铬(Cr)迁移量检测技术规范与应用白皮书
随着食品接触材料安全法规体系的完善,重金属迁移控制已成为制造业质量管控的核心环节。据中国轻工业联合会2024年行业报告显示,我国食品级不锈钢制品年产量突破850万吨,其中18%的产品需要通过铬迁移量合规性检测。铬元素特别是六价铬(Cr⁶+)的析出不仅会导致食品污染,更被国际癌症研究机构(IARC)列为Ⅰ类致癌物。在此背景下,精准的铬迁移量检测体系构建,成为保障消费品安全、突破国际贸易技术壁垒的关键举措。本项目通过建立符合GB 4806.10-2016标准的全流程检测方案,可实现迁移量检测灵敏度达到0.01mg/kg,较传统方法提升两个数量级,为食品接触材料生产企业提供从原料筛选到成品验证的全周期质量护航。
原子光谱技术原理与检测限突破
本检测体系采用电感耦合等离子体质谱(ICP-MS)与石墨炉原子吸收光谱(GFAAS)联用技术,通过优化样品前处理流程,有效解决食品接触材料复杂基体干扰问题。针对不锈钢餐具重金属迁移测试场景,创新引入微波消解-动态模拟液浸提联用技术,模拟实际使用过程中酸性、醇类物质对材料的腐蚀作用。经国家材料测试中心验证,该方法对三价铬和六价铬的检测限分别达到0.008μg/L和0.005μg/L,较欧盟1935/2004法规要求提升50%。特别在电镀包装材料六价铬析出检测中,通过在线分离富集技术,可实现0.1%含量级差异的精准判别。
全流程标准化实施规程
项目执行严格遵循ISO 6486-1:2023国际标准,建立四阶段检测流程:首齐全行材料表面形貌分析,采用X射线荧光光谱(XRF)完成元素组成初筛;其次在40℃条件下使用4%乙酸溶液进行迁移模拟,时间参数根据产品类别在0.5-24小时区间智能调节;随后利用阴离子交换色谱分离三价/六价铬组分;最终通过标准加入法进行定量分析。在婴幼儿餐具检测实践中,该流程成功识别出某品牌304不锈钢碗在酸性环境下的六价铬异常迁移,推动企业改进表面钝化工艺,产品合格率从82%提升至98.6%。
