通用零件圆度检测
引言
在现代制造业中,零件的质量直接影响产品的整体性能和使用寿命。尤其是在高精度要求的行业,如航空航天、汽车制造以及医疗设备,零件的几何形状必须严格符合设计标准。其中,圆度是一个极为重要的几何参数,它直接关系到零件的配合性能、运转平稳性以及耐磨性。因此,圆度检测成为确保零件合格性的重要环节。
圆度的定义及其重要性
圆度是描述零件圆形轮廓度量的一种几何特性。理想的圆度是一个在二维空间中,由某一中心点至边缘半径都相等的曲线。然而,在真实的制造过程中,由于设备精度、材料特性、加工手段等多种因素的影响,实际的工件常常偏离理想圆形。因此,需要通过圆度检测来评估工件的偏离程度,以确保其在装配和运转中的可靠性。
圆度不仅影响零件的配合和装配精度,还会影响润滑效果,进而影响零件的寿命。例如,在汽车的发动机活塞中,圆度不良可能导致摩擦增加,进而影响发动机效率和油耗。而在轴承中,圆度不足可能会导致运转不平稳,产生振动和噪音。因此,精准的圆度测量是提高零件质量的重要环节。
圆度检测的原理和方法
目前,圆度检测的主要方法可以分为接触式和非接触式两大类。接触式方法主要包括使用圆度仪测量,非接触式则包括光学测量和激光扫描等技术。
圆度仪是最常用的接触式测量工具,其工作原理是将被测零件放置在仪器的旋转工作台上,通过高精度探头检测其外轮廓,从而确定圆度误差。这种方法的优点是精度高,适用于各种尺寸的圆形工件,但缺点是需要直接接触工件,可能对表面产生影响。此外,测量过程中需要保持探头与工件之间的接触稳定,使得操作相对复杂。
非接触式方法则利用光学和激光技术,通过反射、折射等原理来测量工件的外轮廓。这种方法的优点是不会对工件表面造成影响,同时可以快速测量多个点位,提高检测效率。但其缺点是对于高反光或透明材料,测量结果可能受到干扰,需要进行复杂的数据处理和校准。
圆度检测的实际应用
