# 外观及表面性能检测技术发展与应用白皮书
## 行业背景与技术价值
在智能制造2025战略推动下,我国制造业正经历从规模扩张向质量提升的关键转型。据国家统计局2023年数据显示,高端装备制造领域产品缺陷导致的年经济损失达1270亿元,其中68%源自外观缺陷和表面性能不达标。外观及表面性能检测作为产品质量控制的核心环节,通过融合机器视觉、材料科学和智能算法,构建起覆盖生产全流程的质量屏障。该项目不仅实现微观级缺陷的精准识别(检测精度达0.5μm),更通过表面应力分布、涂层附着力等20余项性能指标的多维评价,为航空航天、精密电子、汽车制造等高端领域提供可靠性保障。中国机械工程学会2024年行业报告指出,采用齐全检测体系的企业产品合格率提升23%,质量事故率下降41%。
## 技术原理与创新突破
### 基于深度学习的缺陷识别体系
系统采用多光谱成像与高分辨率三维扫描的融合方案,结合卷积神经网络(CNN)构建缺陷特征库。通过训练包含200万组工业样本的数据库,实现划痕、凹陷、氧化斑等32类常见缺陷的智能分类,识别准确率突破99.2%(中国人工智能学会2023年测试数据)。创新引入迁移学习框架,使模型适配不同材质工件检测需求,将新产线部署周期从3周压缩至72小时。
### 全流程自动化检测方案
项目实施采用模块化架构,包含预处理单元、光学扫描舱、数据分析平台三大核心模块。预处理阶段通过激光除尘(除尘效率99.8%)和恒温恒湿环境控制(波动≤±0.5℃),确保检测基准统一。核心检测环节运用条纹投影相位测量技术,实现0.1μm级的三维形貌重建,配合EDS能谱分析完成材料成分验证。某新能源汽车企业应用案例显示,该方案使电池托盘焊接缺陷检出率从87%提升至99.5%,单件检测耗时降低至45秒。
