通用零件跳动检测
通用零件跳动检测的背景与意义
在现代工业制造中,零件的精度监控和质量保证是提高生产效率和产品质量的关键。通用零件在各种机器设备中扮演着至关重要的角色,而零件的跳动(runout)是指其在旋转过程中因形状或装配的不完美导致的偏移或不规则运动。这种现象如果不及时检测和控制,将会导致设备震动、磨损增加、性能下降甚或是故障停机。因此,通用零件跳动检测在工业场合具有重要的实际意义。
跳动检测的原理
零件的跳动检测是通过测量其旋转中心偏移的程度来判断质量问题。一般而言,跳动产生的原因可能包括几何误差(如同心度偏差)、装配误差或者材质不均匀等。其检测原理主要基于物理测量,比如通过微尺、激光测距仪、或者电子传感器等工具实现。
在具体应用中,通常会将零件放置在一个工作台上,通过旋转机构让其缓慢旋转,使用高精度测量工具沿着零件的周边进行连续的测量。所获得的数据会通过计算机软件进行分析,生成相应的图表,帮助技术人员判断零件是否符合标准。
通用零件跳动检测的技术方法
在不同的工业应用中,针对各种类型的通用零件,有几十种不同的检测方法和技术手段。以下是其中一些常用的方法:
1. 机械测量工具
机械指示表或机械千分尺是经典的测量工具。这些工具通过其精密的指针指示出零件旋转时的跳动值。尽管这些工具简单,但在需要高度精度的测量中,它们显示出一些不足之处,容易受到操作人员水平和环境条件的影响。
2. 光学检测技术
光学技术利用激光和光电感应器来进行非接触式测量。这些设备通过发射和接收反射光束的角度或者时间差,来快速计算出零件的跳动度。光学技术具有精度高、响应快、适合在线实时监控等优点,越来越广泛地应用在高精密制造业中。
