钢锤检测项目及技术要求
一、材料质量检测
-
- 化学成分分析:检测碳(C)、锰(Mn)、硅(Si)等元素含量,确保符合工具钢标准(如45#钢或同等材质)。
- 硬度测试:锤头工作面硬度需达到HRC 46-55(洛氏硬度),非工作面HRC 28-40,以平衡强度与抗冲击性。
- 金相组织检验:观察材料内部结构(如马氏体、残余奥氏体比例),判断热处理工艺是否合格。
-
- 木材检测:含水率≤16%,无腐朽、裂纹;弹性模量需≥10 GPa(如白蜡木、山毛榉)。
- 复合材料检测:玻璃纤维或碳纤维锤柄需测试抗拉强度(≥500 MPa)与抗弯强度。
二、结构完整性检测
-
- 锤头重量误差:±3%(以标称重量为基准)。
- 锤头与锤孔配合公差:过盈量需控制在0.1-0.3 mm,防止松动。
-
- 楔紧度检测:锤头与锤柄安装后,施加轴向拉力≥500 N,位移≤1 mm。
- 动态冲击测试:以额定载荷连续冲击1000次,锤头与锤柄无分离或裂纹。
-
- 目视检查:锤头表面无气孔、夹渣、折叠等缺陷。
- 磁粉探伤/超声波探伤:检测内部细微裂纹或夹杂物(缺陷深度≤0.5 mm)。
三、安全性能检测
-
- 锤击面边缘需倒圆(半径≥2 mm),非击打面倒角≥45°。
- 锤柄末端防滑凸缘高度≥5 mm,防止脱手。
-
