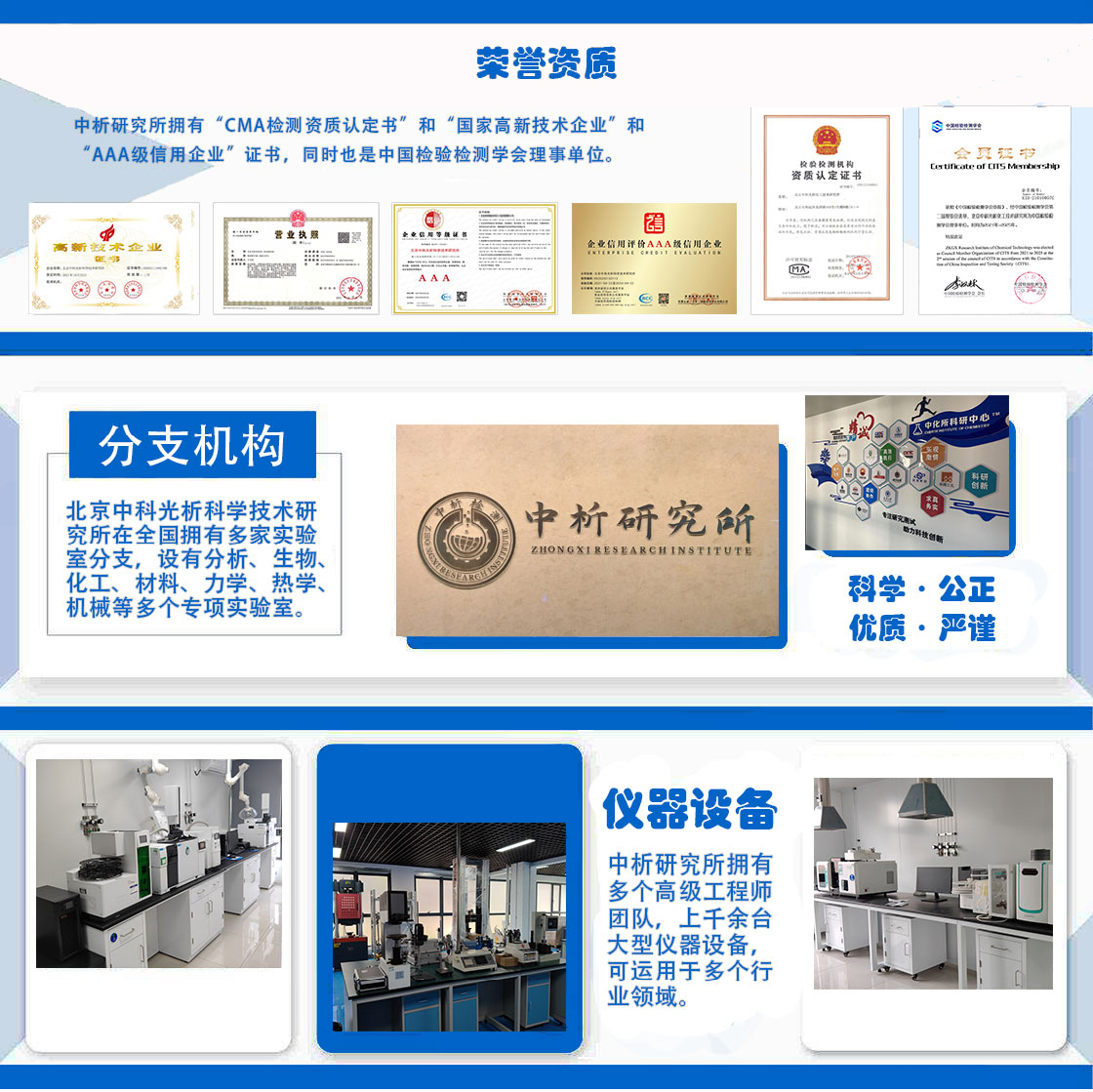
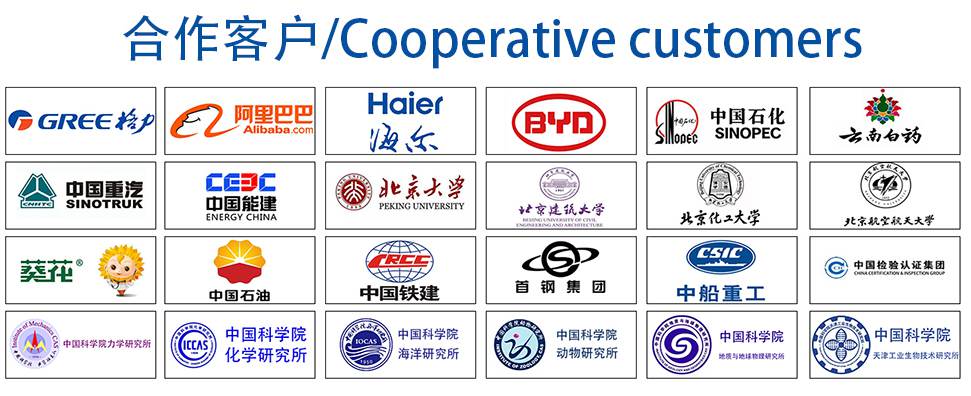