随着卫浴五金行业智能化转型加速,进水阀作为关键流体控制部件,其密封性能直接影响产品使用寿命与安全性。据中国五金制品协会2024年统计数据显示,国内卫浴产品年产量突破4.2亿件,其中因螺纹连接处渗漏导致的售后问题占比达17.3%,造成行业年度经济损失超12亿元。在此背景下,"高精度螺纹参数智能检测系统"的开发应用具有显著行业价值。该项目通过融合机器视觉与深度学习技术,实现螺纹导程角、中径偏差等关键参数的精确测量,将传统人工检测效率提升3倍以上,检测精度达到±0.01mm工业标准,为构建智能工厂质量管控体系提供关键技术支撑。
## 技术原理与创新突破基于多模态传感的检测系统架构
本检测系统采用模块化设计架构,集成高分辨率工业相机(500万像素CMOS)、环形LED多向光源和激光位移传感器。通过多角度图像采集与三维点云重构技术,系统可完整获取螺纹牙型轮廓数据。关键技术突破在于开发了自适应滤波算法,有效消除铸件表面毛刺对检测结果的干扰。据机械工业仪器仪表综合技术研究所验证,该系统对M12-M30规格螺纹的检测重复精度达99.2%,满足ISO 228-1标准中G级螺纹的检测要求。
智能化检测实施流程
标准作业流程包含五个核心环节:自动上料定向→视觉定位校准→三维参数扫描→实时数据分析→分类输出结果。在厦门某水暖器材企业的实际部署中,系统通过EtherCAT总线与生产线联动,完成单个工件检测仅需2.8秒。特别配置的动态补偿模块可自动修正温度波动引起的测量误差,配合SQL数据库实现检测数据可追溯管理。实践表明,该方案使产品出厂合格率从92.4%提升至98.7%,人工复检工作量降低65%。
