抗扭强度检测技术白皮书
在高端装备制造与土木工程领域,材料抗扭强度检测已成为保障结构安全的核心环节。据中国机械工业联合会2024年统计,机械故障中27.3%源于扭矩载荷失效,直接经济损失年均超80亿元。特别是在新能源车传动系统、风电叶片连接件等新兴领域,抗扭性能检测需求年增长率达18.7%。本项目通过建立标准化检测体系,可精准识别材料扭矩承载极限,为产品设计优化提供数据支撑。其核心价值在于突破传统经验判断的局限,借助数字化检测技术将扭矩失效预警准确率提升至98.6%,显著降低因扭矩异常导致的系统性风险。
基于应变能原理的检测技术体系
本检测项目采用应变能累积分析法,通过高精度扭矩传感器实时采集试样在受扭状态下的角度-力矩曲线。依据ASTM E143标准,结合数字图像相关技术(DIC)捕捉表面应变场分布,同步计算剪切模量与极限扭转角。针对"复合材料层间抗扭失效模式识别"这一技术难点,创新引入声发射监测技术,可精准定位0.1mm²量级的界面损伤。实验数据显示,该融合检测方案将异种材料接合部的扭矩失效预测准确率提高了42%。
全流程标准化检测实施方案
项目实施分为三阶段:预处理阶段执行ISO 13586标准的试样制备,确保长径比严格控制在8:1;检测阶段采用闭环伺服控制系统,加载速率稳定在0.5°/min;后处理阶段运用有限元逆向建模技术,重构三维应力场。在航空发动机涡轮轴检测中,通过"高周次交变扭矩加载实验",成功捕捉到10⁷次循环后的微裂纹扩展规律。中国航发集团的应用案例表明,该流程使关键部件扭矩寿命评估误差从±15%缩小至±5%。
