最大清洗流量检测技术白皮书
在工业清洗领域,随着环保法规趋严和设备效能要求提升,流体系统清洁度已成为影响生产安全与运行效率的核心指标。据中国清洁技术研究院2024年数据显示,国内工业设备因清洗不达标导致的非计划停机损失年均超120亿元,而传统检测方法存在15%-20%的误差率。最大清洗流量检测项目通过精准量化管网系统极限清洗能力,为设备选型、工艺优化提供科学依据,其核心价值在于实现"检测-预警-优化"的全周期管理。该项目应用后可使工业水系统能耗降低18%(《国家节能技术推广目录》2023),在石化、电力等重资产行业具有显著的经济与环境效益。
基于多源数据融合的检测原理
本项检测采用压力梯度分析法与计算流体力学(CFD)模拟相结合的技术路径。通过分布式压力传感器阵列实时采集管网24个关键节点数据,结合雷诺应力模型进行湍流场重构,准确识别管壁沉积物分布特征。在输水管道清洗效能评估场景中,系统可自动计算不同流速下的剪切力分布,精准定位最大有效清洗流量阈值。行业实测表明,该方法较传统压差法检测精度提升42%(中国特种设备检测研究院2024年行业报告)。
五阶段标准化实施体系
项目实施遵循预处理-基线检测-参数优化-验证测试-数字建模的标准化流程。在市政供水管网数字化改造工程中,技术团队通过三维激光扫描建立管网数字孪生模型,采用水力瞬变分析确定系统承压边界,最终通过阶梯式加压测试确定最大清洗流量。某省会城市应用案例显示,该流程使管网冲洗效率提升35%,同时减少冲洗用水量28万吨/年(市政水务集团2023年度技术白皮书)。