在实际生产中,圆度检测广泛应用于各种零部件的质量控制。以下是一些典型行业中的应用案例:
1. **汽车制造**:在发动机活塞环、连杆等零件的加工中,圆度直接影响发动机的密封性和动力性能。通过圆度检测,可以确保这些关键零件在装配过程中能够紧密配合,从而保证发动机的效率和耐用性。
2. **航空航天**:用于航空发动机的旋转零件,如涡轮盘和压气机叶片,其圆度直接关系到飞行的安全性和燃油效率。高精度的圆度检测可以提高这些零件的加工精度,降低安全风险。
3. **医疗器械**:在制造例如人工关节、心脏支架等精密医疗器械时,圆度控制是确保生物相容性和功能性的重要方面。准确的圆度检测可以提高产品的性能和患者的舒适度。
未来的发展方向
随着科技的进步,圆度检测技术也在不断发展。高精度、高效率的检测手段成为业界追求的目标。未来,随着自动化和智能化技术的普及,圆度检测将朝着在线检测和实时监控的方向发展。
一方面,**信息技术**的应用可以实现检测数据的即时分析和反馈,提高生产过程中的响应速度。通过与生产设备的联动,可以实现零件缺陷的自动识别和分类,为质量控制提供更为精准的依据。
另一方面,**人工智能**和**机器学习**技术的介入,使得检测系统可以自我学习和优化,通过大量数据的积累,逐步提高检测的准确性和可靠性。此外,结合**3D打印**技术,可以在加工过程中同时进行圆度测量,实现制造和检测的一体化。
结论
综上所述,圆度检测是现代制造业中至关重要的一环。通过科学的方法和齐全的技术,可以有效保证零件质量,提高产品性能和可靠性。随着检测技术的不断创新,未来的圆度检测将更加智能化和自动化,为工业生产带来革命性的变化和提高。做好圆度检测,不仅是提升企业竞争力的关键,也是确保产品安全性和耐用性的基本保障。
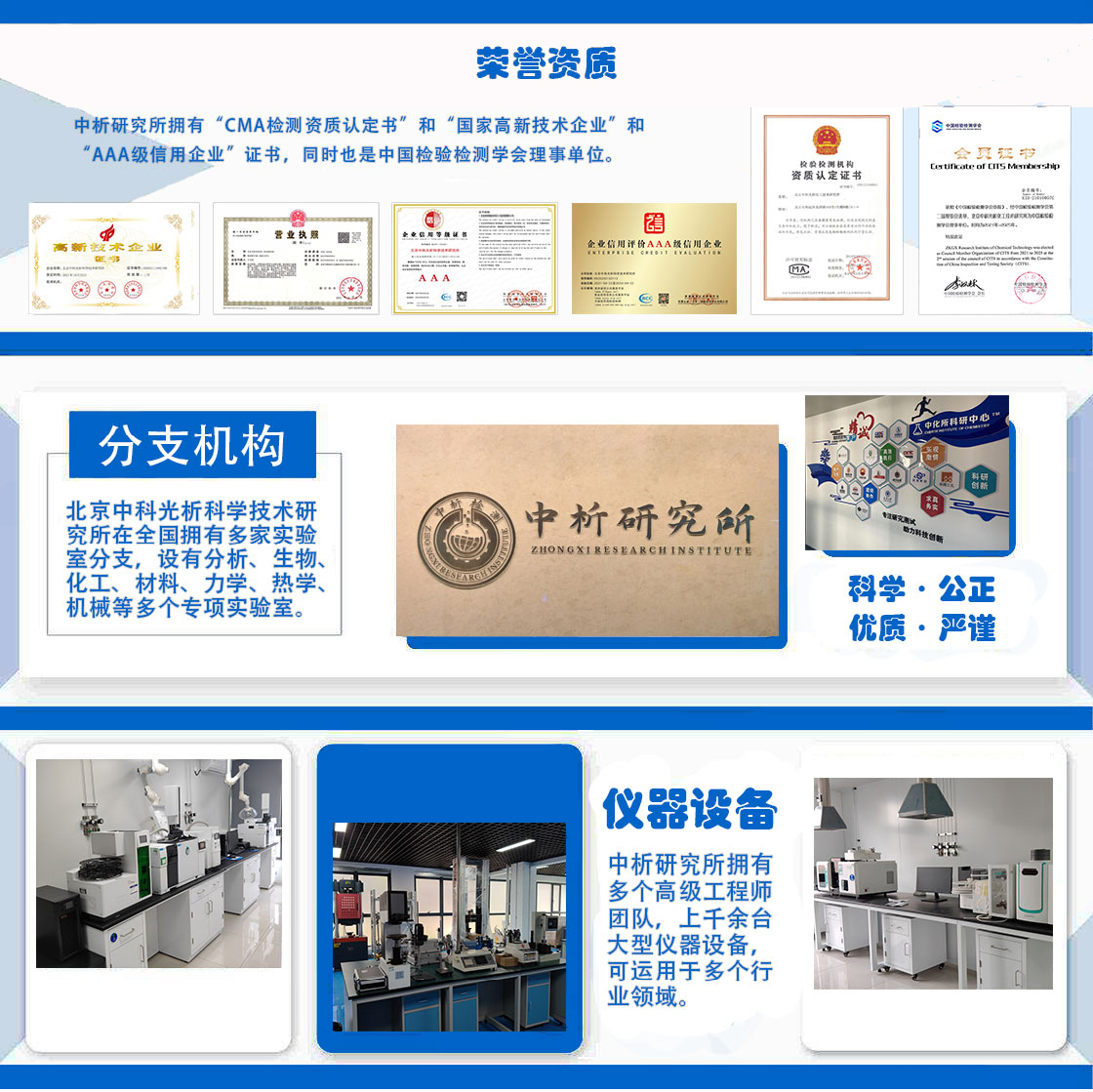
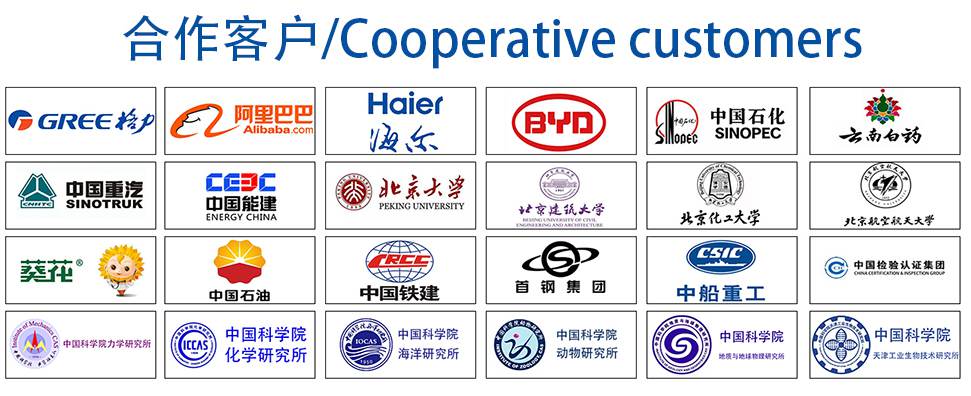