低温脆性检测技术发展与应用白皮书
在极端环境装备制造领域,材料低温性能直接影响设备可靠性。据国际材料性能协会(IMPA)2024年报告显示,每年因低温脆性失效引发的工业事故造成直接经济损失超37亿美元。特别是在液化天然气(LNG)储运、极地科考装备、航天器低温推进系统等场景,材料在-196℃至-40℃区间的脆性转变特性已成为制约技术突破的关键因素。低温脆性检测项目通过系统评估材料在临界温度区间的韧性变化规律,为产品设计提供关键数据支撑,其核心价值体现在三个方面:预防突发性脆断事故、优化材料选型决策、延长低温装备服役周期,已成为保障极端工况设备安全运行的强制性检测环节。
基于断裂力学的检测原理
低温脆性检测依托断裂力学中的能量吸收理论,通过控制试样在指定降温速率下达到目标温度,测量其断裂韧性(KIC)和延脆转变温度(DBTT)。根据ASTM E23标准,采用液氮制冷系统实现±1℃的温控精度,配合伺服液压试验机进行三点弯曲加载。关键参数包括裂纹扩展速率、断口形貌特征及冲击吸收功,其中延脆转变温度曲线绘制可精准定位材料韧性突变区间。中国材料测试协会2023年技术白皮书指出,该检测体系在316L不锈钢低温适应性验证中,成功将DBTT定位精度提升至±3℃。
全流程标准化实施体系