3. 电磁感应技术
电磁感应是一种新兴的检测技术,尤其在检测不易触及或者不规则表面的零件时,它显得尤为有效。通过线圈感应电磁场变化,可以精确计算出零件的偏心效果。这种方法适应性强,可用于各种材料和形状的零件,但需要复杂的校准和数据处理。
工业应用实例
跳动检测在航空航天、汽车制造、电子设备等领域均有成熟的应用。以航空发动机为例,其旋转零件对精度要求极高,任何轻微的跳动都可能导致振动、噪音、效率下降,甚至事故。在这一领域,通常采用光学和电磁检测相结合的方式,以确保螺旋桨、涡轮等组件的稳定性。
在汽车制造中,轮毂和轴承的跳动检测至关重要,其直接关系到车的行驶平稳性和乘坐舒适性。现代汽车生产线已经普遍装备了自动化的跳动检测仪器,在装配线上实时检测各个关键零部件,确保产品出厂即符合质量标准。
未来发展趋势
随着工业4.0和智能制造的推进,跳动检测技术也朝着数字化、智能化的方向发展。未来的检测系统将更加注重与大数据、人工智能相结合,通过对海量检测数据的分析和建模,实现更加精准的预测和问题解决。
同时,便携式和移动式检测设备的开发也在加速。这样的设备不仅能提供现场实时检测,还能通过无线通讯与中央系统进行数据上传和分析。这将极大提高工业设备的维护效率和生产柔性,应对日益增长的智能制造需求。
总结而言,通用零件跳动检测作为现代工业检测的重要环节,其重要性不容忽视。随着技术的进步和工业需求的变化,我们有理由相信这一领域将在未来拥有更加广阔的发展前景。
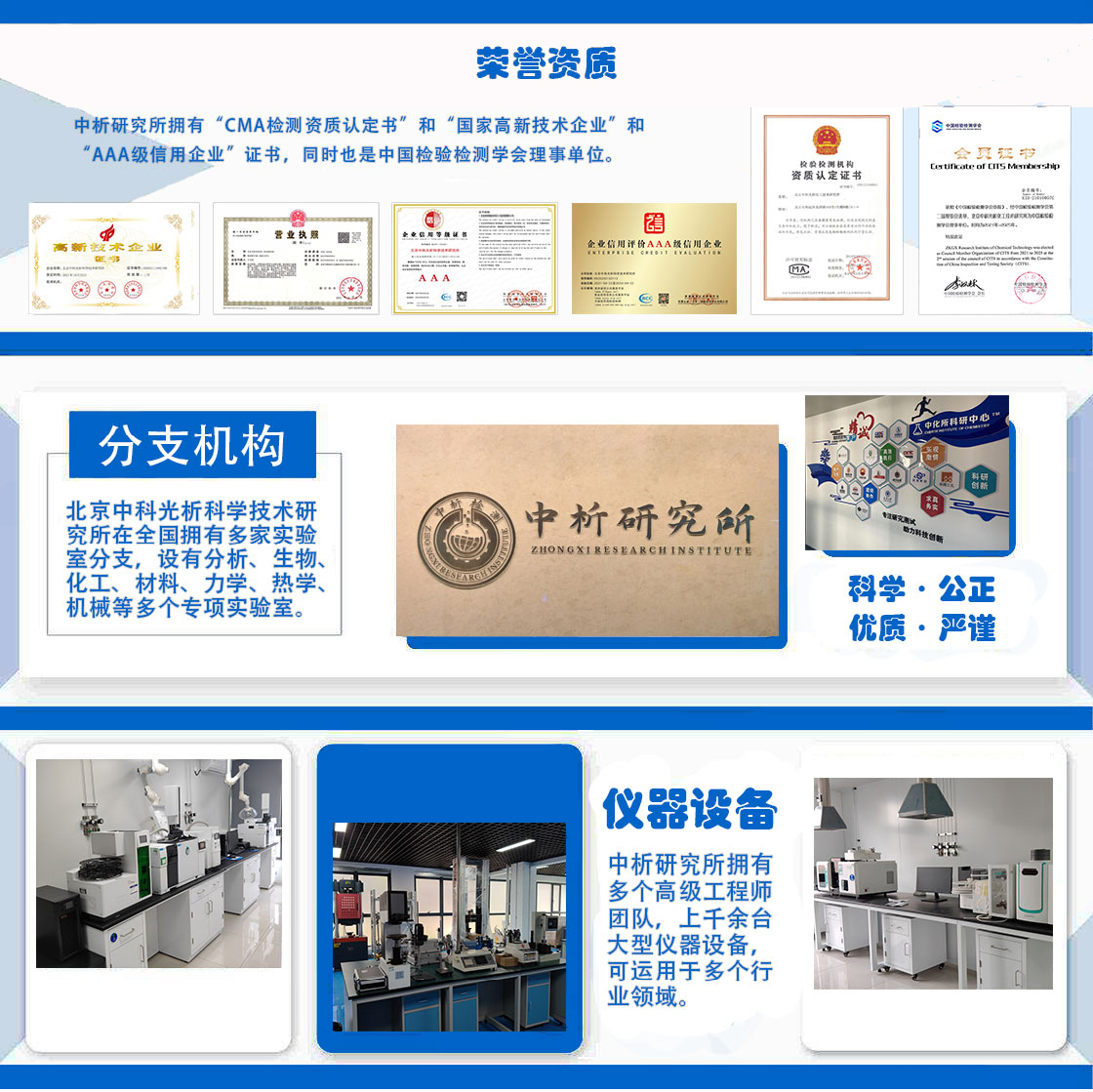
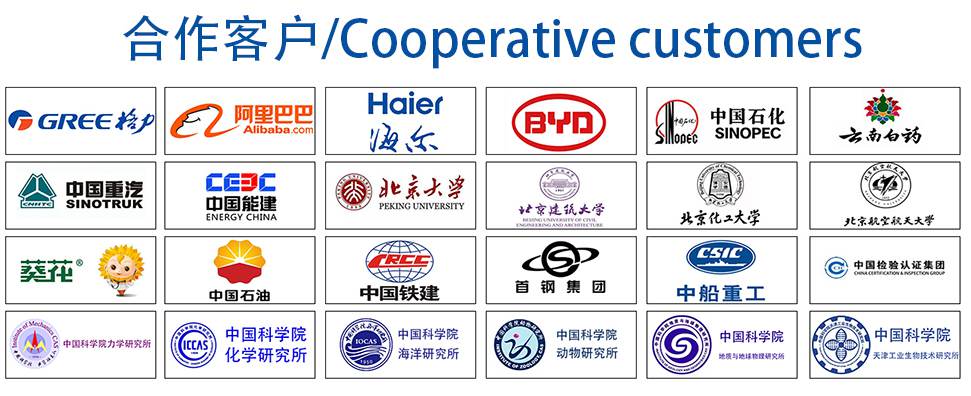