通用零件同轴度检测
通用零件及其重要性
在现代制造业中,通用零件的应用已成为不可或缺的一部分。通用零件通常指的是那些可以广泛应用于不同机械装置或设备中的元件,如螺丝、螺母、轴承、齿轮等。这些零件经过标准化设计和批量生产,具有成本低、易于采购、质量稳定等优点,使得设备的设计、生产和维护更加便捷。
然而,尽管通用零件在制造业中被频繁使用,其精度要求却不容忽视。尤其是在高精密设备中,部件之间的配合精度直接影响到设备的整体性能和使用寿命。因此,通用零件的检测,尤其是几何公差中的同轴度检测,就变得尤为重要。
同轴度的概念及其测量难点
同轴度是指在空间中两个或多个轴线的共线程度,即零件的回转轴线在规定的公差范围内对基准轴线的排布。它是机械零件的几何公差之一,对旋转件尤为重要。同轴度检测能够确保当零件安装到整机上时,能够平稳运行,不会出现偏心导致的振动或磨损问题。
对于通用零件而言,同轴度的检测可能看似简单,却因零件形状和尺寸的多样性而复杂化。测量同轴度的难点主要在于如何准确确定基准轴线,以及如何在多种工况下对零件进行精准测量。此外,由于加工误差、材料不均匀等原因,实物检测往往会遇到与理论设计不一致的难题。
通用零件同轴度的传统检测方法
传统的同轴度检测依赖于各种机械和光学仪器。这些仪器包括游标卡尺、千分表和圆度仪等。对于简单形状的零件,使用上述测量工具可以迅速得出相对准确的读数。游标卡尺和千分表可用来测量零件的尺寸数据,而圆度仪则能够检测零件的圆度和同轴度。
另一种常见方法是轴和套筒的转动对中法。在这种方法中,将零件安装在旋转工作台或主轴中。通过旋转零件,并在旋转过程中测量其偏离程度,来衡量零件的同轴度。这种方法适用于简单的圆柱形零件,但对于形状复杂的零件,测量精度和效率可能不够令人满意。
现代同轴度检测技术的应用
