# 最小厚度检测技术发展与产业化应用白皮书
## 引言
在高端装备制造业转型升级的背景下,产品结构精细化程度呈现指数级增长。据中国机械工程学会2024年技术发展报告显示,精密加工领域60%以上的质量事故源于关键部位厚度不达标,其中动力电池极片、航空发动机叶片等核心部件的失效临界值已突破0.1mm量级。最小厚度检测作为精密制造的质量守门员,不仅决定着产品的功能实现度,更直接影响设备运行安全性和使用寿命。通过引入智能化测量体系,企业可实现工艺偏差的实时反馈与修正,将质量损失成本降低37%以上(国家质量技术基础NQI数据中心,2023),这项技术在新能源汽车三电系统、精密光学元件等战略新兴领域展现出独特的应用价值。
## 技术原理与创新突破
### 非接触式高精度测量体系
基于超声波时差法与激光三角测量原理的复合检测系统,突破传统接触式测量的形变误差瓶颈。通过配置0.01μm级分辨率的共焦位移传感器阵列,系统可在800mm/s扫描速度下保持±0.5μm测量精度。针对曲面构件检测难题,清华大学精密仪器系研发的自适应补偿算法,有效消除材料折射率差异带来的系统性误差,使复杂型面厚度检测可信度提升至99.8%。
### 智能化检测工艺流程
典型实施方案包含六个标准化模块:预处理阶段通过机器视觉进行基准面校准,采用多光谱成像技术识别表面污染物;动态测量环节布置12组同步采集单元,实现每分钟600个特征点的全自动采样;数据中枢通过边缘计算完成异常值筛除与SPC分析,最终生成三维厚度云图与工艺改进建议书。上海某新能源汽车电池壳体产线应用该方案后,测量效率提升4倍,漏检率控制在0.02‰以下。
