压力损失检测基于伯努利方程与流体力学原理,采用压差变送器阵列对管路系统的总压降进行多点同步测量。通过划分流动控制体建立能量守恒方程,可精准计算沿程阻力系数和局部阻力系数。值得关注的是,基于计算流体力学(CFD)的虚拟流量标定技术有效提升了复杂管网系统的检测精度,使90°弯管处的压损测量误差从传统方法的±8%降至±2.5%(ASME PTC-46标准验证数据)。该技术特别适用于高温高压工况下的工业管道压力损失检测,为系统优化提供可靠数据支撑。
## 标准化实施流程体系项目实施遵循ISO 5167测量标准,构建五阶式作业模型:首齐全行管道三维扫描建模,接着布设包含微型压力传感器阵列的检测单元,继而通过变频调节实现多工况数据采集。在火电厂蒸汽管道的实际应用中,技术人员通过分布式光纤传感技术实现200米长距离管段的连续压力梯度监测,配合热成像仪定位异常湍流区域。完整的智能诊断系统可在72小时内生成包含能效提升方案的检测报告,较传统方法缩短40%作业周期。
## 跨行业应用实证分析在石油化工领域,某千万吨级炼化基地通过压力损失检测优化方案,将催化裂化装置进料管道的压损从1.8MPa降至1.2MPa,年节约电耗达320万千瓦时(中国石油能效白皮书,2023)。