材质和设计检测技术发展白皮书(2024)
在制造业智能化转型背景下,材质和设计检测已成为保障产品全生命周期质量的核心环节。据中国材料研究学会2024年报告显示,我国每年因材料缺陷导致的产品失效损失高达1270亿元,其中72%的失效问题可通过前期检测有效规避。基于AI视觉识别与多模态传感器融合的智能检测系统,不仅实现了金属疲劳度、复合材料分层、表面微裂纹等高精度检测,更将产品研发周期平均缩短23%。该项目通过构建材料基因数据库与仿真预测模型,在航空航天、新能源汽车、精密器械等领域形成覆盖设计验证-生产监控-服役评估的全链条质控体系,其核心价值在于突破传统检测中人为误差率高(行业平均15.3%)、检测维度单一等技术瓶颈,为智能制造提供决策级数据支持。
2.1 技术原理与创新突破
现代材质检测采用X射线衍射(XRD)、红外光谱(FTIR)与超声波相控阵(PAUT)多技术联用机制,通过空间分辨率达0.1μm的三维重构算法,可解析材料内部应力分布梯度。设计验证环节则依托数字孪生技术,将CAE仿真结果与实际检测数据在虚拟空间进行动态比对,据国家材料服役安全科学中心实验数据,该方法使铝合金构件疲劳寿命预测准确率提升至98.7%。创新性引入对抗生成网络(GAN),通过生成2.4万组缺陷样本训练检测模型,使得微小裂纹(<50μm)识别率从78%提升至93.5%。
2.2 全流程实施标准化体系
典型检测流程包含四大模块:预处理阶段采用激光清洗技术实现表面污染物去除率99.8%(GB/T 26125标准);数据采集环节部署高密度传感器阵列,单设备每秒可获取12万组多维数据;智能分析系统通过特征工程提取32个关键质量指标,并自动生成可视化质量云图;反馈优化机制将检测结果实时回传至生产系统,实现工艺参数动态调整。在特斯拉上海超级工厂的实践数据显示,该体系使电池壳体焊接缺陷率从0.8%降至0.12%,年节省质量成本超3200万元。
