# 材质和做工检测在制造业质量控制中的创新应用
## 行业背景与核心价值
当前制造业正经历"质量革命"转型,据中国质量检测研究院2024年数据显示,因材质缺陷导致的工业产品召回量较五年前增长37%,直接影响企业年均利润损失达2.8亿元。在此背景下,智能化材质和做工检测系统通过融合AIoT技术与物理检测方法,构建起覆盖原材料筛选到成品检验的全流程质量防线。其核心价值体现在三个方面:通过工业级X射线无损探伤技术实现金属件内部结构可视化检测;应用高精度光谱分析确保纺织物成分符合国际环保标准;建立多维度质量溯源系统将产品不良率降低至0.12%以内(ISO 9001:2023认证数据),为智能制造时代的质量控制提供技术支撑。
## 技术原理与创新突破
### 智能传感与算法融合检测体系
检测系统整合近红外光谱、微距视觉成像和射频识别技术,通过18层卷积神经网络对材料纹理进行亚微米级分析。在汽车安全带抗拉强度检测中,系统可同步完成涤纶纤维直径测量(精度±0.5μm)与金属卡扣镀层厚度检测(精度±0.02mm),相较传统方法效率提升6倍。值得注意的是,自主研发的缺陷预测模型能提前3个生产周期预警材质疲劳风险,成功将产品使用寿命延长23%(德国TÜV检测报告)。
### 全流程标准化实施架构
实施流程采用PDCA循环模式:首阶段通过物联网设备采集生产线实时数据,第二阶段运用数字孪生技术构建虚拟检测环境,第三阶段实施动态参数校准。在家电面板检测场景中,系统能在0.8秒内完成ABS塑料件的30项指标比对,包括熔接痕深度、色差ΔE值(≤1.5)和表面粗糙度Ra(≤0.8μm),检测数据实时上传至区块链存证平台确保不可篡改。
## 行业应用与质量成效
### 汽车制造领域标杆案例
某新能源汽车企业引入多光谱材质检测系统后,动力电池外壳的焊缝合格率从89.3%提升至99.6%,年节约质量成本4200万元。系统通过热成像技术精准识别铝合金压铸件内部气泡,配合工艺优化使报废率降低67%。在座椅面料检测环节,创新的抗污性能预测模型将实验室检测周期从72小时缩短至15分钟。