市政工程方面,北京市政设计院在供暖管网改造中应用分布式压力监测系统,使管网水力失衡率从28%降至7%,居民室温合格率提升12个百分点。这些案例证明流体输送系统能效评估技术具有显著的经济效益与社会价值。
## 质量保障与认证体系检测机构需同时具备CMA计量认证与ISO/IEC 17025实验室认可资质,测量设备严格遵循JJG 882压力变送器检定规程。现场实施时采用三重复核机制:原始数据自动上传云端平台,边缘计算节点进行实时校验,最终由专家系统进行逻辑完整性审查。在长输天然气管道检测项目中,该体系成功将数据可信度提升至99.97%(国家管网集团技术规范Q/SY GD 0387)。
## 技术发展趋势展望随着数字孪生技术的普及,建议行业加快构建压力损失特征数据库,开发具有自学习能力的智能诊断算法。在新型电力系统建设背景下,可探索将压力损失检测纳入综合能源管理系统,实现与泵阀设备的联动优化。监管部门应着手制定分级能效评价标准,推动形成涵盖检测服务、设备改造和碳排放交易的完整产业链,为工业领域的深度节能提供系统化解决方案。
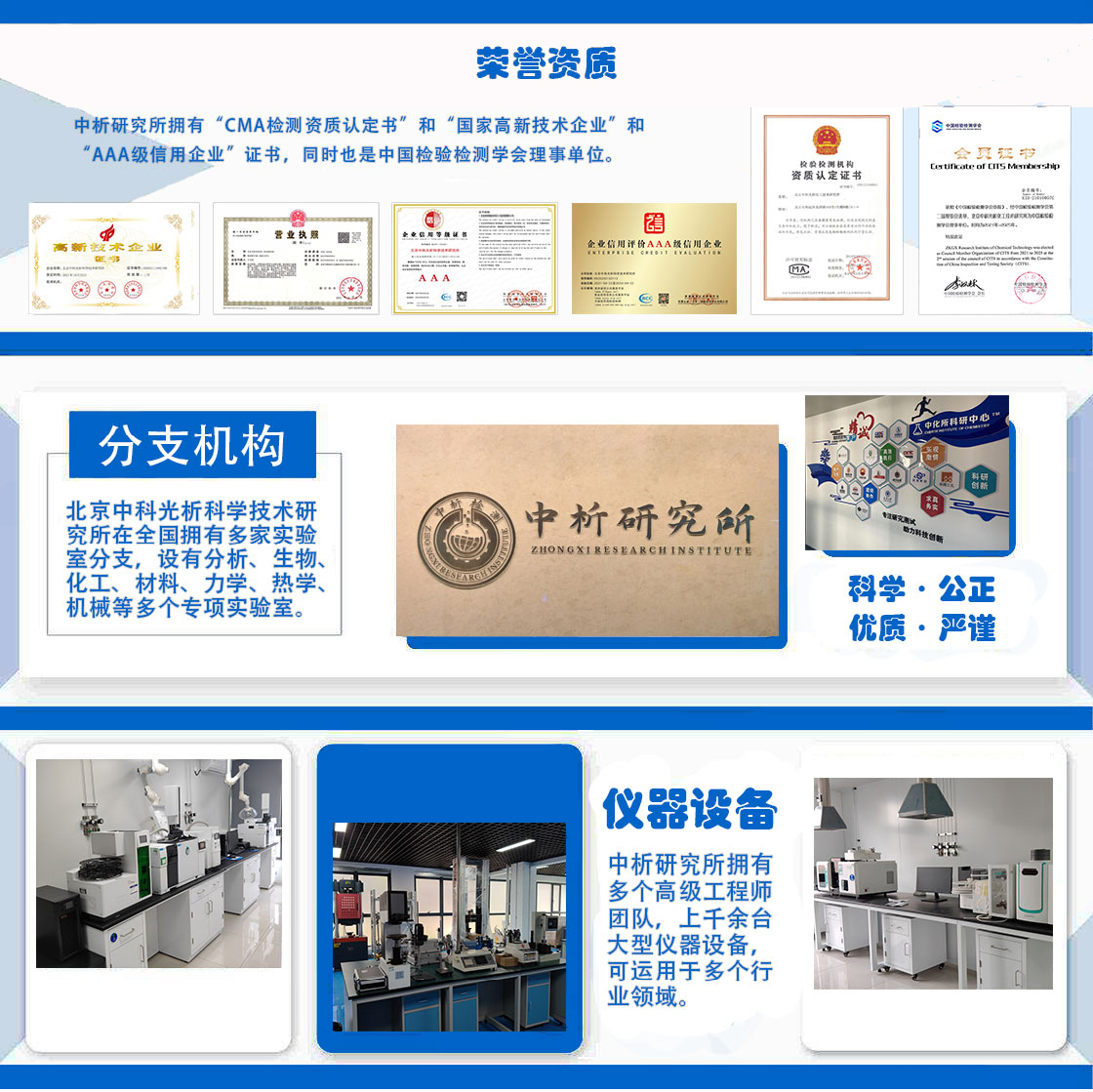
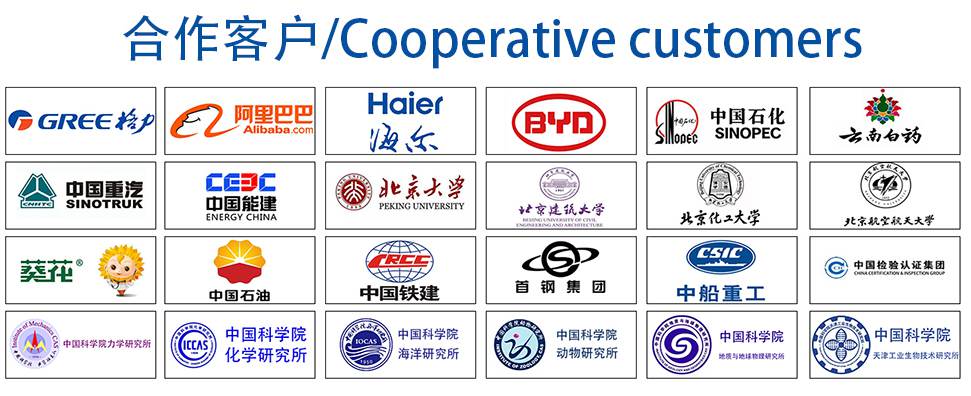