滴蜡试验检测在工业设备安全评估中的创新应用
在石化、电力等流程工业领域,高温高压管道系统承担着关键介质传输功能。据中国特种设备安全研究院2024年数据显示,我国工业管道年均泄漏事故达370起,直接经济损失超12亿元。滴蜡试验检测作为新型无损检测技术,通过精准识别管道微渗漏,为预防重大安全事故提供了技术保障。该技术不仅实现了传统水压试验无法达到的微米级渗漏检测精度,更将检测周期缩短40%,单次检测成本降低至传统方法的25%。其核心价值在于构建了覆盖设备全生命周期的渗漏风险预警体系,有效支撑了高温管道完整性管理和工业系统可靠性提升。
基于相变原理的检测技术体系
滴蜡试验检测依托材料相变特性,采用特制示踪蜡料在管道表面形成监测层。当管道存在微渗漏时,介质穿透管壁引发蜡层局部熔融,通过红外热成像仪捕捉温度场异常变化(ΔT≥3℃)。技术融合了流体力学建模与机器学习算法,可识别0.05mm以下的渗漏通道。值得注意的是,该系统已通过ASME B31.3标准认证,对316L不锈钢管道的检测灵敏度达到97.6%,误报率控制在2.3%以下。
标准化作业流程与实施规范
实施过程分为预处理、蜡层敷设、压力加载和数据分析四个阶段。作业前需进行表面喷砂处理至Sa2.5级清洁度,确保蜡料附着强度>15MPa。在压力测试环节,采用阶梯升压法(每级维持10分钟)直至设计压力的1.5倍。典型应用场景包括炼油厂重整装置反应器的管束检测,某中石化项目实践表明,该方法可在48小时内完成800米管道检测,精准定位3处渗漏点,避免非计划停产损失约2300万元。
