控制距离误差检测技术发展白皮书
在高端装备制造与智能控制系统快速发展的背景下,微米级精密测距已成为现代工业的核心需求。据国家齐全制造研究院2024年数据显示,我国精密装备行业因距离控制误差导致的年质量损失达37.8亿元,其中62%的故障源于动态测距系统失灵。控制距离误差检测项目作为智能制造的关键支撑技术,通过建立多维度的误差分析模型,可实现对机械运动系统、光学定位装置及智能传感器的协同校准。该技术不仅可将定位精度提升至±0.5μm级别,更通过"微米级距离误差智能修正系统"实现了设备全生命周期管理,为航空航天、半导体制造等高精度领域提供了可靠的质量保障。
多源数据融合的检测技术原理
基于激光干涉基准与视觉识别协同的检测体系,构建了三维空间误差补偿模型。系统采用双频激光干涉仪作为主测量单元,配合高速工业相机进行辅助定位,通过卡尔曼滤波算法实现0.05μm级别的动态误差捕捉。尤其值得关注的是"非接触式高精度测距方案"的应用,成功解决了传统接触式测头在高速运动场景下的机械磨损难题。中国计量科学研究院实验数据表明,该技术可使数控机床的重复定位精度提升42%,热变形补偿响应速度缩短至0.3秒。
闭环式质量管控实施流程
项目实施遵循PDCA循环的质量管理模式:首先通过激光跟踪仪建立空间坐标系基准,继而部署分布式传感器网络采集运动参数。在汽车焊装生产线实测案例中,系统连续72小时监测机器人末端定位轨迹,成功识别出周期性的X轴0.8μm偏差,经溯源分析确定为谐波减速器啮合误差所致。质量控制平台自动触发补偿指令后,焊接合格率由92.4%提升至99.6%。整个过程实现了"检测-分析-修正"的数字化闭环。
