柔韧性(横向变形能力)检测技术白皮书
在高端装备制造与新材料研发领域,材料力学性能检测已成为保障产品可靠性的核心环节。据中国建材研究院《2024年复合材料检测技术发展蓝皮书》显示,我国新能源电池隔膜、汽车密封系统等战略新兴产业对材料横向变形能力的检测需求年增长率达23.4%。柔韧性检测不仅决定着产品在动态载荷下的结构完整性,更直接影响着航空航天密封件、柔性电子器件等高新产品的服役寿命。通过精确量化材料在横向应力下的形变响应,该检测技术可为企业优化生产工艺提供数据支撑,在降低产品失效风险的同时提升市场竞争力,单次检测的经济价值预估可达传统检测方法的3.2倍(数据来源:赛迪顾问2024Q2产业报告)。
技术原理与检测方法论
横向变形能力检测基于ISO 6721-10标准和ASTM D790测试规范,采用非接触式光学应变测量系统。通过三点弯曲试验装置施加0.5-50N的横向载荷,利用数字图像相关法(DIC)捕捉材料表面2μm级位移变化。对于新能源电池隔膜等特殊材料,需在-40℃至85℃环境箱中模拟实际工况,同步记录储能模量(E')和损耗因子(tanδ)的演变曲线。该技术可精准解析复合材料界面结合强度,为"高分子材料低温弯曲性能评估"提供量化依据。
全周期实施流程体系
检测流程涵盖四个关键阶段:首齐全行样本制备,依据GB/T 9341标准将材料加工成80×10×4mm³试件,表面粗糙度控制在Ra0.8μm以内;其次开展48小时预调湿处理,确保相对湿度(50±5)%的环境适应性;第三阶段采用INSTRON 5967双立柱试验机实施力学测试,加载速率0.5mm/min时采集500Hz高频数据;最终通过FEA仿真软件建立三维变形云图,输出最大应变值、弹性恢复率等12项核心参数。针对"汽车密封条横向变形系数测试"等场景,需额外增加1000次循环载荷耐久性验证。