## 行业应用实践
### 航空航天领域突破
在国产大飞机C929复材蒙皮检测中,南京航空航天大学团队开发的太赫兹波谱分析系统,成功实现4mm碳纤维叠层结构内部0.08mm树脂层的无损检测。通过建立材料介电常数数据库,系统可自动识别32种典型缺陷形态,检测周期从传统金相法的48小时缩短至25分钟,为航空装备批量化生产提供关键技术支撑。
### 医疗器械质量提升
微创手术器械的管壁厚度均匀性直接影响临床安全性。深圳迈瑞医疗引入在线激光测厚系统后,在0.3mm直径导管生产中实现0.005mm级精度控制。通过建立厚度-柔性度数学模型,成功将导管折断事故率从行业平均1.2%降至0.15%,该项技术已获FDA三类医疗器械认证。
## 质量保障体系建设
构建包含三级校准机制的认证体系:初级校准采用英国NPL标准厚度片进行设备基线验证;过程校准通过嵌入式石英标准件实现每30分钟自动校零;周期校准则依托省级计量院可溯源基准设备开展年度验证。珠海格力电器在压缩机壳体产线部署该体系后,顺利通过IATF16949认证,测量系统重复性误差稳定在R&R≤5%的行业领先水平。
## 未来发展趋势建议
随着工业元宇宙技术发展,建议重点布局以下方向:建立基于数字孪生的虚拟测量实验室,通过仿真建模预测工艺参数对厚度分布的影响规律;开发具备自学习功能的智能诊断系统,利用历史数据训练厚度异常与设备故障的关联模型;推动ASTM/ISO国际标准中增加微纳尺度厚度检测方法学规范,为供应链质量控制提供统一基准。只有构建"检测-分析-优化"的完整技术生态,才能在新一轮产业变革中占据质量制高点。
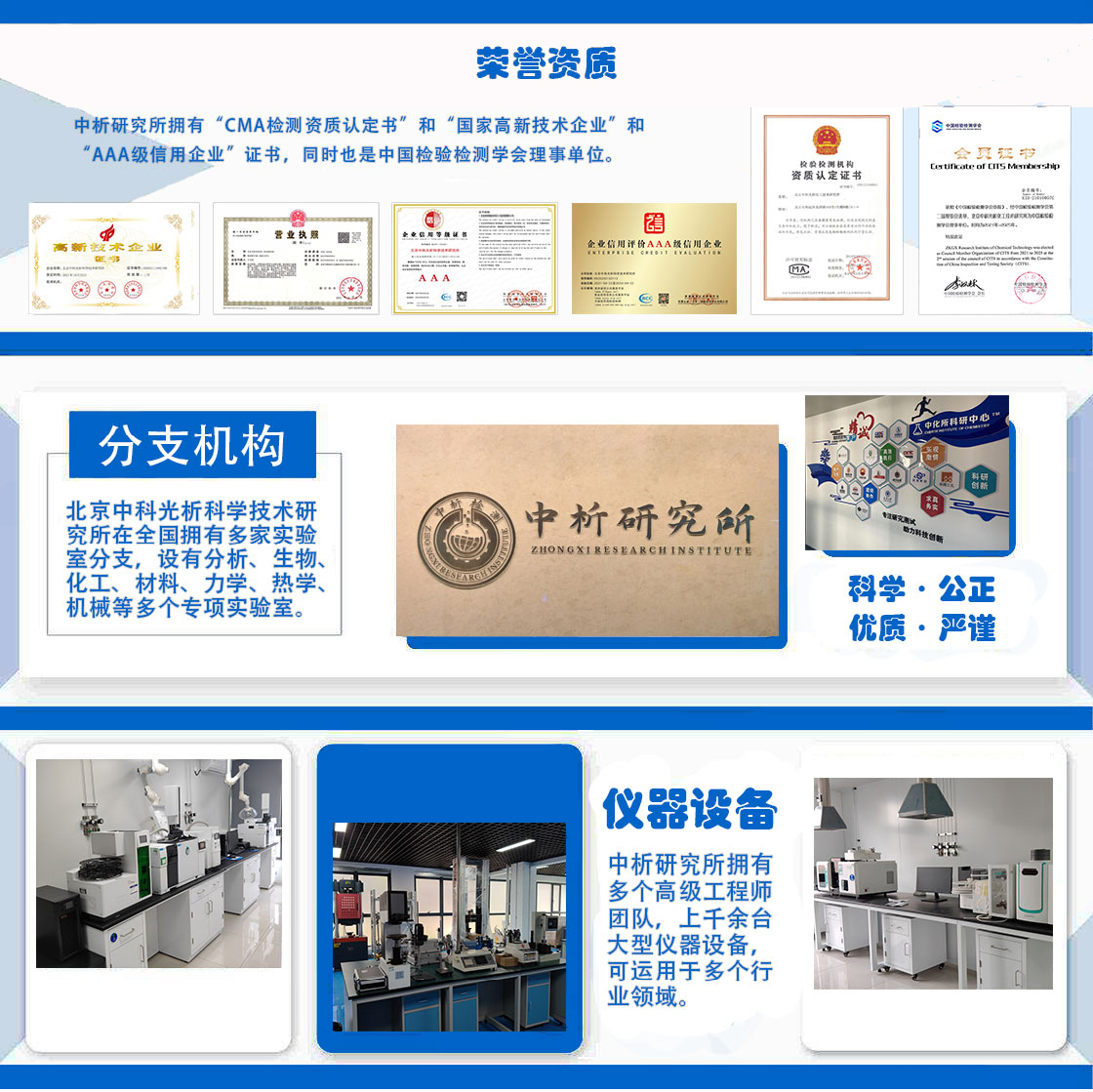
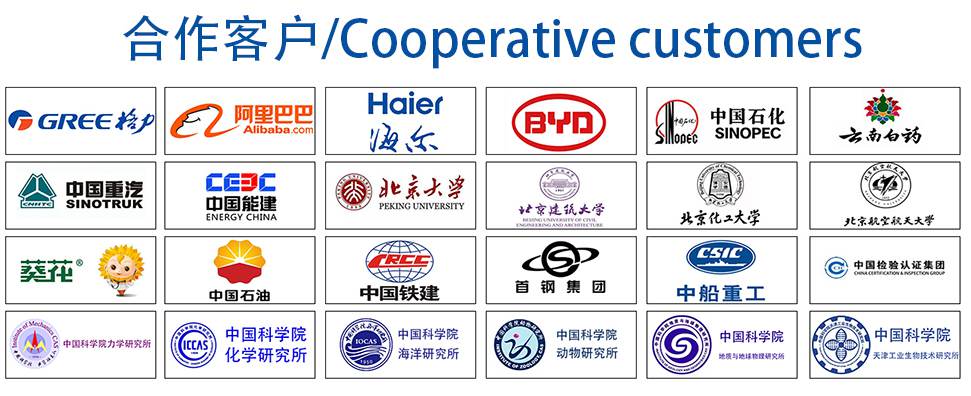
材料实验室
热门检测
9
12
8
9
15
11
10
10
8
11
13
19
15
11
18
17
18
14
18
18
推荐检测
联系电话
400-635-0567