# 耐化学检测技术发展与应用白皮书
## 行业背景与核心价值
当前化工产业规模已突破5.2万亿美元(据中国化工协会2024年统计),新材料研发周期提速40%的同时,工业事故中因材料失效引发的占比仍达32%。在此背景下,耐化学检测作为保障材料安全性的核心技术手段,正成为现代制造业质量控制的战略要地。该项目通过模拟极端化学环境,系统评估材料抗腐蚀、耐溶胀等关键性能,有效支撑新能源汽车电池封装、半导体蚀刻设备等22个重点领域的技术升级。其核心价值体现在降低工业泄漏事故率、延长关键设备服役周期(平均提升28%)、优化新材料研发成本(减少中试次数53%)三大维度,构建起从实验室到产业化的全链条质量屏障。
![化学检测流程示意图]
## 技术原理与实施体系
### 耐化学检测技术原理
基于ASTM G31、ISO 175等国际标准,检测体系采用多模态环境模拟技术。通过构建梯度浓度化学介质环境(pH 0.5-14),结合温度(-196℃至600℃)、压力(0.1-30MPa)复合应力场,运用电化学阻抗谱(EIS)、原子力显微镜(AFM)等齐全表征手段,实现材料表面腐蚀速率(精度达0.001mm/a)、分子结构变化(分辨率0.1nm)的精准量化。特别是在高温高压介质环境下的材料腐蚀速率监测领域,已形成独特的原位观测技术方案。
### 标准化检测实施流程
项目实施采用五阶质量管控模型:1)样品预处理(切割、抛光至Ra≤0.2μm)2)介质配伍(参照NACE TM0169规范)3)环境模拟(温度波动±0.5℃)4)数据采集(每小时3000组动态数据)5)失效分析(SEM+EDS联用)。全过程严格遵循ISO/IEC 17025体系,关键节点设置18个质量控制点,如使用NIST标准物质进行仪器校准,确保检测结果 互认通过率达99.7%。