- 将钢锤冷却至-20℃,进行低温冲击试验(参考ISO 11148标准),锤头无碎裂。
-
- 重心位置偏差:纵向偏离锤头中心线≤5%。
四、耐久性及功能性测试
-
- 模拟实际工况,以10 J冲击能量连续作业5000次,锤头变形量≤1%。
-
- 盐雾试验(GB/T 10125):电镀层、涂层经48小时测试后,表面锈蚀面积≤5%。
-
- 手柄直径设计符合人体工学(25-35 mm),表面防滑纹路摩擦系数≥0.4。
五、检测方法及设备
检测项目 | 方法 | 设备 |
---|---|---|
硬度检测 | 洛氏硬度计压痕法 | 洛氏硬度计 |
成分分析 | 光谱分析法 | 直读光谱仪 |
内部缺陷检测 | 超声波探伤 | 数字超声探伤仪 |
动态冲击测试 | 落锤冲击试验机 | 程控冲击试验台 |
上一篇:内六角扳手检测下一篇:电线连接工具 手动机械压线钳检测
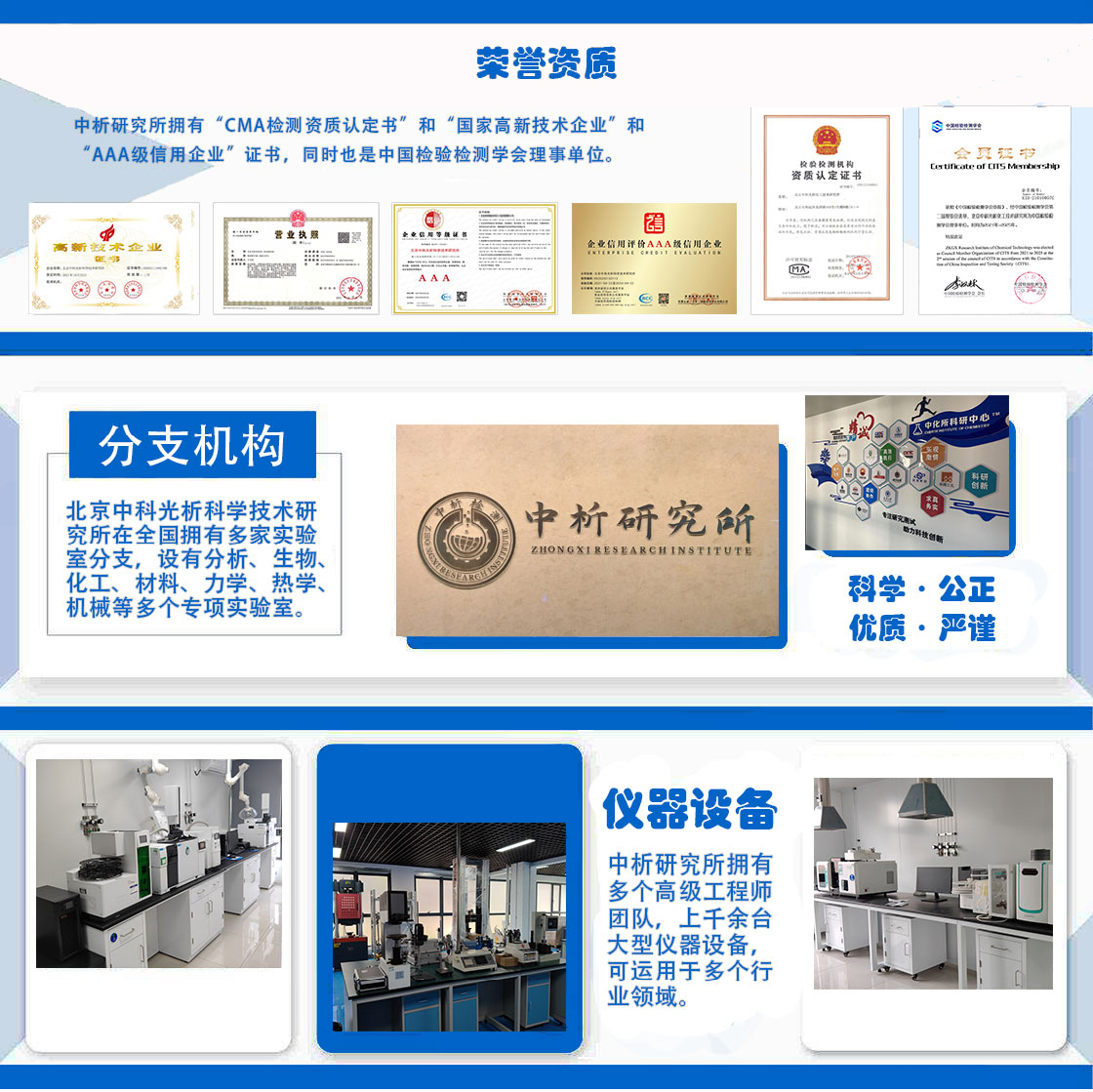
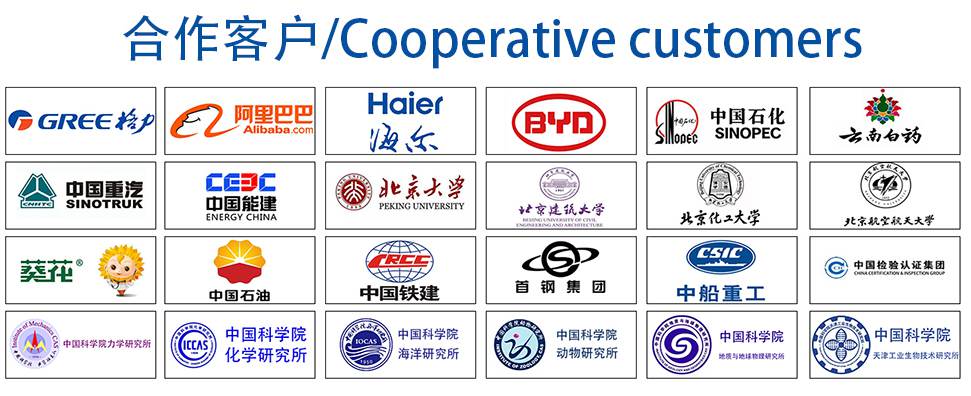
材料实验室
热门检测
254
212
189
202
195
203
207
200
206
214
202
197
195
201
194
192
205
197
206
200
推荐检测
联系电话
400-635-0567