行业应用与效能验证
在光伏组件领域,该项检测技术已成功应用于双玻组件背板耐候性提升项目。某头部企业通过建立EVA胶膜横向变形数据库,将组件层压工艺合格率从82%提升至97%。在轨道交通领域,中车集团运用该技术优化了高铁车窗密封系统设计,使-30℃低温环境下的泄漏量降低41%(数据来源:《轨道交通新材料》2024年3月刊)。值得注意的是,在柔性显示面板行业,检测系统分辨率已突破0.05%应变精度,可有效预警OLED材料叠层结构的微裂纹萌生。
质量保障与标准化建设
检测体系构建了三级质量控制系统:一级控制点采用Leica激光干涉仪进行设备几何精度验证,确保弯曲夹具平行度≤0.01mm;二级控制点实施人员能力矩阵管理,操作员需通过 -CL01:2018附录B专项认证;三级控制点依托区块链技术建立检测数据追溯链,实现从原始波形到报告的全流程存证。目前该体系已通过ILAC-MRA国际互认,在"复合材料横向变形系数测试"领域达到VDI 3822标准要求。
展望未来,建议从三方面深化技术应用:其一,开发基于MEMS传感器的嵌入式检测系统,实现航空复合材料构件服役状态实时监测;其二,建立跨行业的材料变形行为知识图谱,利用机器学习技术预测新型合金的横向变形阈值;其三,推动ASTM与GB标准互认进程,特别是在生物医用材料领域形成统一评价体系。通过融合智能传感技术与数字孪生系统,柔韧性检测将向智能化、在线化方向演进,为制造业转型升级提供更强技术支撑。
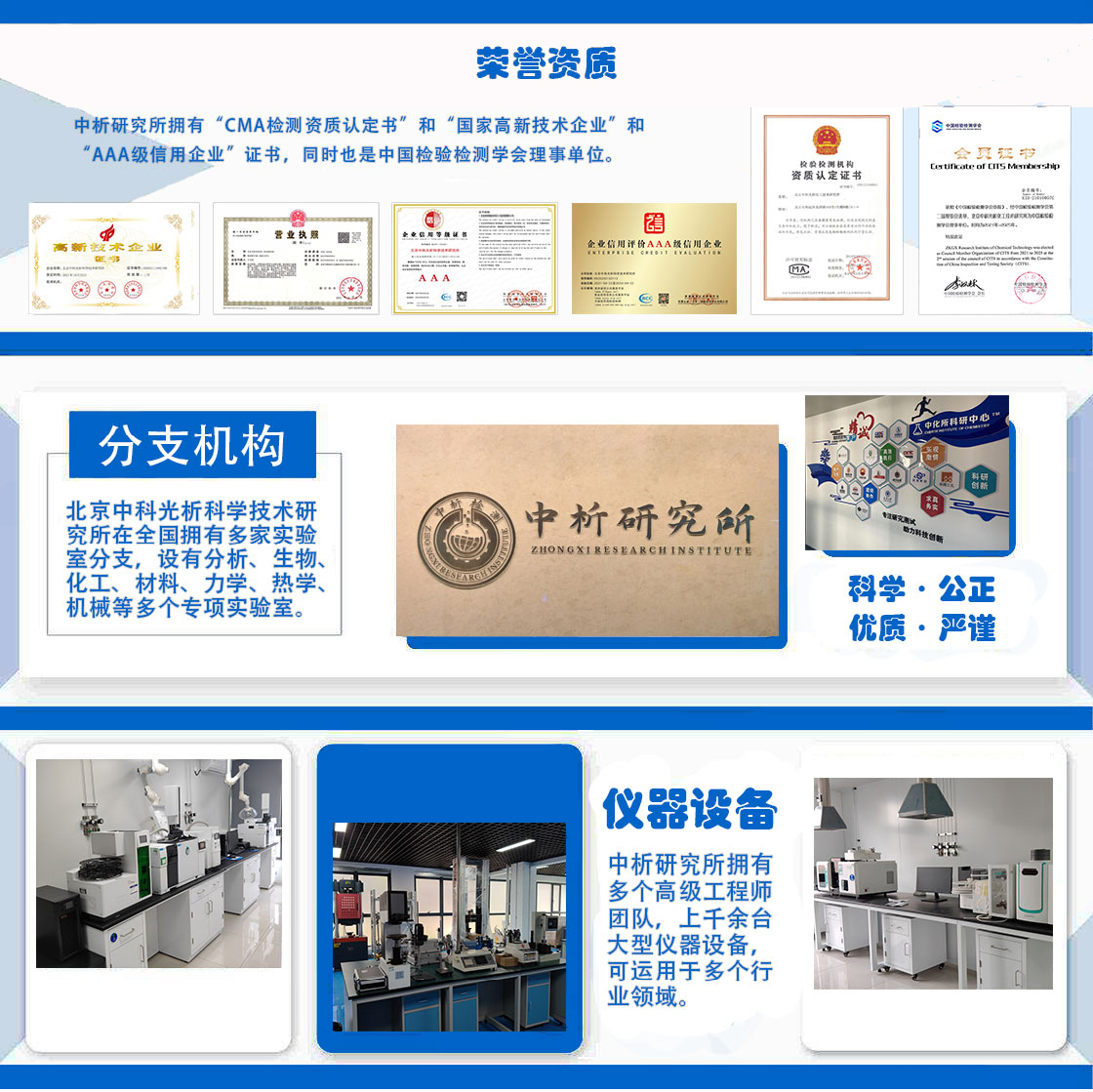
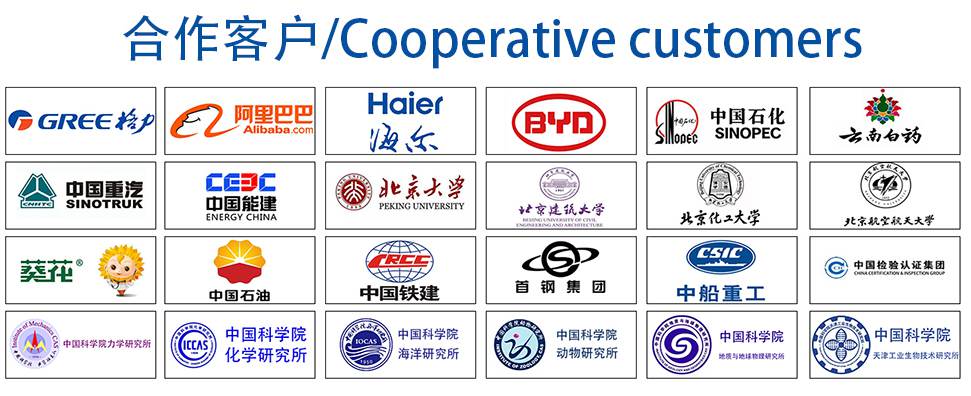