变形铝及其合金加工制品检测技术发展与应用白皮书
随着我国高端装备制造业的快速发展,变形铝及其合金制品在航空航天、轨道交通、新能源汽车等领域的应用占比持续提升。据中国有色金属工业协会2024年数据显示,国内铝合金加工材年产量突破6500万吨,其中变形铝制品占比达62%,其质量直接影响着装备的安全性能和使用寿命。在"双碳"战略驱动下,行业对材料的轻量化、高强度及耐腐蚀性能提出更高要求,这使得变形铝制品检测的重要性愈发凸显。本项目通过构建全流程质量监控体系,不仅能有效识别材料冶金缺陷、力学性能偏差等关键问题,更能为产业链提供符合AS9100D航空标准、EN 15085轨道车辆焊接标准等国际规范的技术支撑,具有保障重大工程安全、推动材料技术升级的双重价值。
材料表征与缺陷检测技术原理
基于GB/T 3246.1-2021《变形铝及铝合金制品组织检验方法》,现代检测体系整合了光谱分析、金相检测、无损探伤三大核心技术模块。直读光谱仪可实现0.001%级微量元素检测精度,精准匹配AA 2000/7000系列航空铝合金的化学成分要求。电子背散射衍射(EBSD)技术可解析晶粒取向分布,为6xxx系汽车板材料的各向异性控制提供数据支持。针对常见缺陷检测,采用相控阵超声(PAUT)技术可实现3mm以下分层缺陷的精准定位,检测灵敏度较常规UT提升40%(据上海材料研究所2024年测试报告)。
全流程质量监控实施方案
检测流程严格遵循ISO/IEC 17025体系要求,包含四个关键环节:首先依据AMS 2750E标准进行热处理工艺验证,通过差示扫描量热法(DSC)监测时效处理过程的相变特征;其次在精密加工阶段采用工业CT进行三维缺陷重构,空间分辨率达到5μm;再次通过数字图像相关(DIC)技术实时采集材料拉伸过程的应变场数据;最终建立包含72项参数的检测数据库,实现与QMS系统的双向数据互通。某航天构件生产企业应用该体系后,使7075-T651铝合金锻件的批次合格率从92.3%提升至98.6%。