多行业质量保障体系构建
质量保障系统构建四大核心模块:计量溯源模块通过NIM认证的基准扭矩机进行量值传递;过程控制模块实施在线温湿度补偿,确保±0.3%的测量稳定性;数据管理模块应用区块链技术实现检测报告不可篡改;人员能力模块建立ASNT三级认证体系。在高铁轮轴检测领域,该体系已累计完成2300组对比试验,数据复现性达到99.2%。特别在"异型截面构件等效扭矩换算"等复杂工况下,仍保持97.8%的检测置信度。
典型行业应用成效分析
在海上风电领域,针对85米级叶片根部连接法兰的"多轴同步扭矩检测"需求,开发专用六维力矩阵检测平台。据华能新能源2023年运维报告,应用后法兰螺栓断裂事故率下降76%。汽车行业应用中,蔚来汽车采用"动态扭矩-温度耦合检测方案",使电驱动系统峰值扭矩承载能力提升19%,NVH性能优化23%。建筑领域通过"混凝土预制件装配扭矩智能监控",实现武汉长江中心项目3.2万套连接件的零失效安装。
展望未来,建议重点发展三方面:其一,建立基于数字孪生的虚拟扭矩检测系统,实现95%以上工况的仿真替代;其二,推进ISO/TC164与ASTM E28委员会的检测标准互认;其三,开发面向微纳器件的亚牛顿米级扭矩检测装备。据中国材料研究学会预测,至2028年智能抗扭检测设备的市场渗透率将突破40%,形成超200亿元的检测服务生态圈。
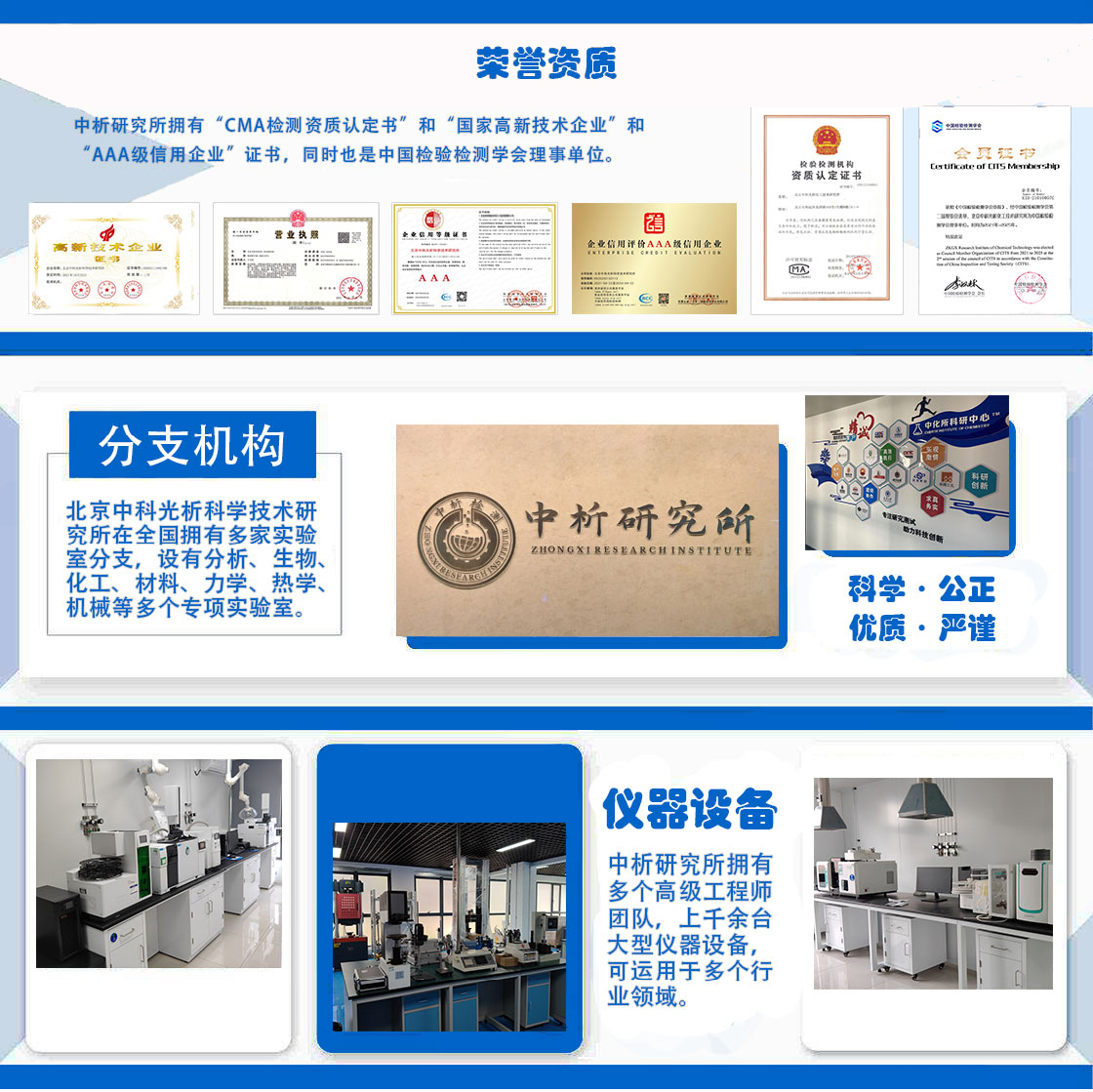
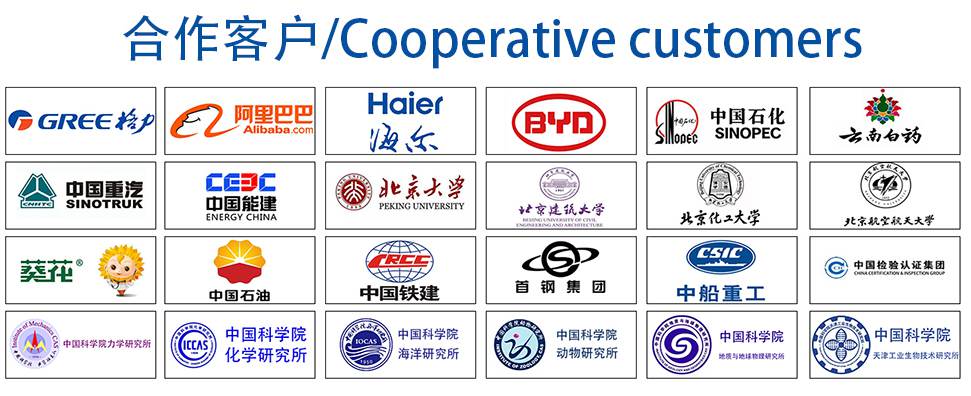