铜加速盐雾试验检测:关键技术与发展实践
在工业制造向精密化、高端化转型的背景下,材料耐腐蚀性能已成为衡量产品质量的核心指标之一。据中国腐蚀与防护学会2023年度报告显示,因金属腐蚀造成的直接经济损失达2.5万亿美元,其中电子元器件、汽车零部件的早期失效问题尤为突出。铜加速盐雾试验(CASS)作为国际通用的加速腐蚀测试方法,通过模拟含铜离子的酸性盐雾环境,可精准评估材料及表面处理工艺的耐腐蚀等级。该项目在新能源汽车三电系统、5G通讯基站连接器等关键领域具有特殊价值,据SGS检测中心统计,采用CASS优化的表面处理方案可使产品耐腐蚀寿命提升40%以上,有效降低售后维护成本并规避质量风险。
技术原理与测试机制
铜加速盐雾试验基于电化学腐蚀原理,在传统中性盐雾试验(NSS)基础上引入0.26±0.02g/L氯化铜溶液,将pH值严格控制在3.1-3.3范围内形成酸性腐蚀环境。该体系通过铜离子的催化作用,使金属表面形成微电池效应,加速阳极溶解过程。检测设备需维持35±2℃恒温环境,雾化沉降量达到1.0-2.0ml/80cm²·h的标准要求。相较于常规盐雾试验,CASS测试的腐蚀速度可提升8-10倍(数据来源:ASTM B368标准),特别适用于评价镀层致密性和阴极保护效果。
标准化实施流程建设
检测流程分为预处理、设备调试、周期监测三个阶段。预处理环节需依据ISO 9227标准,采用化学除油与去离子水清洗双重工序确保试样表面清洁。测试设备需定期校准雾化喷嘴压力(维持在70-170kPa区间)和集雾器倾斜角度。典型测试周期设置48小时为基本单位,通过目视检查、X射线能谱分析(EDS)相结合的方式量化锈蚀面积。某新能源汽车企业实践表明,在充电桩连接器检测中采用分级评估体系(腐蚀面积≤0.1%判定为A级),可将产品失效率从1.8%降至0.3%。