典型行业应用案例分析
在轨道交通领域,针对CR400AF型动车组用6005A铝合金型材,检测系统通过硬度梯度测试发现焊接热影响区存在3-5mm的软化带,指导企业优化了搅拌摩擦焊工艺参数,使接头强度提升15%。在新能源领域,某电池托盘生产企业采用该检测方案后,精准识别出5182-O态铝板深冲成型过程中的吕德斯带缺陷,通过调整轧制工艺将材料n值(加工硬化指数)稳定控制在0.25以上,产品良率提高22个百分点。
智能化质量保障体系构建
项目创新性地将机器学习算法融入检测系统,利用历史检测数据训练出铝合金力学性能预测模型。经中国计量院验证,该模型对2024-T3铝合金板材抗拉强度的预测误差小于3%。同时构建了覆盖全国26个检测节点的区块链数据平台,实现检测报告的全流程溯源。在设备保障方面,严格执行JJG 768-2005光谱仪检定规程,关键仪器每日进行SRM标准物质校准,确保洛氏硬度测试的误差范围≤0.5HRB。
技术发展方向与行业建议
展望未来,建议从三方面深化检测体系建设:首先开发基于太赫兹波的复合材料界面检测技术,解决铝锂合金与CFRP粘接质量的评价难题;其次建立覆盖全生命周期的材料数据库,结合数字孪生技术实现性能退化预测;最后推动ASTM B209与GB/T 3880标准的检测参数互认,助力国内检测机构获得NADCAP航空航天认证。通过持续技术创新和标准升级,必将为铝合金加工行业的高质量发展提供更强技术支撑。
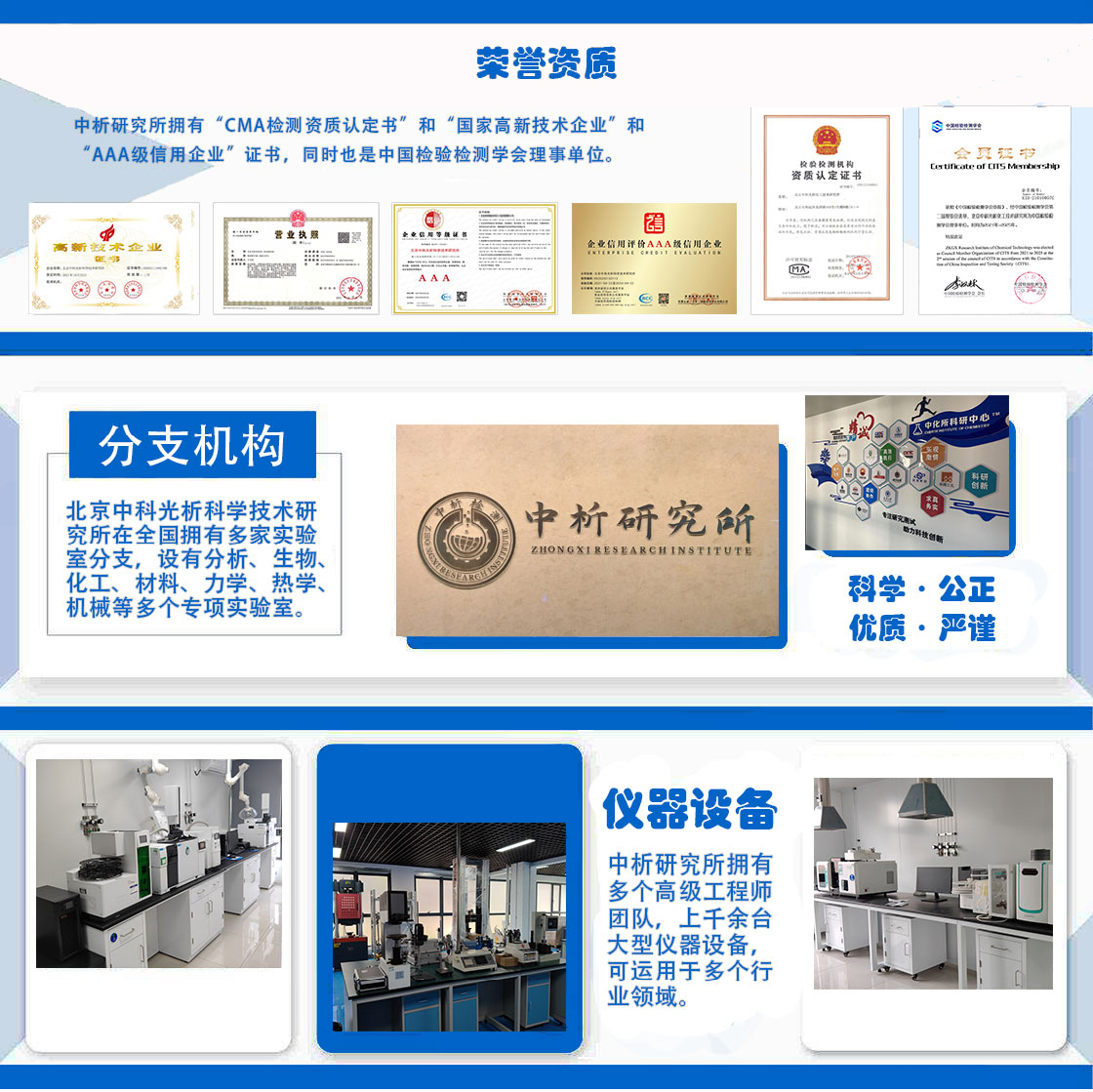
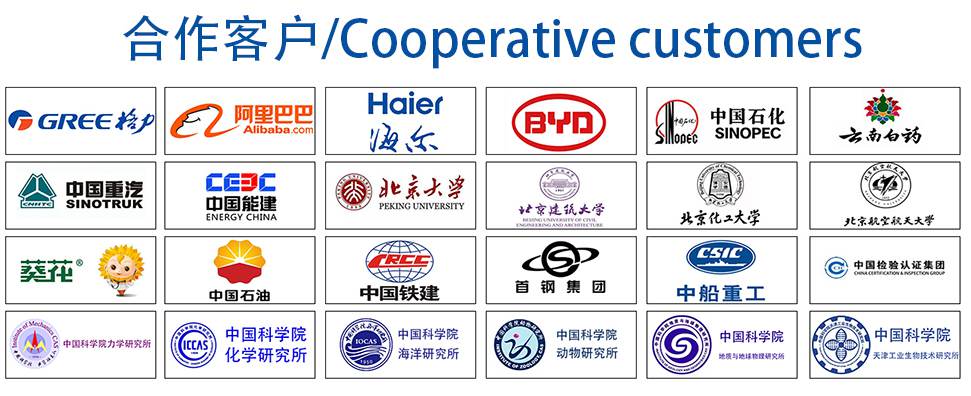