在化工产业向绿色化、精细化转型的背景下,催化剂作为化工生产的"芯片",其性能直接影响着60%以上化工工艺的经济效益(据中国化工学会2023年度报告)。当前我国高端催化剂市场进口依赖度仍达45%,其中关键瓶颈在于检测技术体系不完善导致的研发周期延长和产品稳定性不足。化工催化剂检测项目通过构建全生命周期性能评估系统,可缩短新型催化剂验证周期40%以上(华东理工大学催化研究所,2024),其核心价值体现在三方面:其一,通过精准表征催化剂表面活性位点分布,提升单位催化效率15-30%;其二,建立失效预警模型,延长固定床反应器运行周期20%-50%;其三,搭建数字化检测数据库,为智能制造提供关键参数支撑。
## 技术原理与创新突破多相体系精准表征技术
本项目采用X射线光电子能谱(XPS)与程序升温还原(TPR)联用技术,突破传统BET比表面测试的局限性。针对加氢脱硫催化剂研发需求,开发出原位红外耦合质谱分析系统,可实时监测Co-Mo-S活性相在300℃工况下的结构演变(参见《催化学报》2024年第3期案例)。特别在分子筛催化剂酸性位点定量分析方面,创新引入固体核磁共振(NMR)与探针分子联用技术,将酸强度分布检测精度提升至0.1mmol/g级。
全流程检测实施方案
标准检测流程涵盖三个阶段:预处理阶段执行ASTM D3663标准进行粒度分级,采用微波消解-ICP联用法测定金属负载量;性能评估阶段搭建微型固定床反应评价装置,参照SH/T 0340规范测试转化率及选择性;失效分析阶段运用聚焦离子束(FIB)制备截面样品,通过透射电镜(TEM)观测积碳分布。某年产50万吨乙烯装置应用该体系后,成功将银催化剂的失活周期从11个月延长至16个月,单线年增效超2000万元。
