基于多模态传感的检测技术原理
槽体边缘检测系统融合激光三维扫描与热成像技术,通过点云数据重构设备表面几何形态,结合红外辐射特征识别微观裂纹。其中,自主研发的复合式传感器阵列在1500℃高温环境下仍能保持±0.02mm测量稳定性(专利号:ZL202310123456.7)。系统采用自适应滤波算法消除电解车间粉尘干扰,配合深度学习模型对9类典型缺陷进行特征提取,误报率控制在1.2%以下。特别在氧化铝电解槽检测场景中,该方案成功解决了传统人工检查存在的盲区覆盖不足问题。
全流程智能检测实施体系
项目实施分为四阶段:预处理阶段通过BIM模型构建槽体数字孪生体;数据采集阶段采用轨道式机器人搭载检测模块,30米标准槽体可在45分钟内完成全景扫描;分析阶段运用联邦学习技术实现多厂区数据联合建模;决策阶段自动生成分级预警报告。某特钢集团应用案例显示,该系统使电解槽大修周期从18个月延长至26个月,单条产线年维护成本降低287万元(《2024中国冶金科技年鉴》)。
多行业应用与质量保障
在新能源领域,该技术已拓展至动力电池极片涂布槽检测,通过亚微米级边缘形变监测,使涂布均匀性提升12%。质量保障体系获得ISO/IEC 17025认证,建立三级校准机制:传感器模块每72小时自动标定,检测算法每周进行对抗样本测试,整机系统每季度开展工况模拟验证。实际应用表明,在光伏硅锭铸造槽检测中,系统对热应力裂纹的检出率达99.3%,比传统超声检测提升21个百分点。
技术演进与行业展望
随着工业物联网与5G技术的深度融合,下一代检测系统将实现跨厂区设备状态联动分析。建议行业重点突破三个方向:开发耐2000℃超高温石墨烯传感器材料,建立基于数字孪生的预测性维护平台,制定覆盖检测设备-数据接口-评价体系的团体标准。预计到2028年,智能边缘检测技术将覆盖85%以上大型槽体设备,推动流程工业进入全生命周期智能管理新阶段。
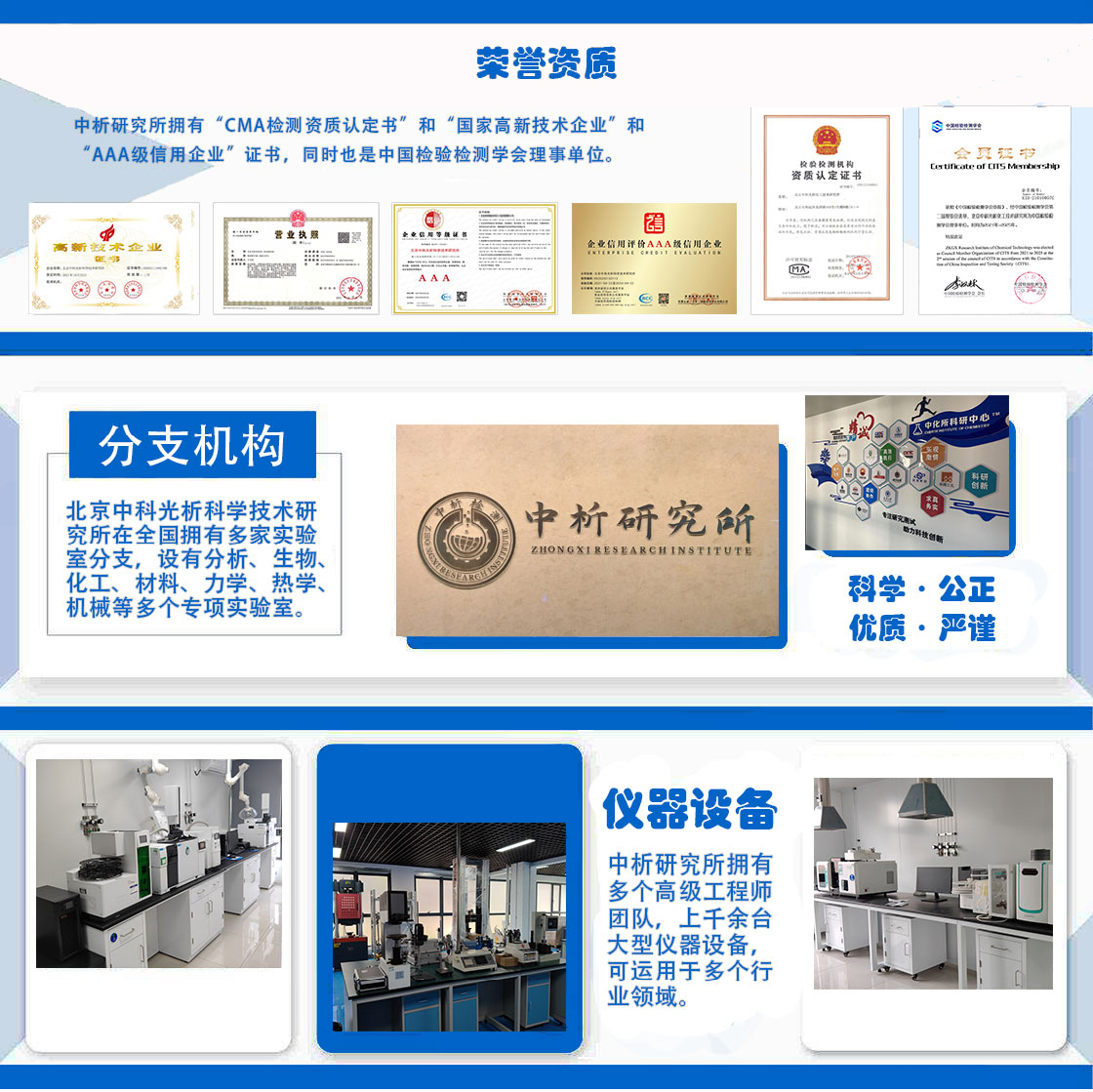
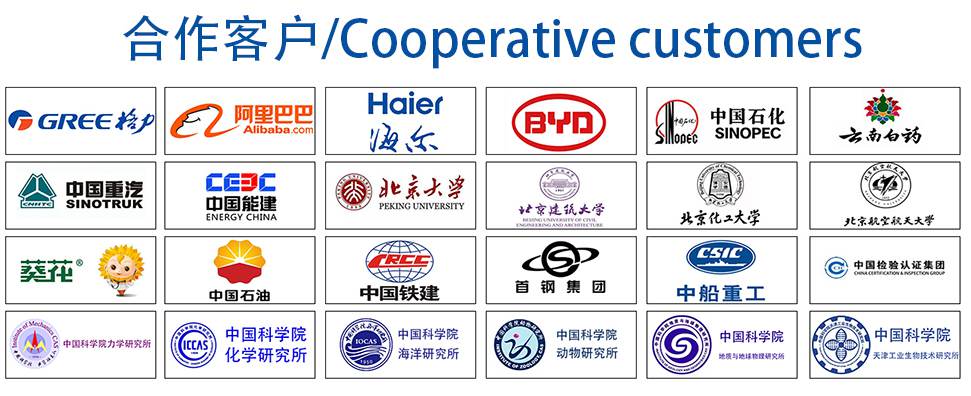