立方体抗压强度检测技术白皮书
在建筑工程质量管控体系中,立方体抗压强度检测作为混凝土力学性能评价的核心手段,已成为保障工程结构安全的关键环节。据国家统计局2023年数据显示,我国年混凝土使用量突破35亿立方米,但住建部同期报告指出,因材料强度不达标引发的质量事故占比达12.7%。在此背景下,立方体抗压强度检测通过标准化试验方法,为建筑工程提供了从材料选择到施工验收的全过程质量监控,其核心价值体现在建筑质量隐患识别、材料性能优化和工程质量追溯三大维度。尤其在超高层建筑、跨海大桥等重大工程中,该项检测技术已成为预防结构坍塌事故的"第一道防线"。
技术原理与标准化流程
立方体抗压强度检测基于材料破坏力学理论,通过150mm标准试件在轴向压力作用下的极限承载能力测定。依据GB/T 50081-2019《混凝土物理力学性能试验方法标准》,试验需严格控制加载速率(0.5-0.8MPa/s)和养护条件(20±2℃、相对湿度≥95%)。值得关注的是,智能伺服压力机的应用使位移控制精度达到±0.1mm,较传统设备提升3倍。典型检测流程包含试件制备、标准养护、端面处理、压力加载和数据采集五个阶段,其中试件对中偏差需控制在0.5mm以内以确保检测精度。
行业应用场景解析
