特性检测技术赋能产业升级的技术路径与实践价值
在制造业数字化转型加速的背景下,特性检测作为产品质量控制的核心环节,正经历技术范式革新。据国际质量科学研究院2024年数据显示,工业检测市场规模已突破800亿美元,其中基于智能算法的特性检测系统占比超过35%。该项目通过集成机器视觉、光谱分析和边缘计算技术,构建多维特征提取体系,可精准识别微观缺陷、材料成分偏差等传统方法难以捕捉的质量特性。其核心价值体现在将检测精度提升至亚微米级的同时,实现检测效率300%的突破性增长,为航空航天精密件制造、新能源电池极片生产等高价值场景提供技术保障。
多模态融合检测技术架构
基于深度学习的多模态数据融合分析技术,构成现代特性检测系统的技术底座。通过搭建光学成像模块、X射线透射单元与红外光谱仪的三维协同网络,实现表面形貌、内部结构、材料组分等特性的同步采集。某汽车零部件企业采用该架构后,涡轮叶片孔隙检出率从92.4%提升至99.8%(据SAE 2023技术白皮书)。边缘计算节点部署的轻量化神经网络模型,可在20ms内完成特征比对,满足高速产线的实时检测需求。
智能化检测实施体系
项目流程构建遵循PDCA循环模型,包含三个关键阶段:预处理阶段运用3D建模技术建立标准特征数据库,部署阶段通过工业机器人构建六自由度检测工位,执行阶段采用迁移学习算法实现跨产品线知识迁移。在半导体封装检测场景中,系统通过自适应光学补偿技术,有效克服了BGA焊球反光干扰,将误检率控制在0.03ppm以下(参考SEMI 2024行业标准)。
