聚氨酯发泡零件拉伸强度检测
聚氨酯发泡零件拉伸强度检测的重要性
聚氨酯发泡材料以其优异的加工性、轻质、高弹性和良好的力学性能,在工业、建筑、汽车、航空航天等领域得到了广泛应用。聚氨酯发泡零件的质量与其力学性能密切相关,其中拉伸强度是反映其性能的重要指标之一。进行拉伸强度检测,不仅可以帮助评估材料品质,还能指导产品设计与工艺优化,确保最终产品的安全性与可靠性。
聚氨酯发泡材料的特点与用途
聚氨酯发泡材料分为硬质发泡、软质发泡和半硬质发泡三种类型。硬质发泡材料具有出色的保温性能,广泛用于建筑保温板、管道隔热层等场合。软质发泡材料柔软且回弹性好,常用于家具、床垫以及汽车座椅等。半硬质发泡材料则兼具硬质和软质发泡的一些特点,常用于需要一定强度又具缓冲性能的场景。
在这些应用中,聚氨酯发泡零件将面临不同程度的物理应力。例如,汽车内饰件需要经受长时间的外力作用而保持形状不变;建筑保温材料则需要长期承受温度变化中的热胀冷缩。因此,拉伸强度的检测能够验证材料的抗拉性能是否符合使用要求。
拉伸强度的定义及检测原理
拉伸强度是指材料在拉伸试验过程中所能承受的最大拉应力。具体来说,当材料受到外力作用时,会发生从弹性变形到塑性变形,直到出现断裂破坏的过程。拉伸测试通过模拟这种非均质拉伸状态,测量材料的最大承受能力,即拉伸强度。拉伸强度检测值的高低直接反映了材料抗拉性能的优劣。
对于聚氨酯发泡零件而言,其力学性能受发泡剂、密度、工艺条件等因素的影响。通过拉伸强度检测,可以揭示材料内部分子间键的强度、均匀度以及整体结构的完整性,从而为质量评定提供科学依据。
拉伸强度检测设备与规范
聚氨酯发泡材料的拉伸强度检测通常采用电子万能拉力试验机或专门设计的发泡材料测试系统。这些设备能够对力值和位移进行精确测量,实时绘制应力-应变曲线,记录试样在拉伸过程中的性能参数。
实验前,需要根据相关标准(如ISO 527、ASTM D3574)切割出标准尺寸的试样。通常,试样被制成哑铃状,以确保测试过程中的应力分布均匀,从而提高实验结果的准确性。设备夹具将试样固定后,以一定的拉伸速度(一般为50-500 mm/min)逐渐施加载荷,直至试样断裂。在此过程中,检测设备会记录试样断裂时的最大力值,并结合试样截面积计算出拉伸强度。
拉伸强度检测中的常见问题