行业应用与质量保障
在消费电子领域,头部手机厂商将CASS试验纳入Type-C接口强制检测标准,要求通过96小时测试后接触电阻变化率≤15%。某实验室创新采用循环腐蚀测试法(CCT),将盐雾、干燥、湿热阶段交替进行,更真实模拟沿海地区使用环境。质量保障体系构建包含三个维度: 认证实验室的环境控制(温度波动±0.5℃)、检测设备的年度计量校准(参照JJF 1101-2019规范)、以及数据追溯系统(每批次试样配备二维码)。德国TÜV莱茵的比对试验显示,建立完整质控体系的实验室间数据偏差可控制在±5%以内。
技术演进与发展建议
随着新型合金材料和复合镀层技术的突破,传统CASS试验面临检测灵敏度不足的挑战。建议行业从三方面进行优化:开发基于机器视觉的自动评级系统,建立多因素耦合的加速模型(整合温度、Cl⁻浓度、pH值动态变化参数),以及制定针对纳米涂层的专项检测规程。据Frost & Sullivan预测,至2025年腐蚀检测市场规模将突破82亿美元,智能检测设备与工业物联网(IIoT)的融合将推动检测效率提升30%以上。行业亟需构建包含材料供应商、检测机构、终端用户的协同创新平台,共同完善耐腐蚀性能评价体系。
当前,铜加速盐雾试验正向智能化、场景化方向演进。建议重点领域企业建立产品全生命周期腐蚀数据库,将实验室数据与现场失效案例进行关联分析。同时关注欧盟ELV指令、RoHS 3.0等法规对检测参数的影响,开发环境友好型替代检测方案。通过产学研深度合作,推动我国腐蚀检测技术从标准执行者向规则制定者转变,为高端装备制造提供更有力的技术支撑。
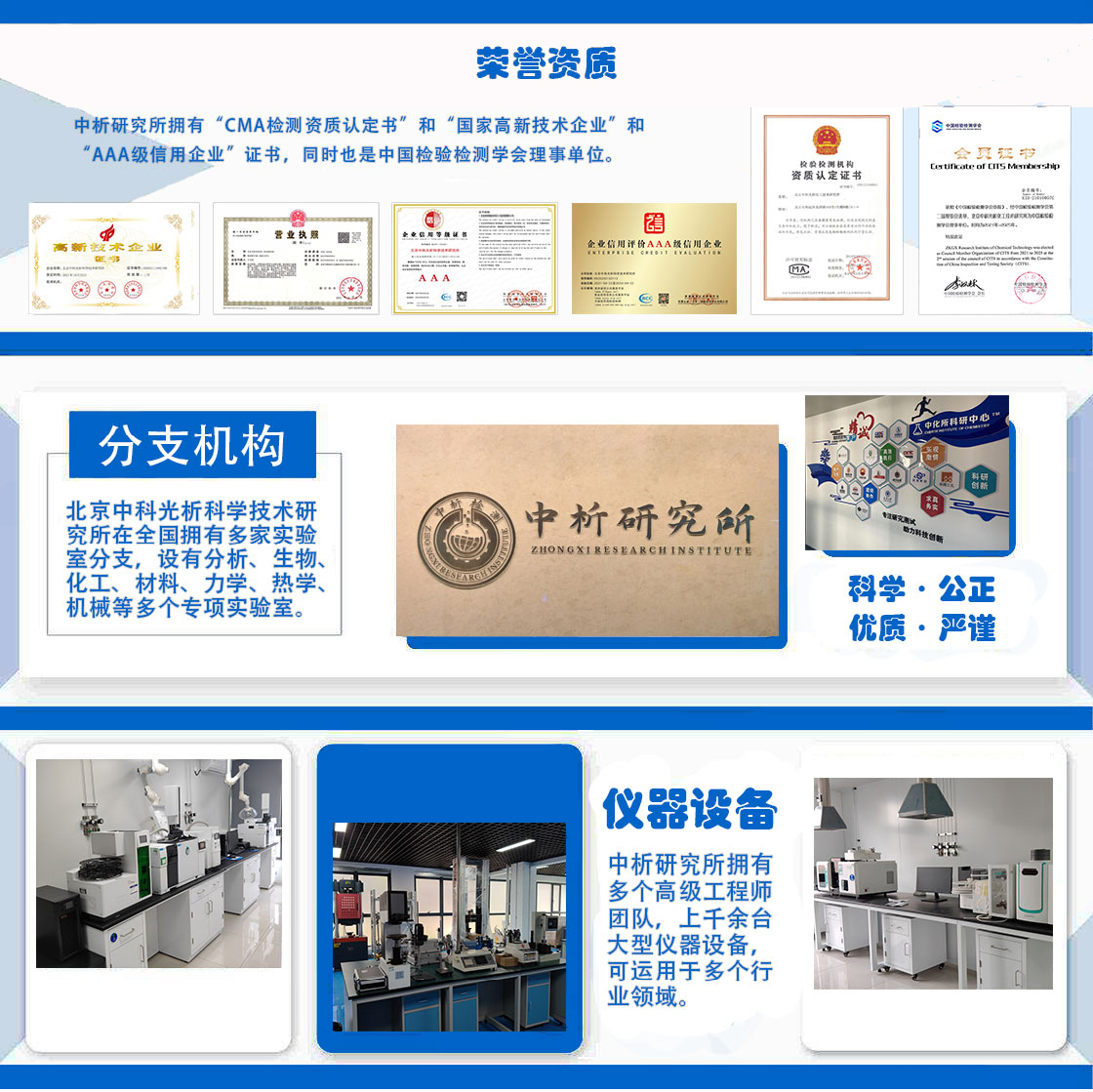
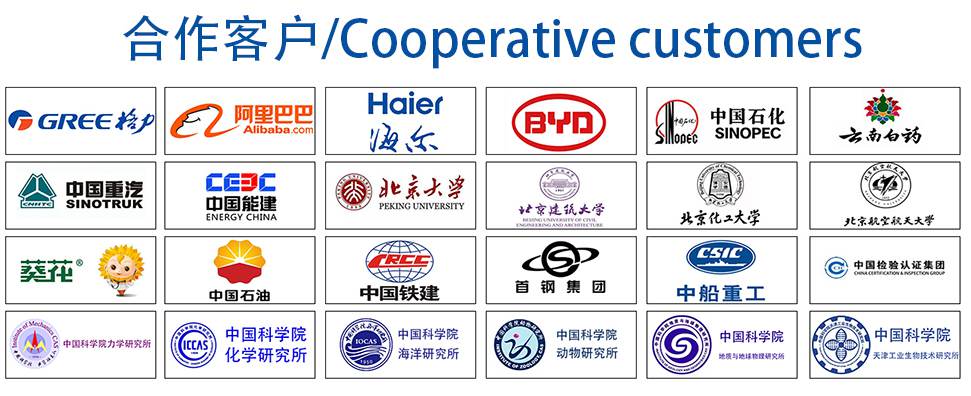