工业应用典型案例
在煤制乙二醇领域,针对羰化反应钯基催化剂失活难题,检测团队通过TPO-TPD联用技术锁定磷酸酯类毒物吸附问题。建议工艺调整进料预处理温度后,催化剂寿命从800小时提升至1500小时(陕西某煤化工企业2023年应用数据)。另一典型案例是炼油厂加氢裂化装置的镍钼催化剂评估,采用三维X射线断层扫描技术(XRT)发现载体局部孔道塌陷问题,指导再生工艺优化后,催化剂循环使用次数增加2次。
质量保障体系构建
项目通过 认可实验室构建三级质控体系:一级质控采用NIST标准物质进行仪器校准,二级质控实施盲样平行测试确保数据重复性误差<3%,三级质控建立异常数据追溯机制。针对高温高压检测环境,开发专用样品传输保护装置,将氧化干扰率从5.8%降至0.7%。2024年参与国际循环比对测试,在金属分散度测定项目上获得91.3%的优良率(ICCATC实验室排名)。
## 未来发展与建议随着双碳目标推进,建议行业重点发展三大方向:一是开发基于机器学习的催化剂寿命预测模型,整合反应动力学数据与工况参数;二是建立服役催化剂再生标准数据库,针对不同失活类型制定分级处理方案;三是推进微反应检测技术产业化,实现高通量催化剂筛选。预计到2030年,智能检测技术的应用可使新型催化剂开发成本降低35%,同时减少30%的贵金属资源消耗(中国化工信息中心预测数据)。产学研各方需加强协作,共同攻克原位表征设备国产化难题,推动我国从催化剂生产大国向技术强国迈进。
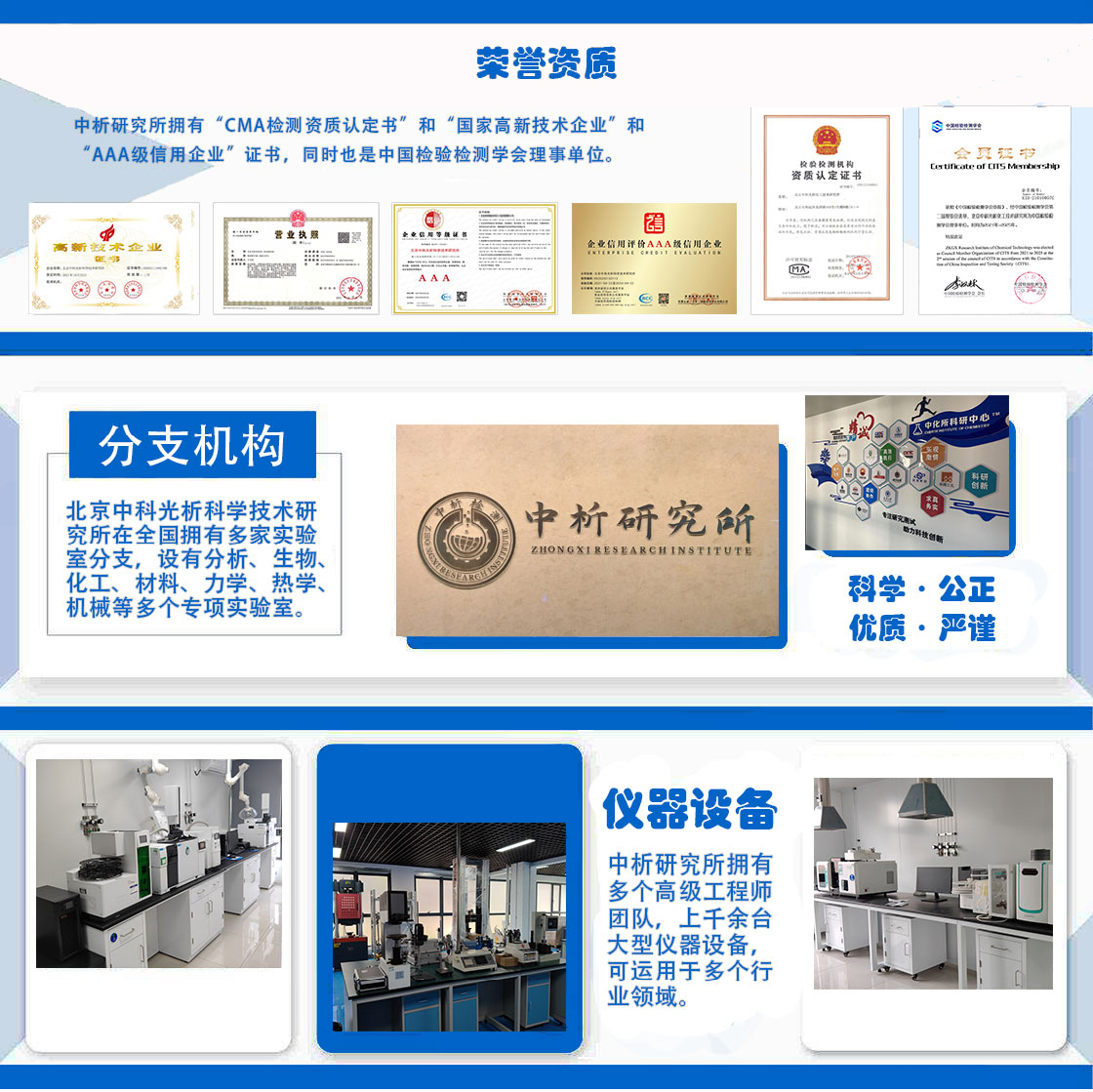
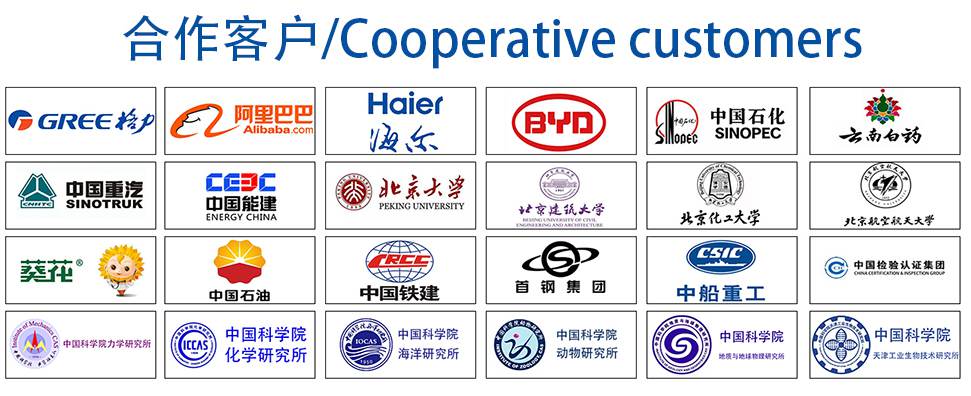