尽管拉伸强度检测技术相对成熟,但实际操作中仍存在一些问题影响检测结果的准确性。例如,试样切割过程中,如果工具过钝或方法不当,会导致试样边缘不规则,进而影响受力分布。此外,试样在夹持过程中如果未能正确固定,可能会导致扭曲、滑移或局部应力集中,最终导致虚高或低估的拉伸强度值。
另外,由于聚氨酯材料内部存在发泡结构,其致密性和均匀性受制于发泡工艺波动。在检测过程中,试样某些部位的微气孔或密度变化会导致断裂位置的离散性。这种现象常常要求实验人员结合多次检测结果进行对比分析,而不能仅依赖于单次测试数据进行结论判断。
优化拉伸强度检测的策略
为了提高聚氨酯发泡零件拉伸强度检测的准确性与可靠性,可以采取以下策略:
- 优化试样制备:使用高精度切割设备和模板确保试样尺寸和形状的准确性。
- 改进夹具设计:采用专门用于发泡材料的夹具,避免试样夹持过程中出现滑移或扭曲。
- 控制检测条件:在恒温、恒湿实验室中进行检测,减少环境因素对实验结果的影响。
- 综合多次数据:对同一类型试样进行多次测试,以获得代表性强的拉伸强度均值。
- 结合其他检测手段:除了拉伸强度检测,可以结合剪切强度、抗压强度测试等数据,全方位评估材料性能。
拉伸强度检测在实际应用中的意义
聚氨酯发泡零件广泛应用于多个行业领域,其安全性和可靠性直接关系到产品的使用寿命和用户体验。例如,在汽车座椅中,拉伸强度不足的发泡材料可能导致座椅缓冲性能的下降,增加乘坐者的不适感;而在建筑行业中,低拉伸强度的保温板可能会在外力作用下断裂,从而影响建筑整体的保温效果。通过拉伸强度检测,可以提前发现潜在的材料问题,避免由于材料性能不足而导致的质量隐患。
同时,拉伸强度检测结果对于优化聚氨酯材料的生产工艺具有重要指导作用。通过分析检测数据,研发人员可以调整发泡剂用量、改进混合工艺,进一步提高产品的性能稳定性。此外,在产品开发阶段,使用拉伸强度检测数据能够帮助工程师选择最佳材料配置和工艺参数,从而实现产品性能与生产成本的最优平衡。
总结
聚氨酯发泡零件的拉伸强度检测不仅是评估其力学性能的重要环节,更是保障其在实际应用中表现可靠的关键手段。通过系统化的检测,可以全面了解材料的抗拉性能,为产品设计、生产工艺优化以及后续质量控制提供科学依据。随着检测技术的进步以及对材料性能要求的提高,未来的拉伸强度检测必将在更精确、更广泛的层面上发挥更为重要的作用。
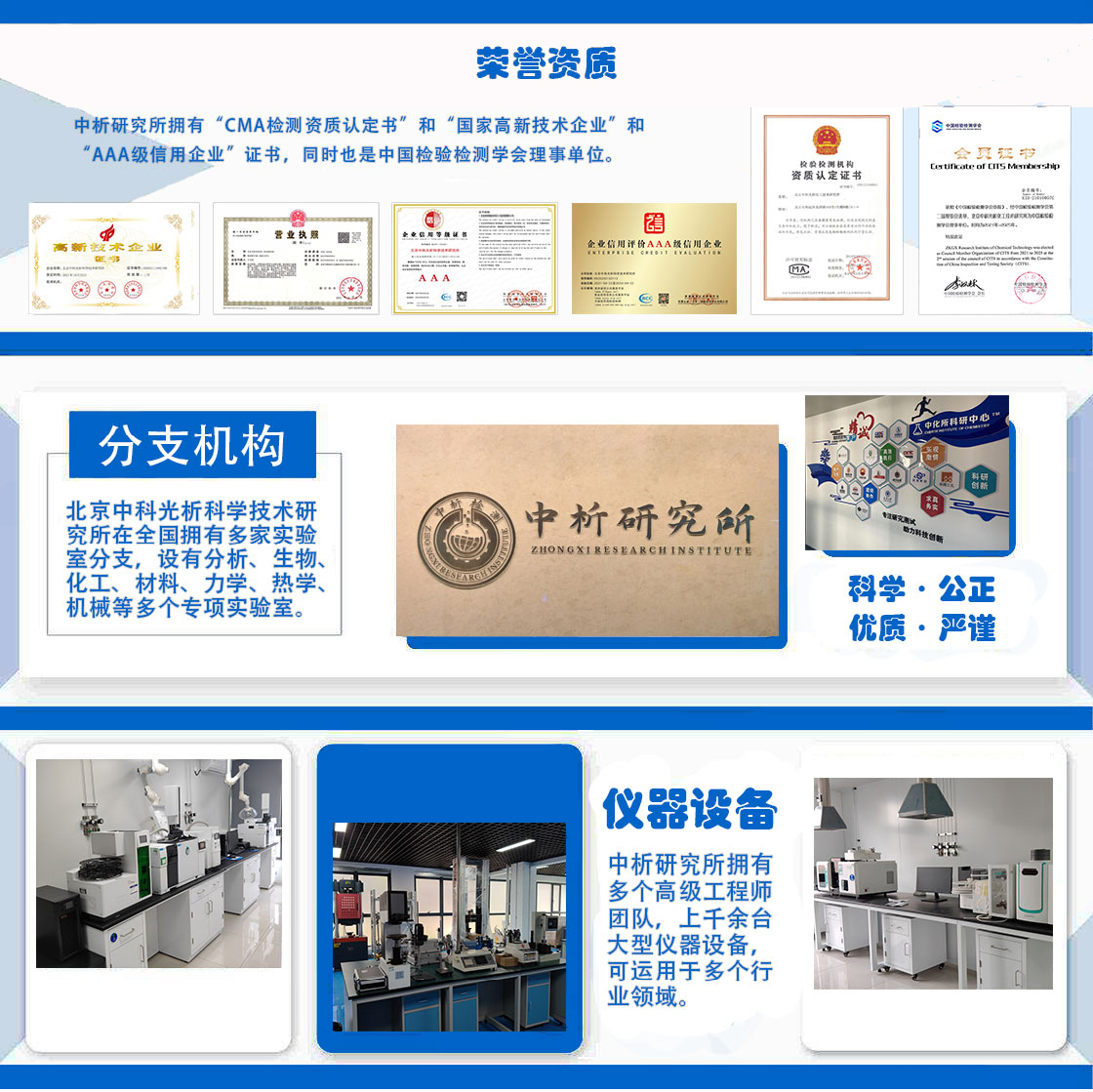
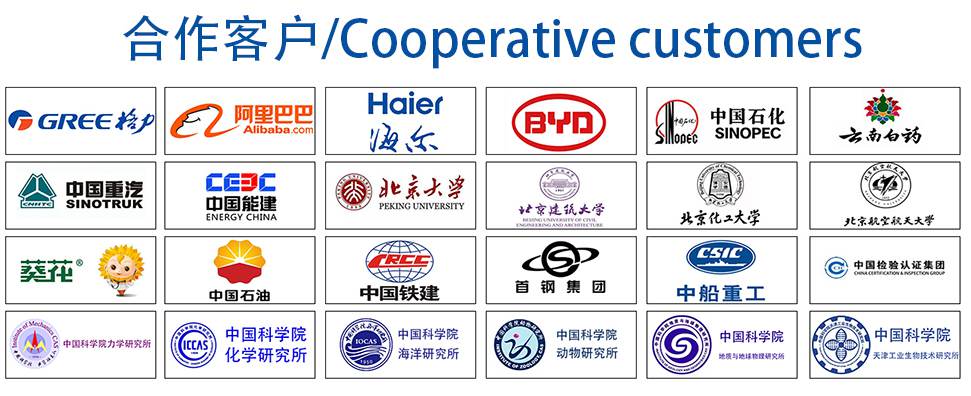