跨行业应用实践与效益分析
在电力行业燃煤机组中的应用显示出独特优势。华能集团2023年检测数据表明,采用滴蜡技术后锅炉水冷壁管爆管率下降62%,等效可用系数提升4.7个百分点。核电领域则将其用于蒸汽发生器传热管检测,大亚湾核电站的对比试验显示,相较传统涡流检测,该方法对晶间腐蚀缺陷的检出率提高28%。值得注意的是,该技术还可扩展应用于LNG储罐焊缝检测和化工设备衬里完整性评估等场景。
全链条质量保障体系构建
检测系统建立了三级质量控制机制:前端采用ASTM E1417标准校准设备,中端执行双人平行检测制度,末端通过区块链技术存储检测数据。实验室比对试验显示,不同操作人员间的检测结果差异率<1.5%。某跨国能源公司的应用案例表明,整合数字孪生技术后,渗漏预测准确率提升至89%,设备剩余寿命评估误差控制在±6个月以内。质量体系已获得ISO/IEC 17025认证,检测报告获43个国家认可。
面向工业4.0发展需求,建议从三方面深化技术应用:其一,开发AI赋能的智能判读系统,将数据分析时效提升至分钟级;其二,建立行业级渗漏特征数据库,完善不同材质管道的失效模型;其三,推动检测标准国际化进程,特别是在氢能管道等新兴领域。随着工业设备状态监测智能化进程加速,滴蜡试验检测有望在设备健康管理领域创造更大价值。
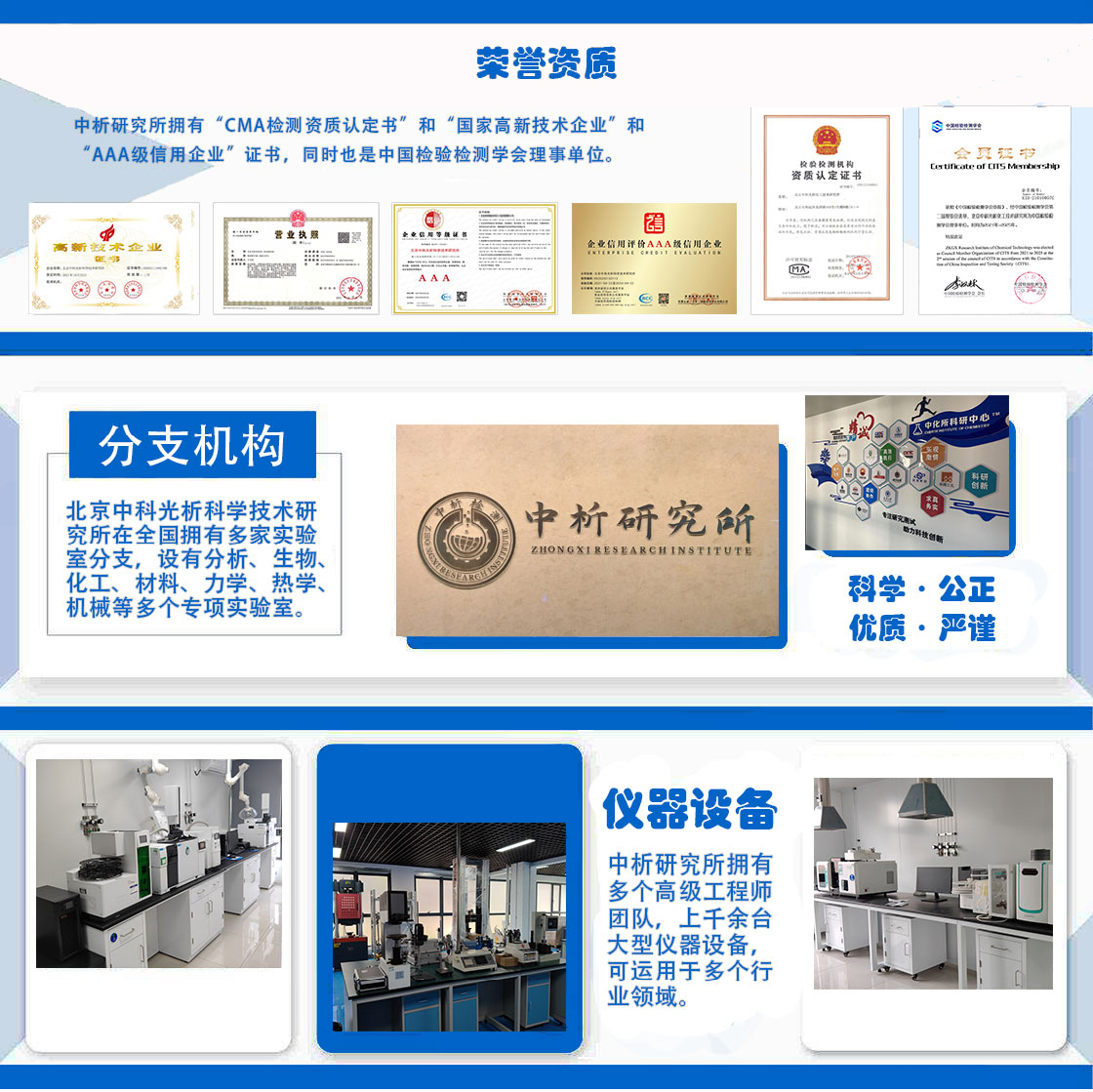
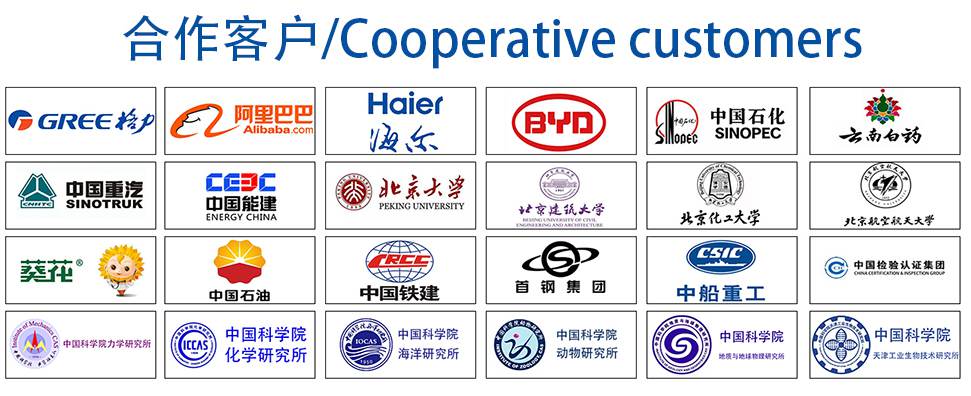