伴随着计算机技术和光学技术的发展,现代同轴度检测技术正在逐步取代传统技术。这些现代技术包括激光测量、视频测量技术以及三坐标测量机(CMM)的应用。
激光测量技术利用激光束的高精度和非接触特性,能够快速地检测出零件的同轴度。激光测量系统通过高频扫描方式获取一系列数据点,再通过计算机软件分析计算,得出同轴度误差。这种方法不仅速度快,而且对操作环境要求较低,适合大批量生产过程中的在线检测。
视频测量技术通过CCD摄像头获取零件表面的图像,利用图像处理技术对同轴度进行分析。视频测量系统具有操作简单、适应性广等优点,尤其适合于批量检测不同尺寸和形状的零件。
三坐标测量机通过探针接触零件表面,精确测量出零件的三维坐标数据,能在不接触零件的前提下评定其同轴度。CMM具有高精度、灵活多用的特点,适用于对精度要求极高的零件,但其成本往往也较为昂贵。
通用零件同轴度检测的未来趋势
随着技术的不断进步,未来的同轴度检测将朝着更加智能化和自动化的方向发展。智能检测系统将引入更多人工智能算法,以提高检测数据的分析精度和速度。实时监控系统和智能反馈系统的集成,将使得现场检测和品质控制更加便捷、高效。
同时,基于物联网的检测技术也将在未来获得应用。通过将通用零件的检测数据上传至云端平台,实现远程监控和大数据分析,这将极大提高企业的生产效率和质量管理水平。
结语
通用零件的同轴度检测是制造业精密控制中的重要环节。无论是传统方法还是现代技术,各有其适用之处和优缺点。在科技飞速发展的今天,敏锐地利用新技术并不断优化生产流程,将使企业在竞争中处于优势地位。面对未来,只有不断创新和进取,才能提高制造业的精度水平,推动行业向更高层次发展。
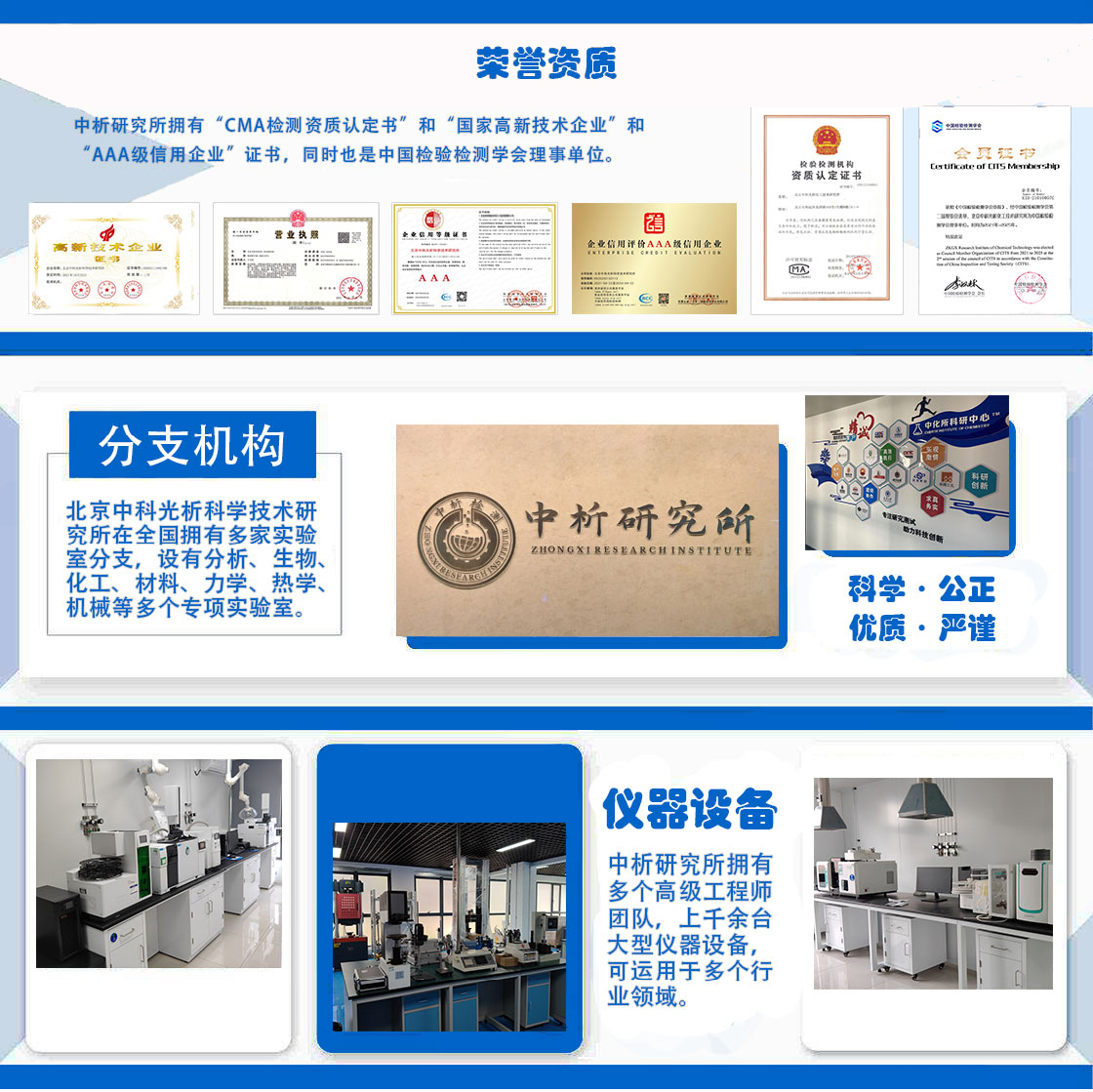
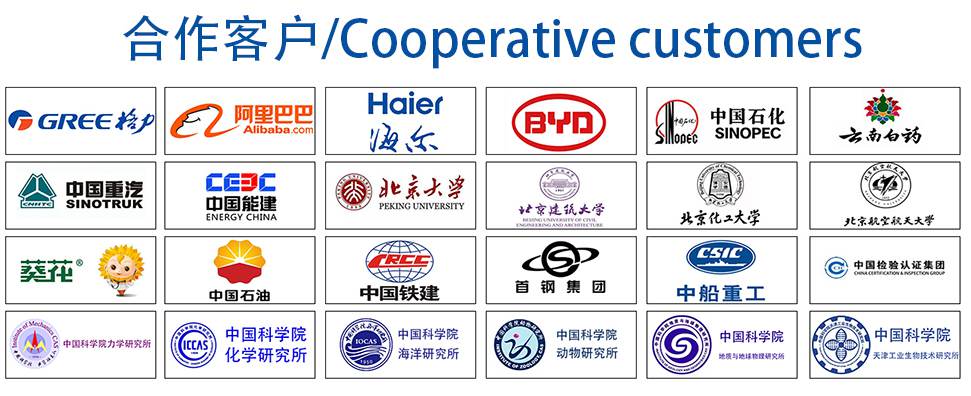