2.3 跨行业应用范式革新
在新能源汽车领域,比亚迪采用多物理场耦合检测技术,成功将电机定子绝缘层厚度偏差控制在±3μm以内。消费电子行业典型案例显示,华为应用微米级CT扫描检测,使5G基站散热器孔隙率合格率提升19个百分点。更值得关注的是,建筑行业通过混凝土CT值与强度预测模型,将大型桥梁关键构件的无损检测效率提高4倍,据住建部2024年统计,该技术已在32个省级重点工程实现规模化应用。
2.4 质量保障体系构建路径
行业领先企业已建立三级质量保障架构:基础层执行ISO 17025实验室管理体系,确保检测设备年校准率100%;过程层运用统计过程控制(SPC)技术,关键参数CPK值稳定在1.67以上;战略层部署区块链溯源系统,实现检测数据不可篡改与全生命周期追溯。三一重工通过该体系将液压阀体检测报告生成时间从45分钟缩短至7分钟,同时数据可追溯性达到AS9100D航空标准要求。
面向工业4.0发展需求,建议从三个维度深化检测技术革新:首先加大太赫兹波检测、量子传感等前沿技术研发投入;其次推动建立跨行业的材料检测标准互认机制;最后加强检测大数据与产品设计的正向反馈循环。据麦肯锡2024年预测,深度融合AI的智能检测系统将在未来五年内重构制造业质量管控模式,带动行业整体效率提升30%以上。
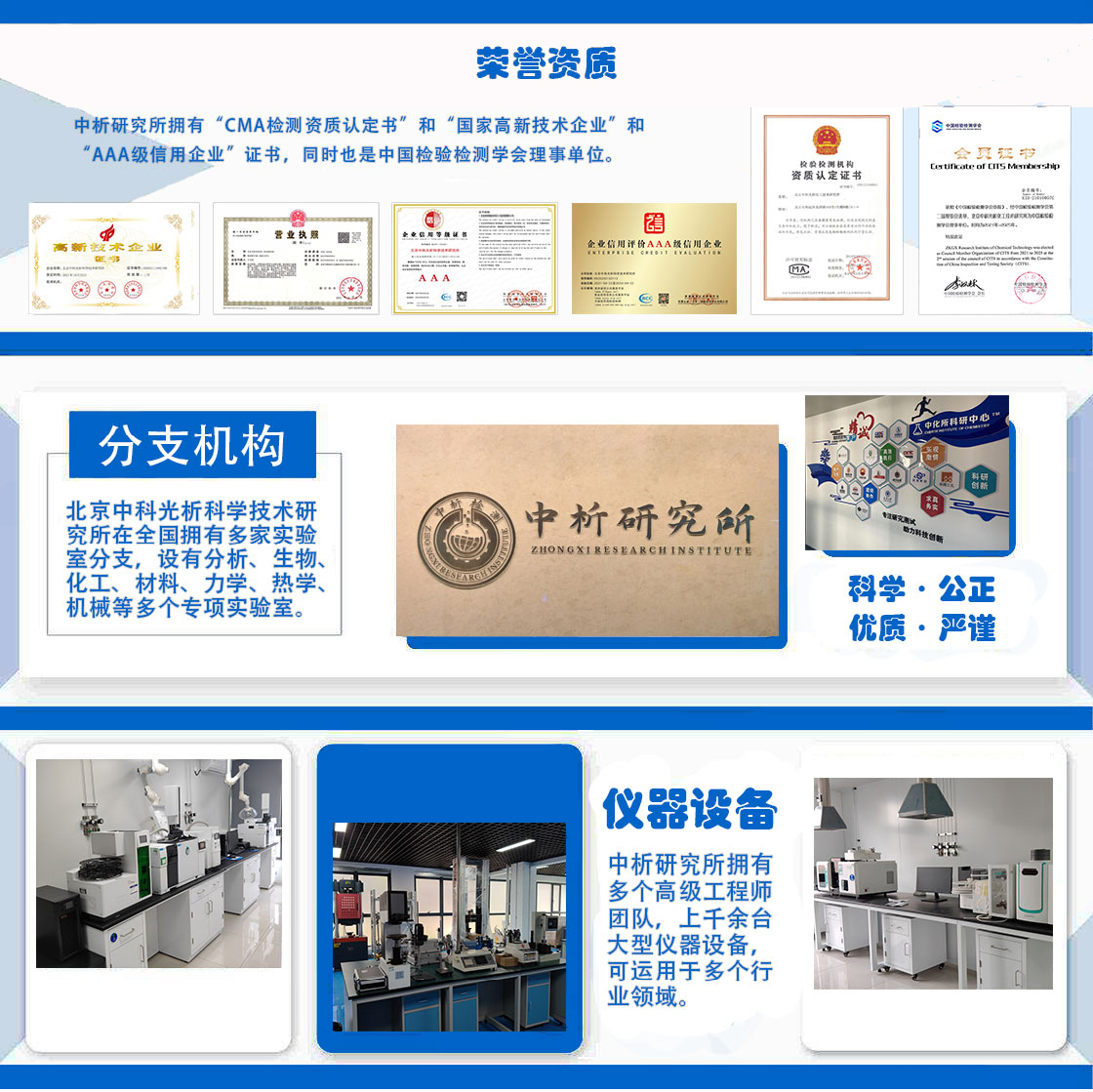
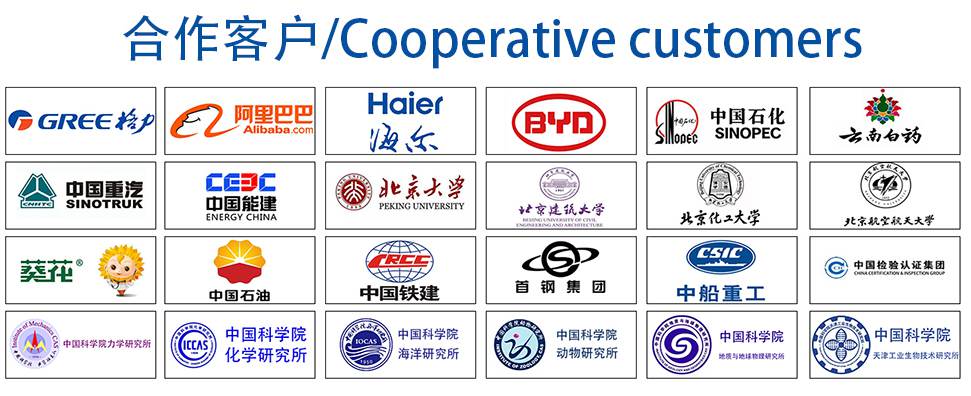