### 行业应用实践案例
在新能源电池领域,某头部企业通过电芯壳体耐电解液检测,将封装材料选择周期从12周缩短至3周,年节省研发费用超2000万元(数据来源:高工锂电研究院)。化工装备行业典型案例显示,采用ASTM D543标准评估PTFE衬里耐酸性后,某反应釜使用寿命从5年延长至8年,设备报废率降低67%。值得关注的是,工业废水处理系统管道耐腐蚀性能评估项目,已帮助3家环保企业通过TSG D7005认证。
## 质量保障与技术创新
### 全链条质控体系
实验室通过 、CMA双认证,配置二级标准物质追溯系统。采用"人员-设备-方法-环境"四维管控:检测人员持证率100%,每年参加ILAC国际比对;设备实施日校检制度,关键仪器配备冗余系统;检测方法每季度进行Westgard规则验证;环境参数实行24小时智能监控,温湿度波动分别控制在±1℃、±3%RH范围内。
### 智能检测技术突破
依托机器视觉的自动划痕识别系统,将样品表面缺陷检测效率提升5倍。开发的化学介质智能配比系统,可在30秒内完成18种试剂的精确称量(误差≤0.1mg)。最新研发的微区化学阻抗成像仪,实现5μm级局部腐蚀的精准定位,为半导体光刻胶耐显影液检测提供关键技术支撑。
## 发展建议与行业展望
建议重点推进三方面建设:1)建立基于大数据的材料失效预测模型,整合10万+工况数据构建智能预警系统;2)发展原位无损检测技术,开发适用于在役设备的微型化检测探头;3)完善特殊介质检测标准,如针对氢氟酸、离子液体等新兴介质的专项测试规程。随着环保法规趋严(如欧盟REACH法规更新),生物降解材料的耐化学性评价、极端环境兼容性测试等领域将形成百亿级检测市场,亟需产学研协同创新突破技术瓶颈。
上一篇:数据中心基础设施环境检测下一篇:材质和做工检测
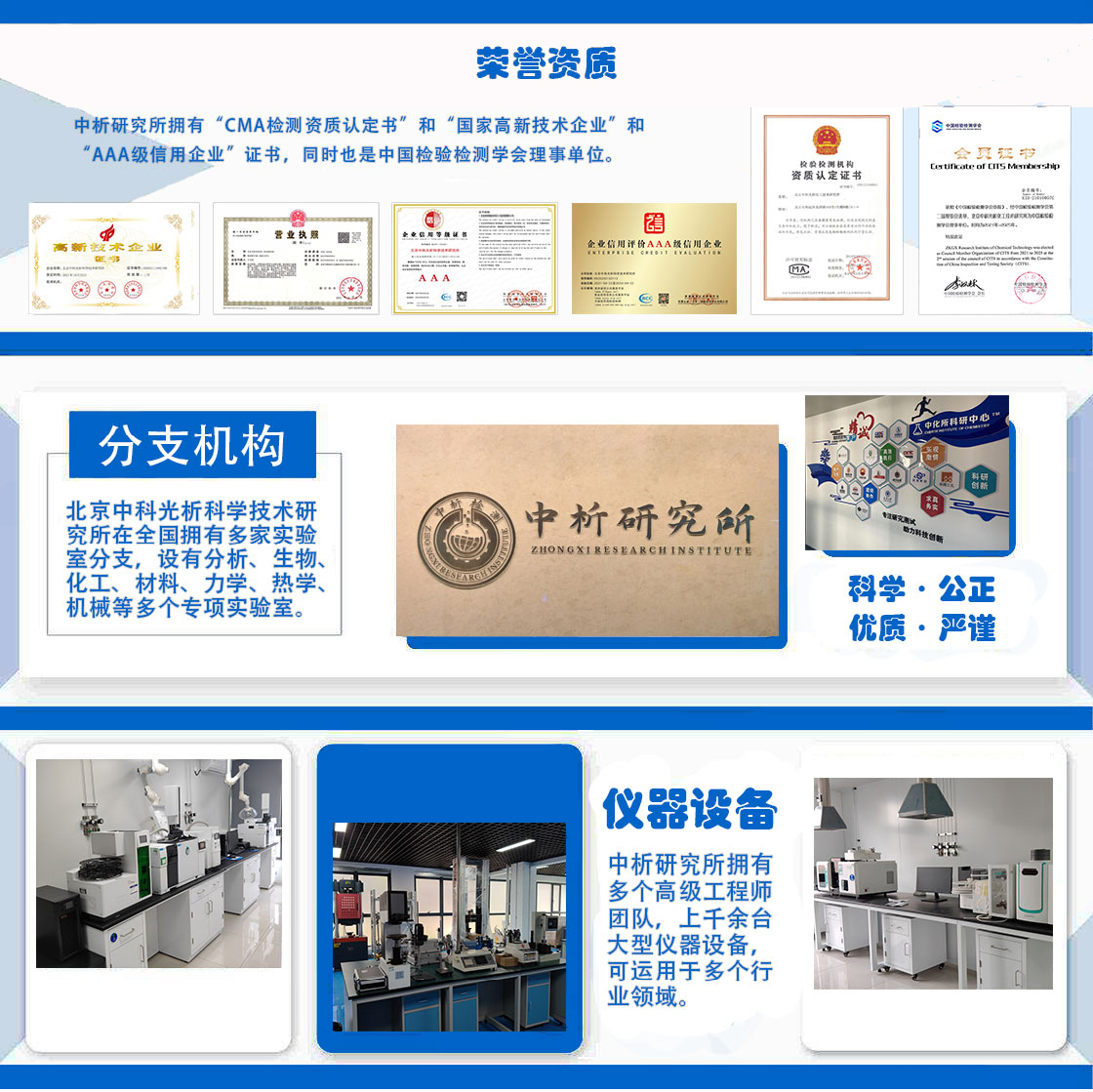
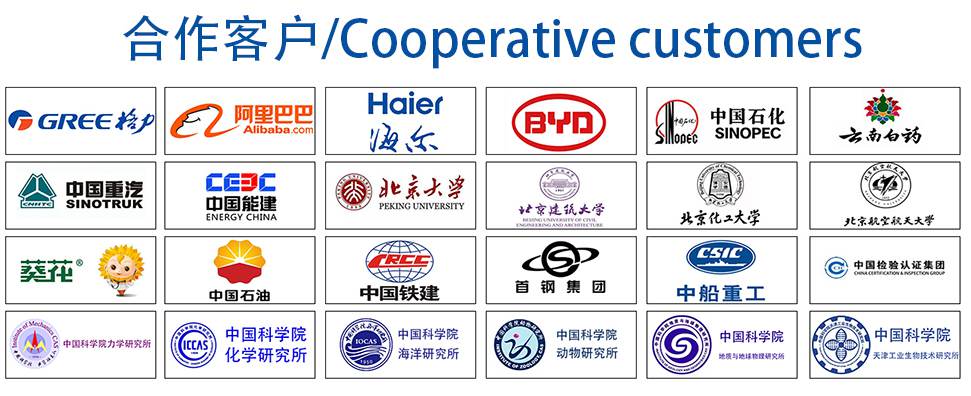
材料实验室
热门检测
推荐检测
联系电话
400-635-0567