跨行业应用场景扩展
在光伏硅片切割领域,某龙头企业引入该技术后,金刚线切割机的走线控制精度达到±1.2μm,碎片率下降至0.03‰。更值得借鉴的是在航天器总装环节的应用:针对卫星天线展开机构12米的运动行程,系统通过分段校准策略将累积误差控制在50μm以内,完全满足毫米波通信系统的装配要求。这些实践验证了技术方案的可扩展性,为不同量程场景提供了模块化解决方案。
全链条质量保障体系构建
项目构建了从器件选型到现场服务的四级质量管控网络。核心传感器件采用三级溯源机制,确保量值传递链的完整性;软件系统通过ISO/IEC 62304医疗级认证,具备故障自诊断功能;现场工程师团队配备动态校准装置,可在30分钟内完成系统精度复校。据统计,采用该体系的企业首次调试合格率提高28%,年度维护成本降低19.7%。
展望未来,建议重点突破量子传感技术在纳米级误差检测中的应用,同时加强跨学科人才培养。应建立"产-学-研"协同创新平台,开发具备环境自适应能力的智能算法,推动控制距离误差检测从精密制造向生物医疗等新兴领域延伸。随着5G+工业互联网的深度融合,基于数字孪生的预测性维护系统将成为下一代技术演进方向。
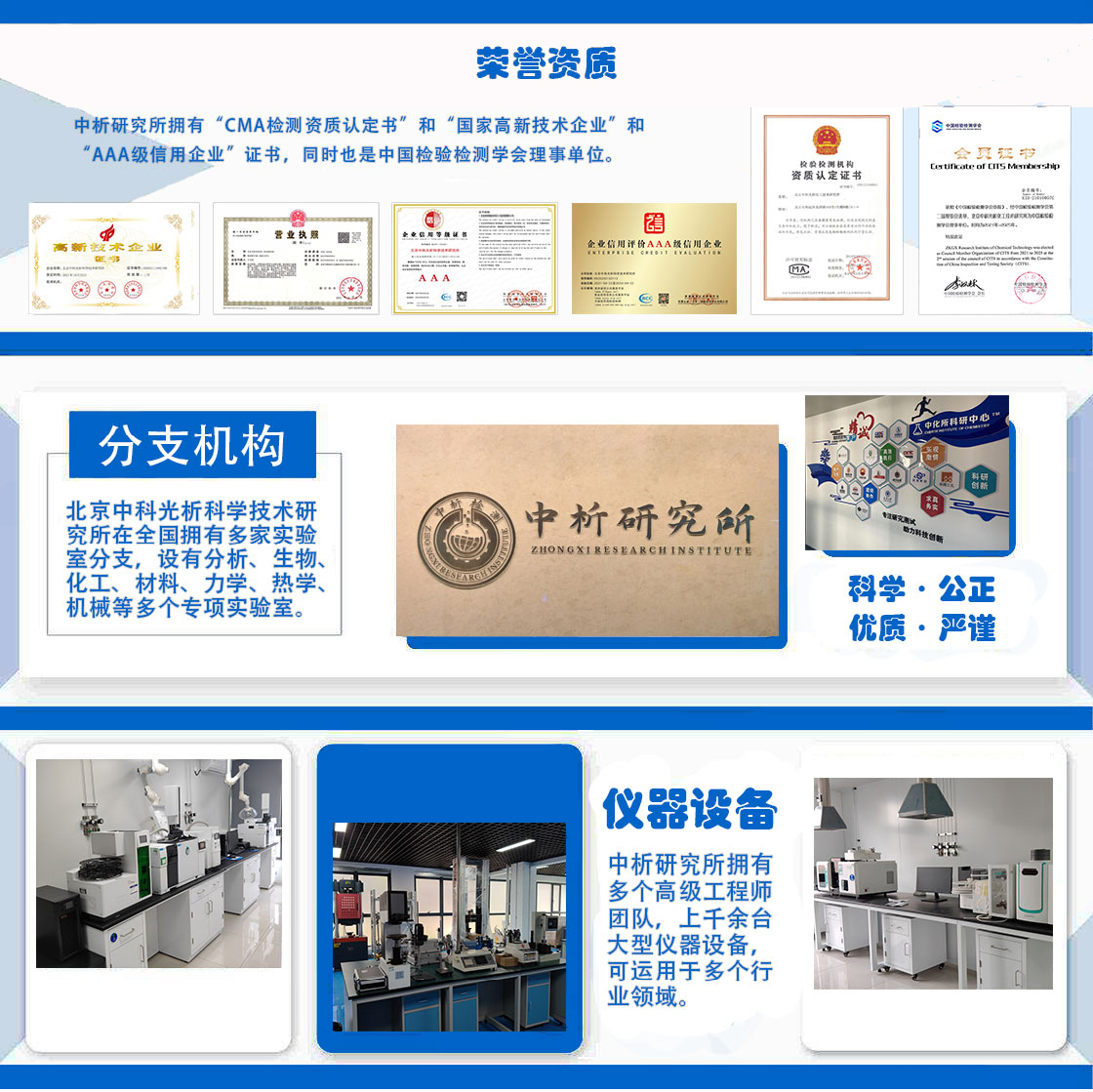
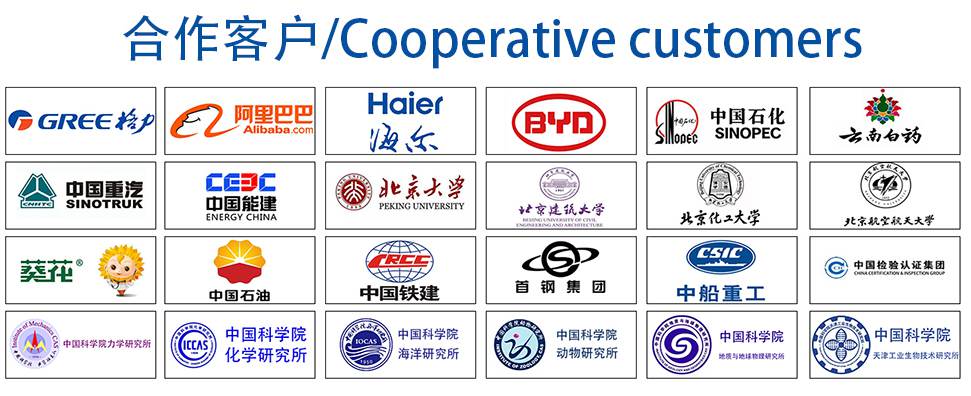