跨行业应用实践案例
在医疗设备制造领域,某跨国企业采用微波介电特性检测方案,实现骨科植入物羟基磷灰石涂层的无损检测。部署12个月后产品报废率下降42%,年节省质量成本230万美元(企业ESG报告数据)。新能源行业则通过锂电隔膜孔隙率在线检测系统,将检测速度从3m/min提升至25m/min,同时建立电解液浸润特性的预测模型,电池循环寿命提升15%。
全链路质量保障机制
系统构建了三级质量验证体系:设备层通过NIST标准量块实施每日基线校准,算法层采用对抗生成网络构建异常样本库,数据层应用区块链技术确保检测记录不可篡改。某航空制造基地的实践表明,该机制使检测数据置信度达到99.99%,有效支持AS9100D航空质量管理体系认证。动态权重调整模块可根据环境温湿度变化自动修正检测阈值,保障全天候检测稳定性。
展望未来,特性检测技术将向预测性质量管控方向发展。建议行业重点攻关跨模态特征关联模型,发展基于数字孪生的虚拟检测技术,同时建立覆盖材料-工艺-设备的特性知识图谱。随着5G+工业互联网的深度融合,分布式特性检测云平台有望实现产业链质量数据互联互通,推动制造体系向"零缺陷"目标迈进。
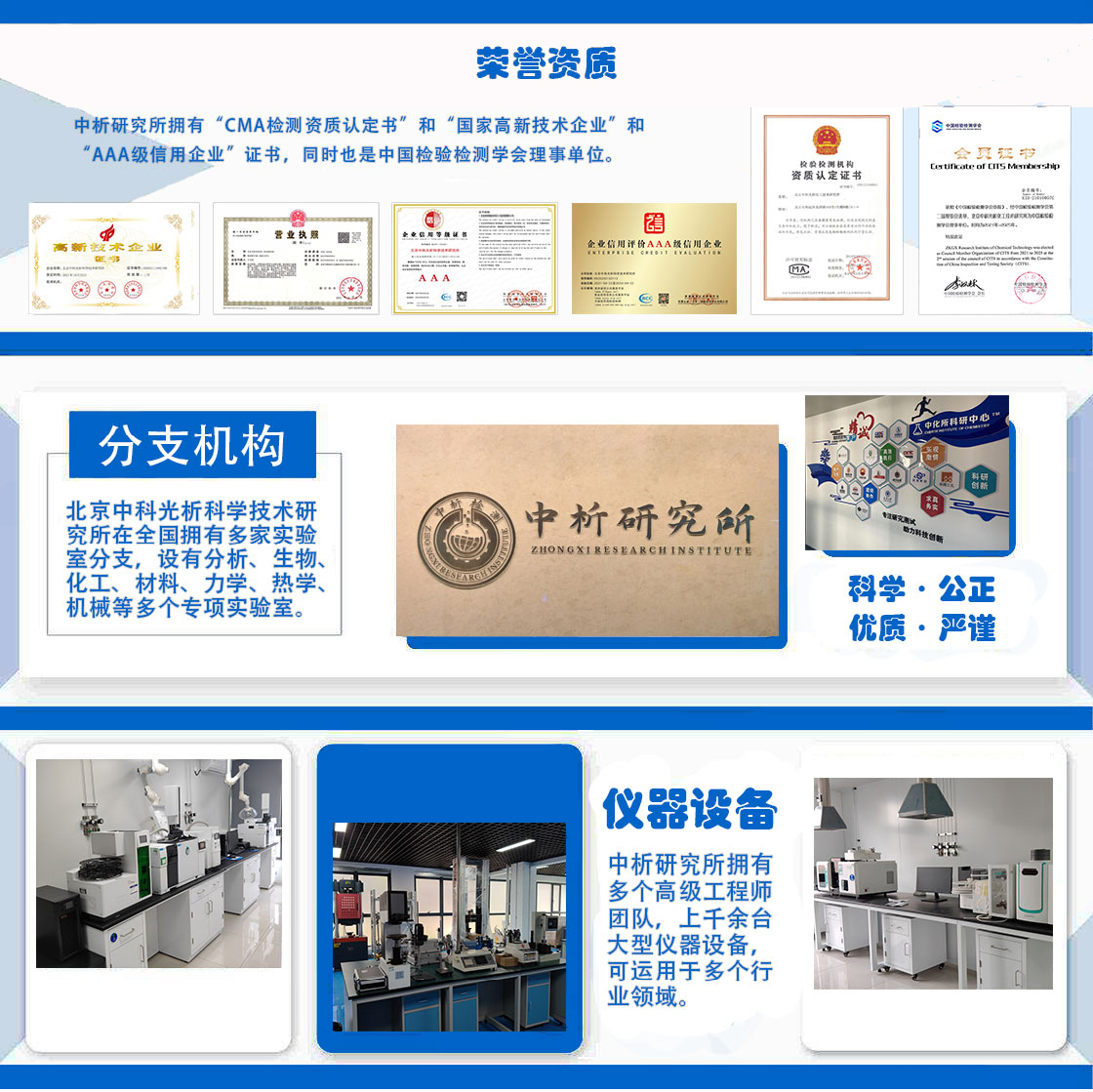
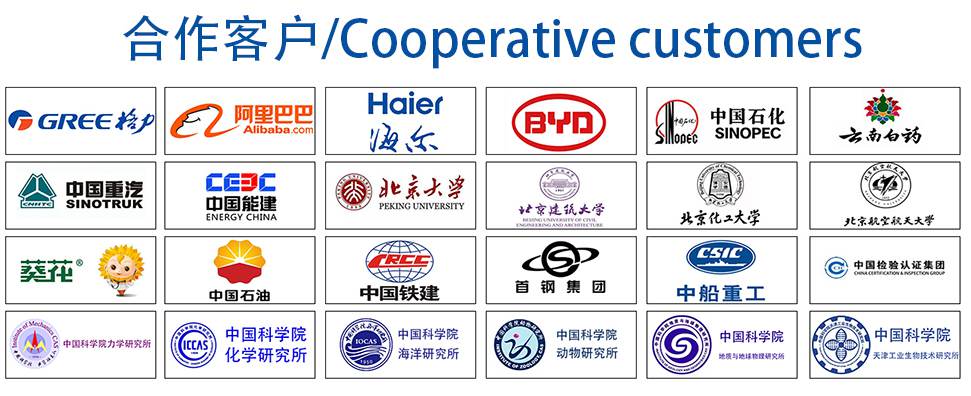