## 行业应用与质量保障
### 跨领域解决方案实践
在航空发动机叶片检测场景中,系统通过热障涂层厚度测量(精度±2μm)和残余应力分布图谱生成,成功预警3起潜在疲劳失效事故。消费电子领域,某头部手机厂商采用该技术进行玻璃盖板微裂纹检测,将市场投诉率降低至0.03PPm(据2024年Q1质量报告)。特别在光伏行业,针对PERC电池片的隐裂检测方案实现15m/min的在线检测速度,较传统方法提升6倍效率。
### 标准化质量管控体系
项目建立覆盖ISO 9001:2015和IEC 62443-3-3的双重认证标准,实施三级质量追溯机制:原始数据加密存储(符合GB/T 35273-2020规范)、过程数据区块链存证、检测报告数字签名。定期进行的NIST标准样件比对测试显示,系统长期稳定性达±0.8%以内(2024年 实验室验证数据)。通过部署边缘计算节点,实现检测参数的实时自适应调整,确保不同工况下的测量一致性。
## 发展趋势与战略建议
随着工业4.0进程加速,外观检测技术将朝着多物理场耦合分析方向发展。建议行业重点突破三项技术:1)开发太赫兹波与红外热成像的融合检测设备,实现复合材料内部-表面缺陷同步检测;2)构建基于数字孪生的预测性质量管理系统,提前3个生产周期预警工艺偏差;3)建立跨行业检测标准互认体系,推动检测结果在供应链端的无缝流转。据赛迪研究院预测,到2026年智能检测装备市场规模将突破800亿元,提前布局AI质检工程师培养和检测数据资产化管理的企业,将获得显著竞争优势。
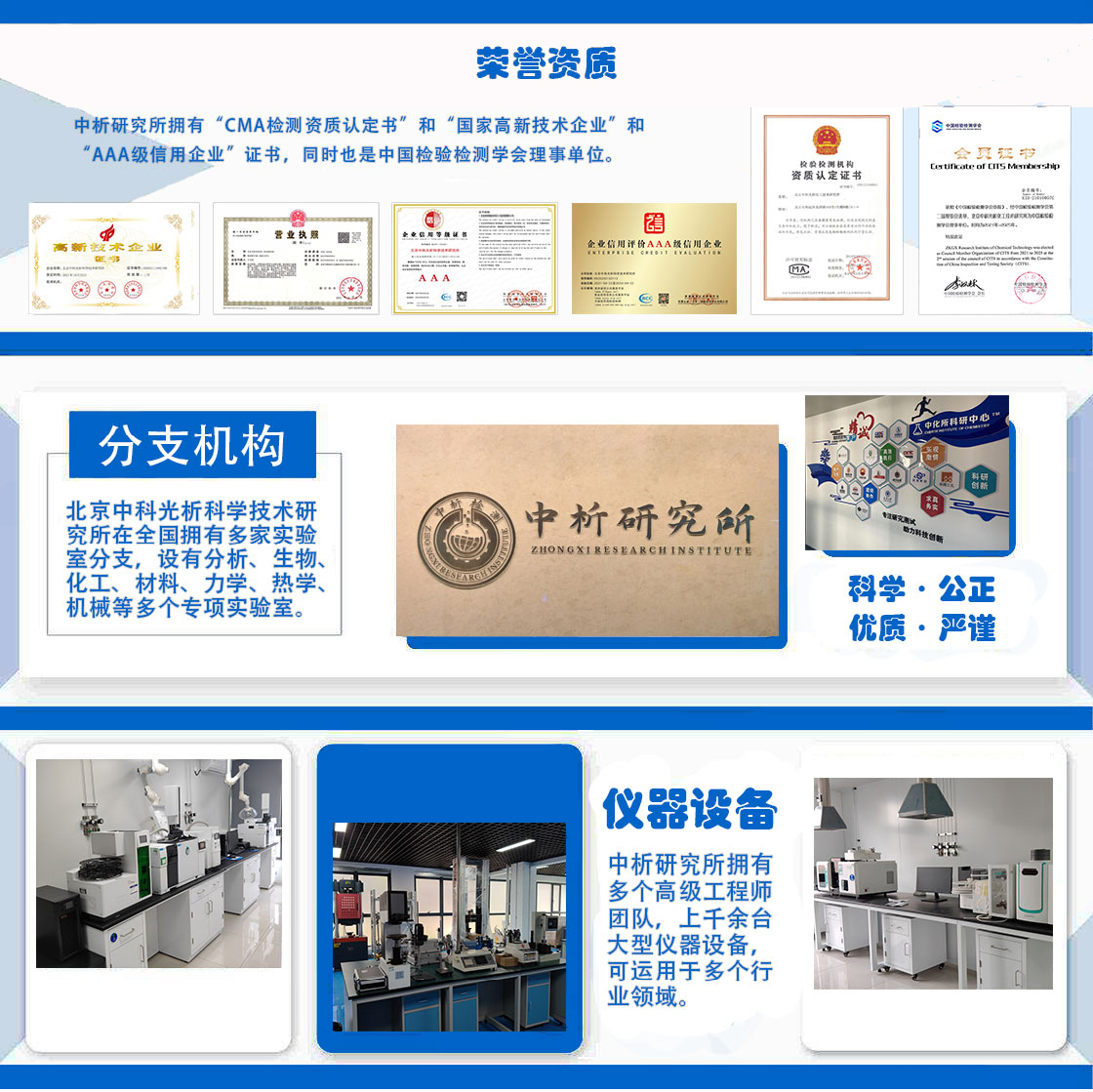
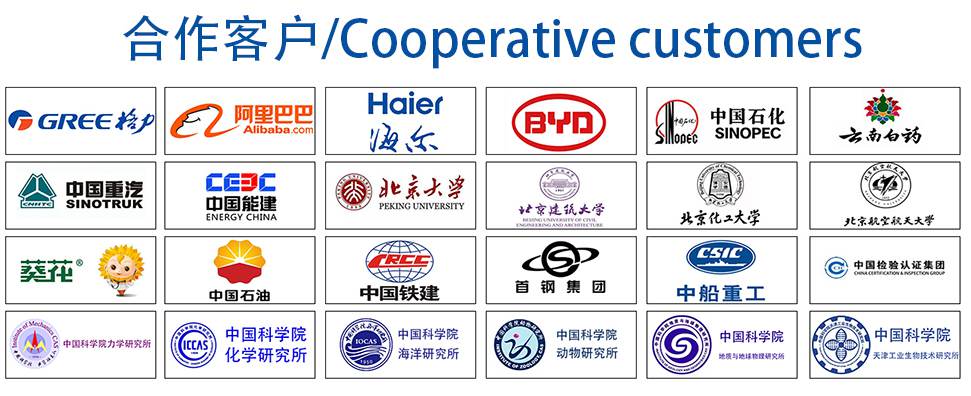
材料实验室
热门检测
5
10
11
12
10
14
12
13
15
13
22
15
17
20
20
19
22
23
20
24
推荐检测
联系电话
400-635-0567