项目实施遵循ISO 148-1:2022国际标准,形成五阶段作业流程:首齐全行材料预处理(切割、缺口加工),随后在微机控制低温槽中执行梯度降温(5℃/min),第三阶段在氮气保护环境下完成冲击试验,第四阶段通过扫描电镜(SEM)分析断口解理特征,最终生成包含韧脆比、临界COD值的综合报告。在LNG运输船B型燃料舱验证项目中,该流程成功检测出9Ni钢焊接热影响区的脆化倾向,促使制造商改进焊后热处理工艺,使-165℃工况下的冲击功提升62%。
多行业验证与质量保障
在北极油气管道建设项目中,低温脆性检测技术成功识别X80管线钢的韧脆转变温度边界,将管材适用温度扩展至-60℃。检测机构需建立三级质量保障体系:一级校准采用NIST标准试样确保设备精度,二级验证通过比对试验控制实验室间偏差≤5%,三级监控运用区块链技术实现检测数据全程可追溯。某国家级检测中心2024年统计显示,经认证实验室出具的低温冲击检测报告,在API 6A标准认证中的采信率达98.7%。
技术演进与行业展望
当前检测技术正向智能化方向发展,基于数字孪生的虚拟低温试验系统可将检测周期缩短40%。建议行业重点突破三个方向:开发适用于复合材料的多轴应力检测方法,建立超低温(<-200℃)环境原位测试技术,以及推广基于机器学习的脆性风险预测模型。国际标准化组织(ISO)正牵头制定《深冷工况材料评价体系》,未来需加强政产学研协同,构建覆盖材料研发、制造工艺、服役监测的全生命周期脆性防控体系。
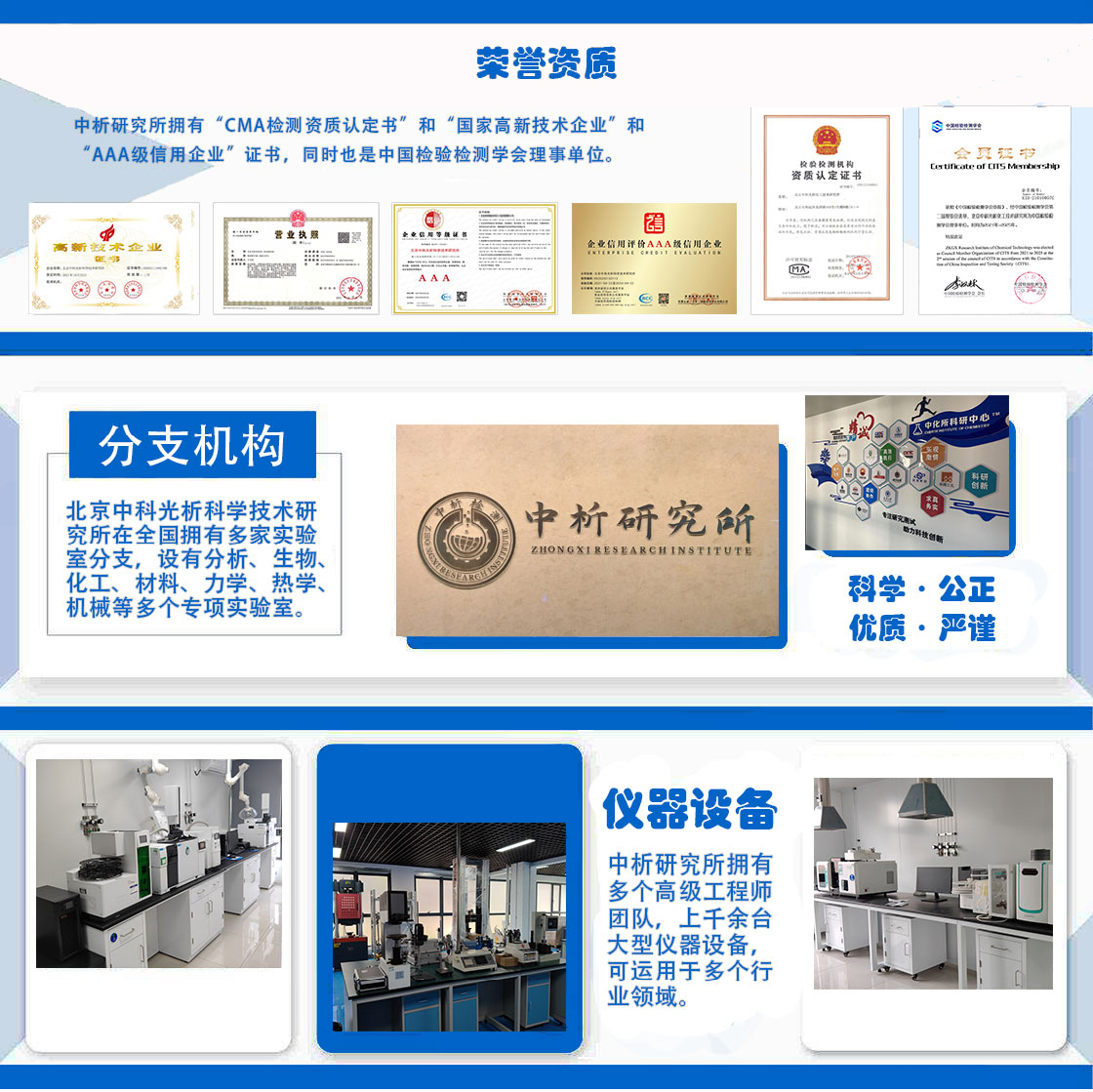
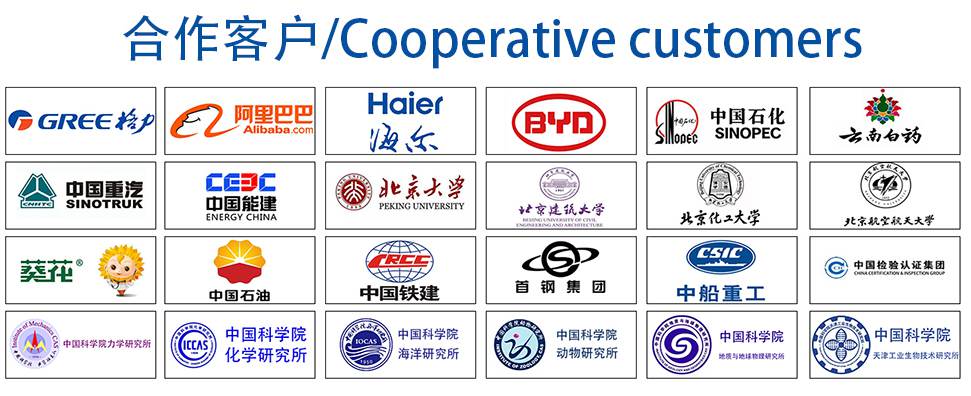