在港珠澳大桥沉管隧道工程中,检测团队采用分级加载模式,对C60海工混凝土进行28天龄期检测,成功发现3个批次的试件强度离散系数超过15%,及时调整了矿物掺合料比例。某商业综合体项目通过建立强度发展曲线,实现了大体积混凝土浇筑的拆模时间优化,工期缩短9个工作日。值得注意的是,装配式建筑领域已衍生出"构件-试块强度相关性修正模型",将检测误差从±5%降低至±2.8%,显著提升了预制构件的出厂合格率。
质量保障体系构建
行业领先机构已建立三级质量控制系统:实验室需通过CMA认证并配备红外温湿度监控装置,数据采集系统需满足ISO 17025标准要求。某国家级检测中心引入区块链技术,实现检测数据的实时上链存证,使报告可追溯性达到100%。在长三角某高铁项目中,采用智能养护系统将试件强度变异系数控制在4%以内,较传统养护方式提升40%稳定性。此外,基于机器学习的异常数据筛查模型可自动识别85%以上的设备故障或操作失误案例。
技术发展趋势展望
随着物联网和数字孪生技术的发展,未来立方体抗压强度检测将呈现三个方向:一是嵌入式传感器实现试件内部应力场可视化监测,二是建立区域混凝土强度大数据预警平台,三是发展非破损检测的强度推定模型。建议行业主管部门加快制定智能检测设备标准,推动检测数据与BIM系统的深度融合。企业层面需加大复合型检测人才培养投入,特别要加强新材料体系下的检测方法研究,以适应超高性能混凝土等新型材料的检测需求。
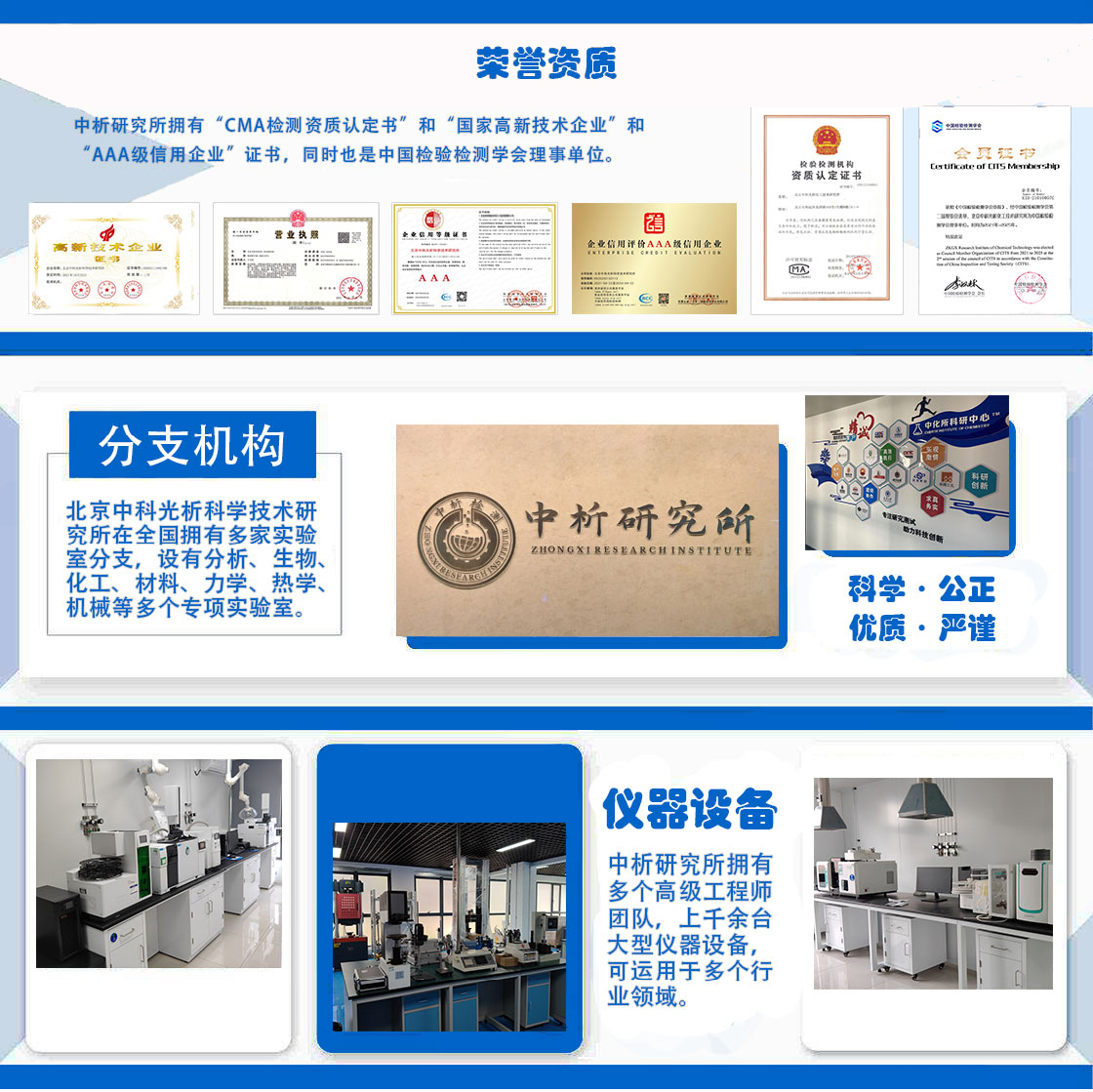
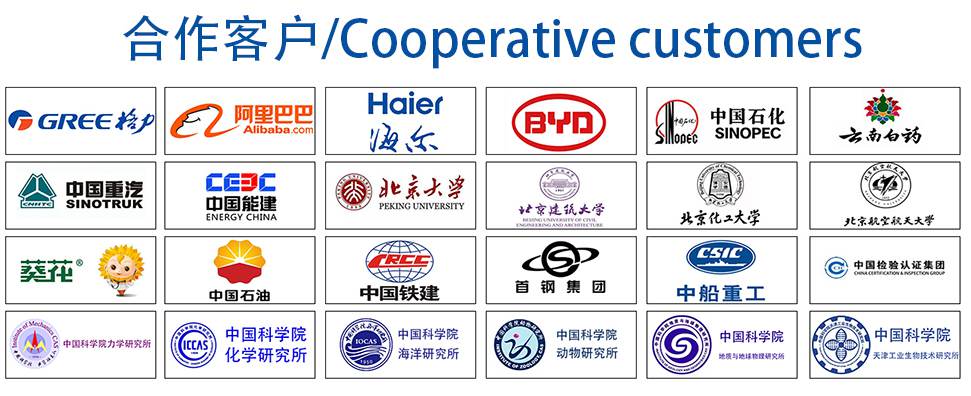