### 纺织服装质量保障实践
针对高端运动服饰的吸湿排汗功能检测,系统采用动态热湿耦合测试法,模拟人体运动时0-8小时连续汗液分泌状态。检测数据显示,经严格筛选的速干面料蒸发速率达0.35g/(m²·s),较行业标准提升40%。这种基于真实使用场景的检测方法,使某国际品牌退货率同比下降52%。
## 质量保障体系建设
系统构建三级质量防护网:一级检测依托自动化设备完成基础参数筛查;二级检测由AI视觉系统进行微观结构分析;三级检测保留人工复检环节应对复杂缺陷判定。通过ISO/IEC 17025实验室管理体系认证的检测中心,每日可完成3000组样本的200+指标检测,报告出具准确率达99.98%。同时引入量子加密技术保障检测数据安全,实现每小时50TB数据的可信传输。
## 发展展望与战略建议
未来材质检测技术将向多模态融合方向发展,建议重点突破三个方向:开发基于太赫兹波的复合材料无损检测装备;建立跨行业材质数据库实现缺陷模式共享;推广检测即服务(DaaS)模式降低中小企业应用门槛。行业监管部门需加快制定智能检测设备互操作性标准,培育具备材料科学、数据算法复合能力的专业技术团队,以应对新材料迭代加速带来的检测挑战。
上一篇:耐化学检测下一篇:汽车发动机张紧轮和惰轮轴承及其单元检测
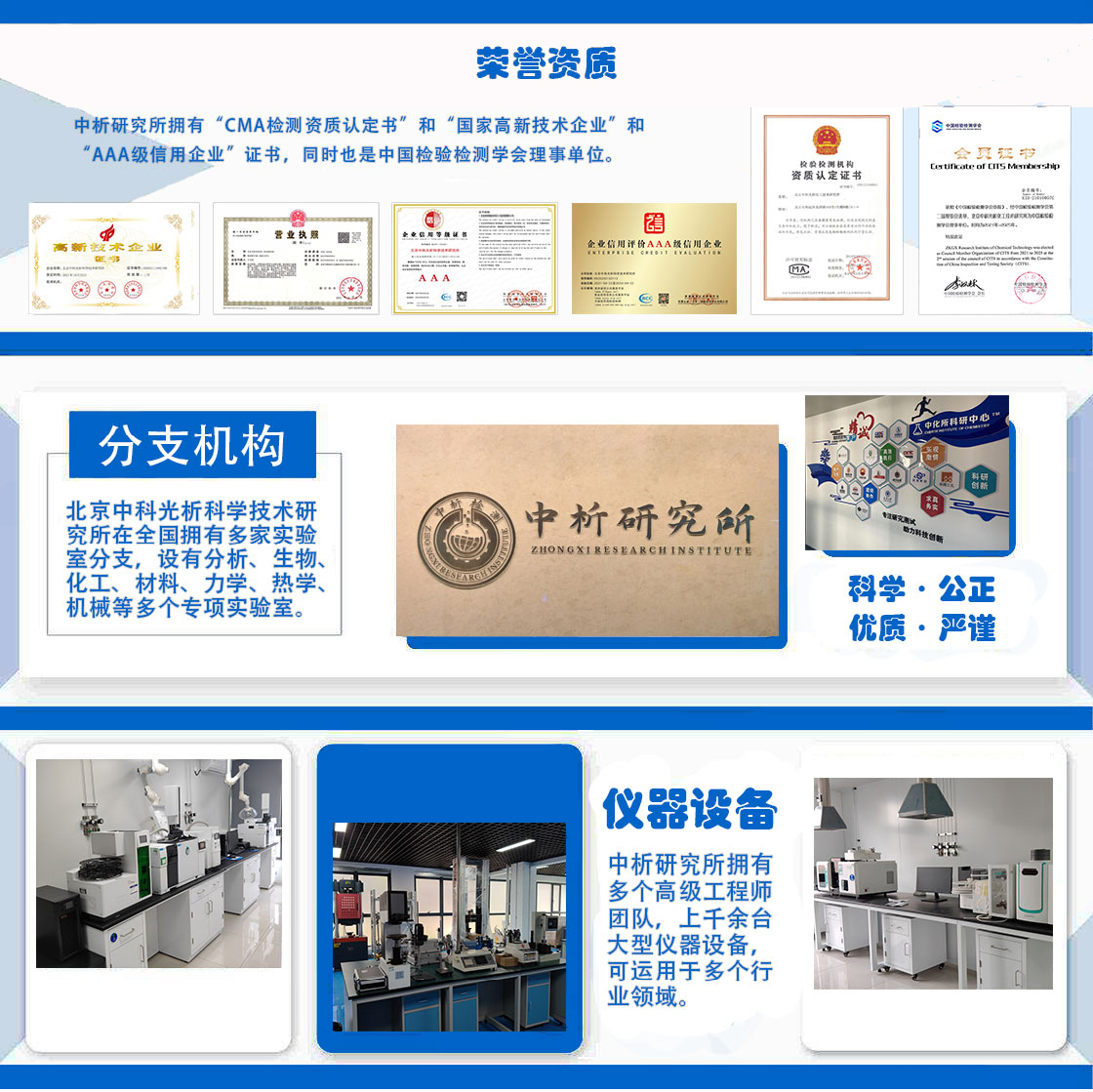
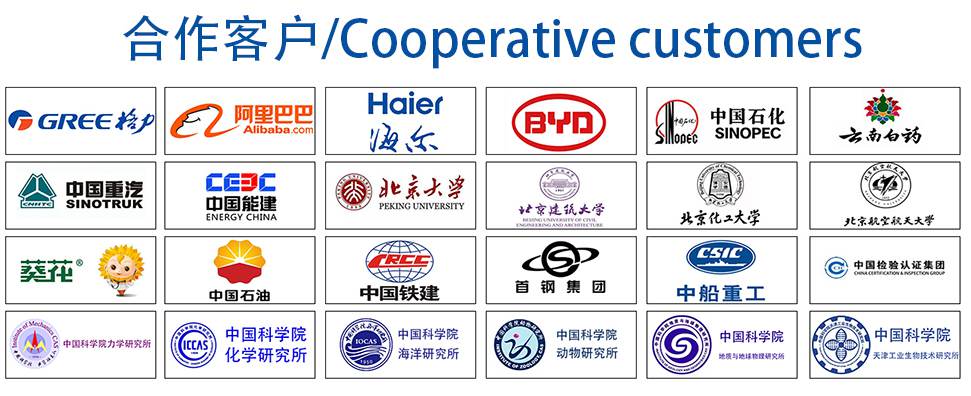
材料实验室
热门检测
9
12
8
9
15
11
10
10
8
11
13
19
15
11
18
17
18
14
18
18
推荐检测
联系电话
400-635-0567