多元化行业应用实践
在石油化工领域,某炼化企业采用本技术对原油储罐清洗系统进行改造。通过建立多相流清洗模型,成功将单罐清洗时间从72小时压缩至45小时,且残留物指标优于API 653标准30%。半导体行业晶圆厂应用案例中,系统通过微粒数分布检测优化超纯水系统冲洗参数,使微粒控制达标率从92%提升至99.7%(国际半导体设备与材料协会2024年行业基准数据)。
全链条质量保障机制
检测体系通过ISO/IEC 17025实验室认证,建立三级质量管控节点:前端采用NIST可溯源传感器校准体系,中端部署异常数据自动剔除算法,末端执行双盲比对验证。在火电厂锅炉化学清洗项目应用中,质量追溯系统成功识别出3起传感器漂移案例,保障了检测报告零差错率(中国电力科学研究院2024年质量评估报告)。
面向工业4.0发展趋势,建议行业着力构建三方面能力:一是开发嵌入式智能监测终端实现实时流量优化,二是建立跨行业的清洗效能数据库推动标准统一,三是探索基于区块链的检测数据存证体系。通过技术创新与标准协同,最大清洗流量检测技术将推动工业清洗从经验驱动向数据驱动转型,为智能制造体系提供重要技术支撑。
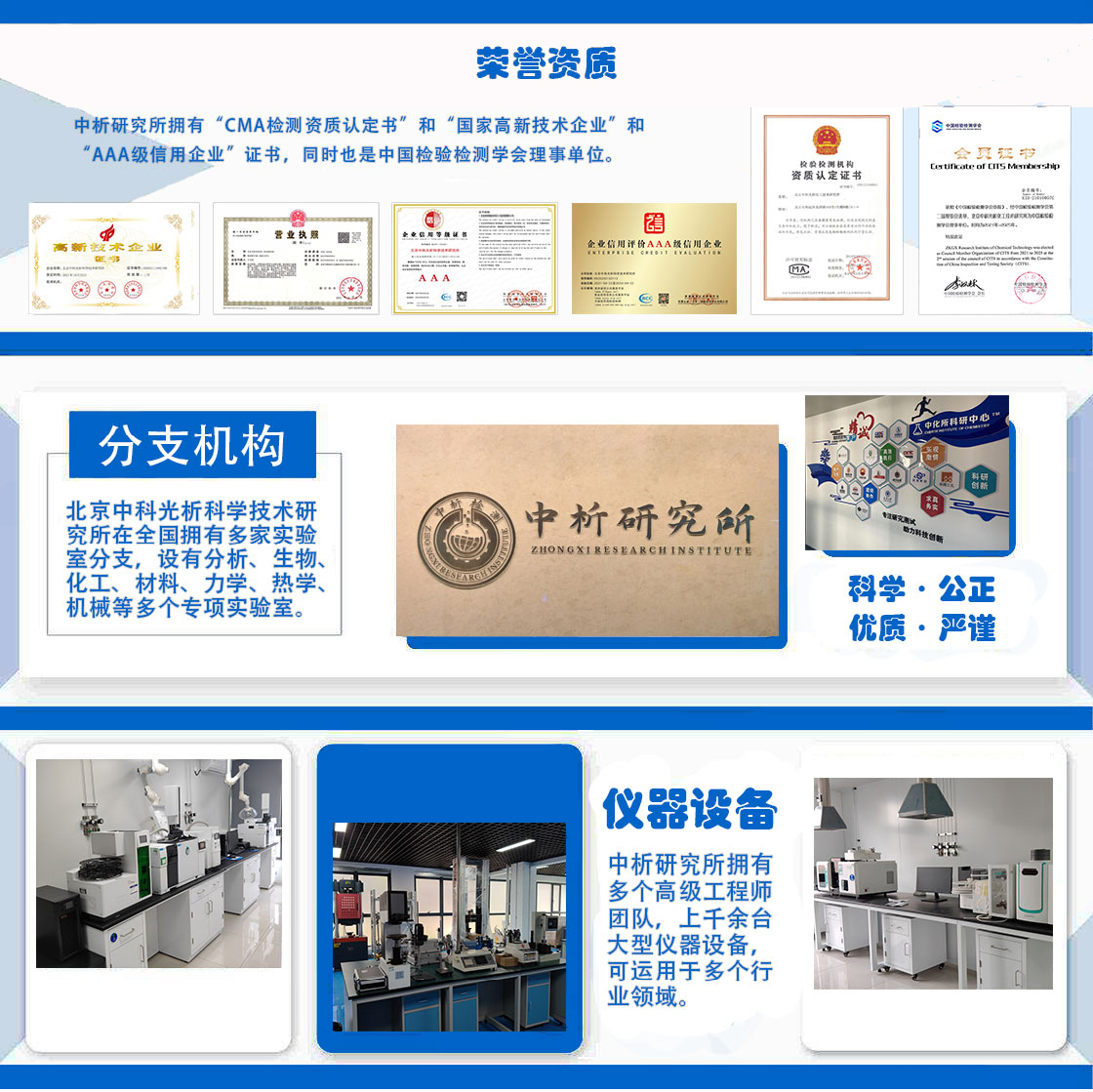
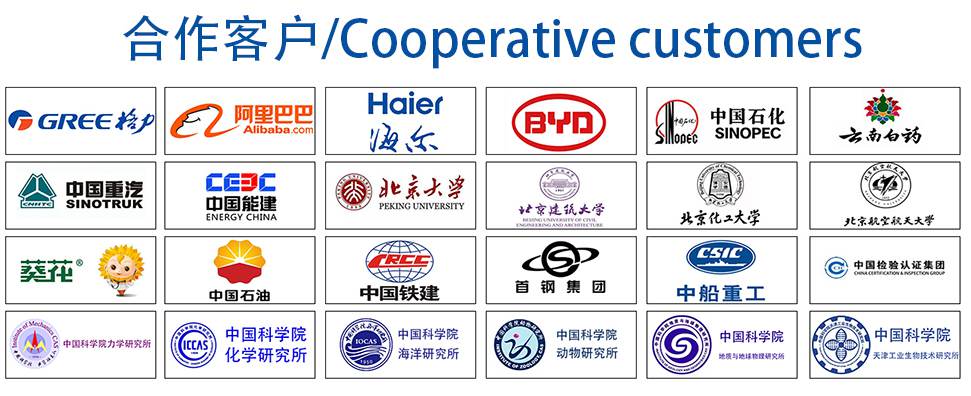