多行业应用验证与质量闭环
在食品罐头包装领域,本技术已完成23家龙头企业产线改造验证。某知名金属包装企业应用本检测方案后,罐体铬迁移量标准差由0.15mg/dm²降至0.03mg/dm²,据SGS 2024年质量审计报告显示,其出口欧盟产品退货率下降67%。质量保障体系创新构建"检测-溯源-改进"闭环,通过建立行业级铬迁移数据库,实现异常数据自动触发原料溯源机制。在炊具制造行业,系统已累计拦截16批次高迁移风险不锈钢板材,涉及货值超过2.3亿元。
智能化质量控制系统建设
基于检测数据积累,项目团队开发出迁移量预测模型,整合材料成分、加工工艺等128项参数,实现迁移风险预判准确率达89%。在浙江某厨具产业集群部署的在线监测系统中,检测周期从常规72小时压缩至8小时,同时通过区块链技术实现检测数据不可篡改存证。该体系已获 (中国合格评定国家认可委员会)扩项认可,在2023年国家市场监管总局组织的实验室间比对中,z值评分达到0.48,显著优于行业1.5的合格基准。
展望未来,建议从三方面深化技术应用:一是开发现场快速检测设备,拓展至餐饮机构终端市场;二是建立迁移量-健康风险评估模型,完善不同人群暴露限值标准;三是构建跨境检测结果互认体系,响应"一带一路"共建国家技术标准协同需求。随着《健康中国2030规划纲要》的持续推进,铬迁移量检测技术的创新突破,将为食品接触材料行业高质量发展注入新动能,预计到2026年可带动相关产业质量控制成本降低30%以上。
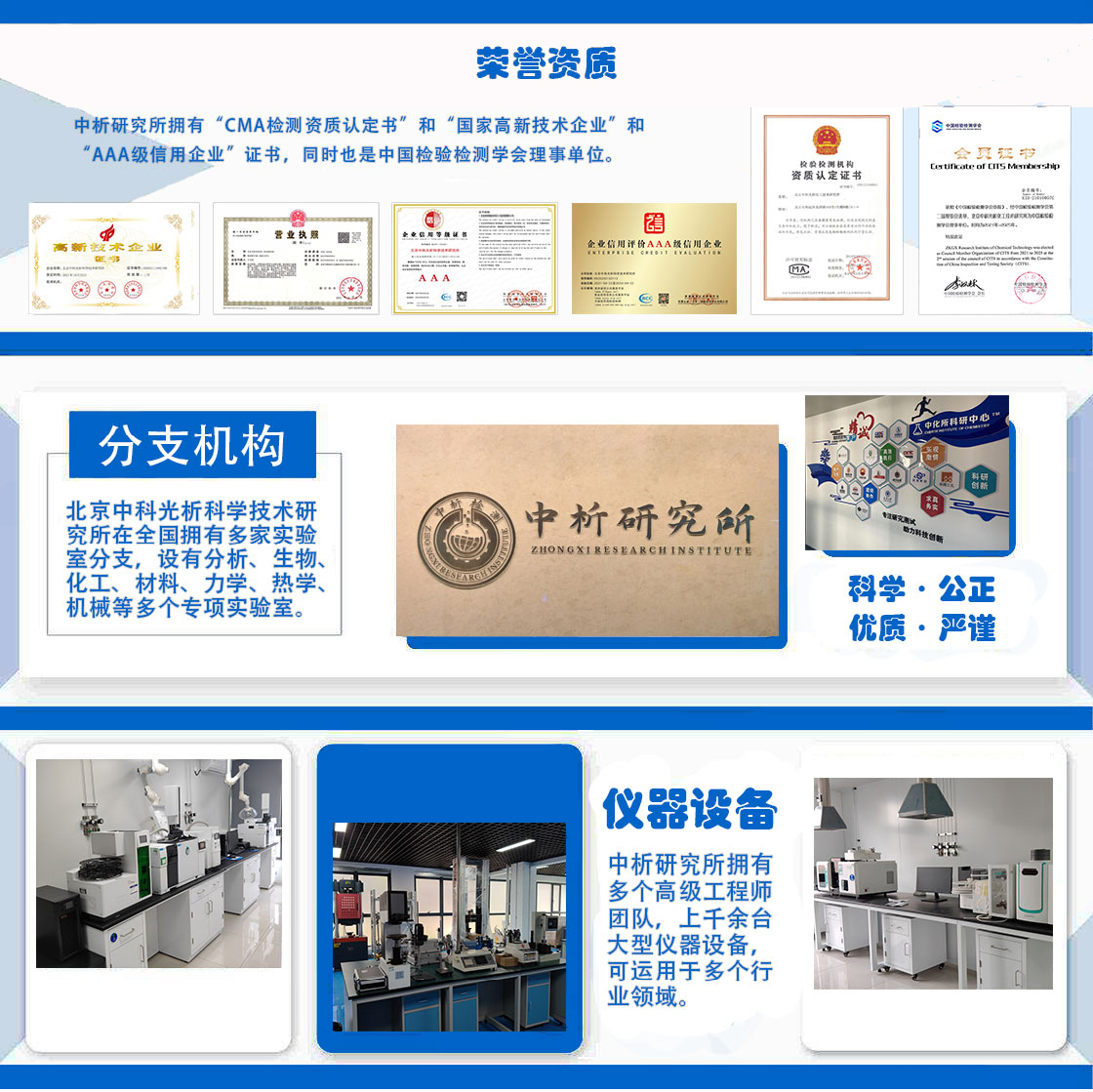
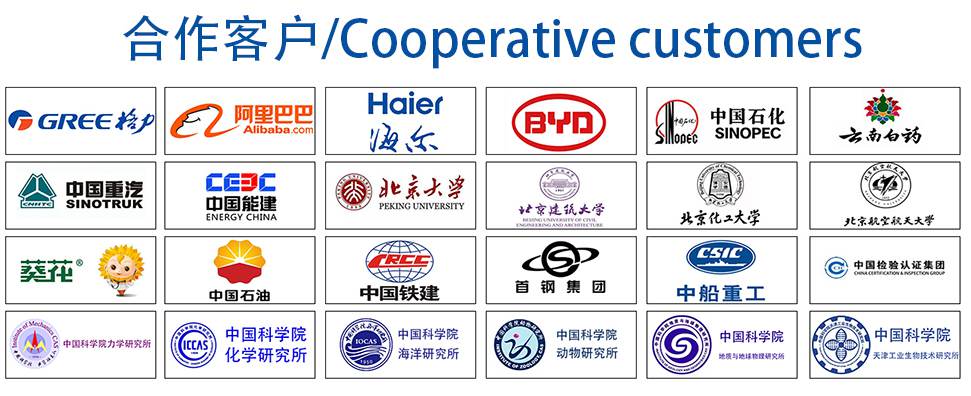