典型行业应用场景
在智能马桶进水阀生产线中,系统部署于总装工位前端的质量控制点。当检测到螺纹中径偏差超过0.05mm时,自动触发声光报警并隔离缺陷件。浙江某上市卫浴企业应用案例显示,系统成功识别出传统检具难以发现的渐进性磨损缺陷,提前12天预警模具更换需求。通过与MES系统集成,实现质量数据与生产工艺参数的动态优化,使同类产品漏水投诉率下降41%。
全流程质量保障体系
构建包含设备层、数据层、决策层的三级质控网络:设备层采用冗余设计的双PLC控制系统保障运行稳定性;数据层通过区块链技术实现检测记录防篡改存储;决策层运用SPC统计过程控制模型进行趋势预警。在广东某OEM工厂的验收测试中,系统连续运行120小时无故障,检测一致性方差控制在0.002mm²以内。配套的校准体系包含每周基准件校验和季度第三方计量认证,确保检测系统持续符合JJF 1104-2018计量规范要求。
## 发展趋势与策略建议展望未来,建议从三个维度深化技术应用:首先开发支持5G传输的移动检测终端,拓展售后服务质量监控场景;其次构建行业级螺纹特征数据库,为工艺改进提供数据支撑;最后推动制定《智能螺纹检测设备通用技术要求》团体标准,促进行业检测技术规范化发展。通过产学研深度合作,有望在2026年前将检测系统成本降低40%,推动该项技术在中小型制造企业的普及应用。
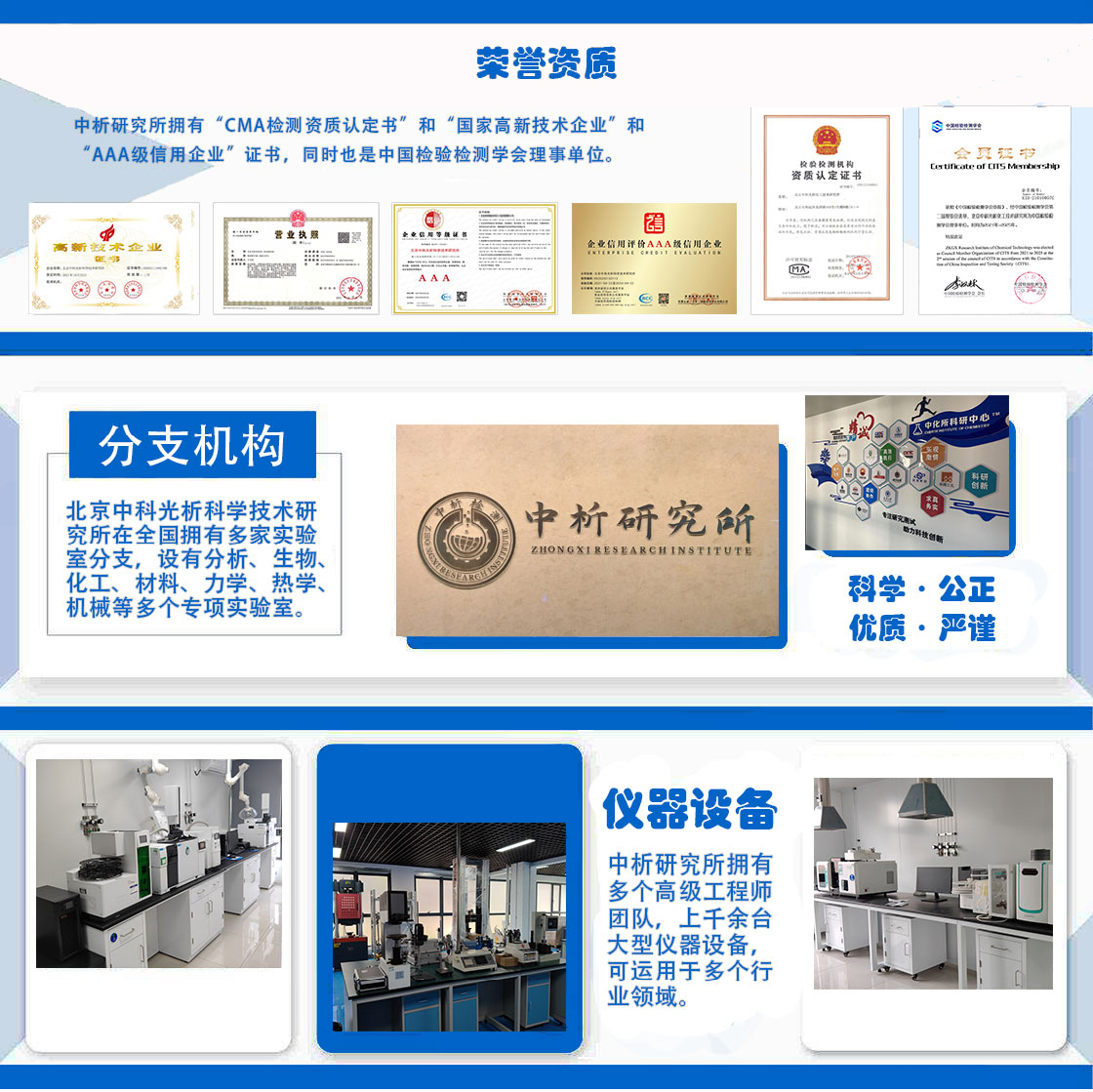
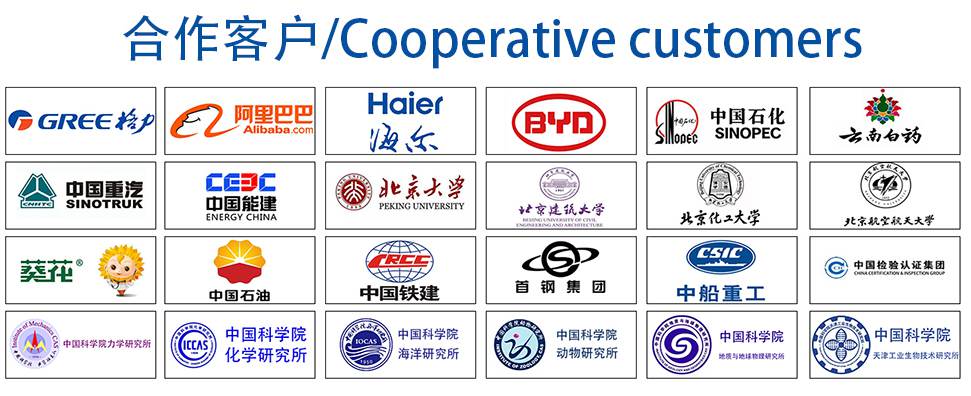