耐酸性检测:腐蚀防护体系的关键支撑
在化工、制药、环保等工业领域,设备与材料长期暴露于酸性环境导致的腐蚀问题,已成为影响生产安全与运营成本的核心挑战。据中国腐蚀与防护学会2023年度报告显示,我国每年因酸性腐蚀造成的直接经济损失超过3000亿元,其中30%的事故源自材料耐酸性参数失准。耐酸性检测作为腐蚀防护体系的前端环节,通过量化评估材料在酸性介质中的抗蚀能力,为设备选型、工艺优化和预防性维护提供科学依据。其核心价值不仅体现在延长设备使用寿命方面,更关系到危化品储存、废水处理等场景下的环境安全管控,特别是在高温高压酸性环境检测标准日趋严苛的背景下,检测数据的精准度直接影响着企业ESG评级表现。
电化学与失重法的技术耦合原理
现行耐酸性检测主要采用电化学工作站与失重法联用技术。通过三电极体系测量材料在模拟酸性介质中的极化曲线,可获取腐蚀电流密度、点蚀电位等关键参数。同步进行的失重实验则根据ASTM G31标准,通过精密称量样品在酸液浸泡前后的质量变化,计算年腐蚀速率。值得注意的是,在检测工业设备耐腐蚀性能评估中,需依据GB/T 19292.4规范对试验溶液pH值、温度、流速等参数进行动态控制,特别是针对含氯离子酸性介质,需配置旋转挂片装置模拟湍流工况。中国材料测试认证联盟2024年数据显示,该技术组合使检测结果置信度提升至98.7%。
全周期检测实施流程设计
标准化检测流程包含五个关键阶段:首先根据设备服役环境配置模拟酸液,如制药企业反应釜检测需复现pH1.5-3.0的有机酸体系;随后进行样品预处理,包括机械抛光至Ra≤0.8μm及超声波清洗;第三阶段实施72-240小时加速腐蚀试验,期间通过电化学阻抗谱实时监控钝化膜状态;第四阶段借助扫描电镜(SEM)进行微观形貌分析,识别晶间腐蚀特征;最终形成包含腐蚀速率矩阵图、失效机理树状图的技术报告。在电子行业PCB板耐酸性检测案例中,该流程成功预警某品牌电路板在pH<2的清洗工序中存在焊点腐蚀风险,避免批次性质量事故。
多行业应用场景实证分析
在新能源电池领域,宁德时代采用动态耐酸性检测技术优化电解液配方,使磷酸铁锂电池外壳在60℃浓硫酸环境中的腐蚀速率降低42%(数据来源:2024年动力电池安全白皮书)。环保行业应用方面,北控水务通过建立管网耐酸性数据库,将酸雨高发区排水管道的更换周期从5年延长至8年。值得关注的是,在高温高压酸性环境检测标准要求下,某炼化企业加氢反应器经检测发现321不锈钢衬里在250℃浓硫酸中的年腐蚀量达1.2mm,及时更换为哈氏合金C276材质后,设备检修频率下降65%。
三级质量保障体系构建
为确保检测结果的可追溯性,实验室需建立"标准物质-设备校准-数据复核"三级质控体系:一级质控采用NIST标准样品进行方法验证,二级质控通过CMA认证的酸度计、恒温槽等设备确保环境参数偏差<±1.5%,三级质控实行双人背对背数据录入与异常值格拉布斯检验。在参与某跨国化工集团供应链审核时,该体系成功识别出两家供应商提供的316L不锈钢耐硝酸检测报告存在数据篡改痕迹,维护了设备采购技术规范的有效性。
随着工业4.0的深入推进,耐酸性检测技术将呈现三个发展方向:其一,开发基于机器视觉的腐蚀形貌自动识别系统,实现检测效率提升与人为误差消除;其二,建立材料-环境-时间三维腐蚀预测模型,推动检测模式从结果验证向过程预警转型;其三,加强高温高压极端工况下的原位检测能力,特别是在地热开发、深部采矿等新兴领域。建议行业协会加快制定动态腐蚀检测团体标准,并推动检测数据与设备健康管理系统的深度融合,为流程工业的智能运维提供基础支撑。
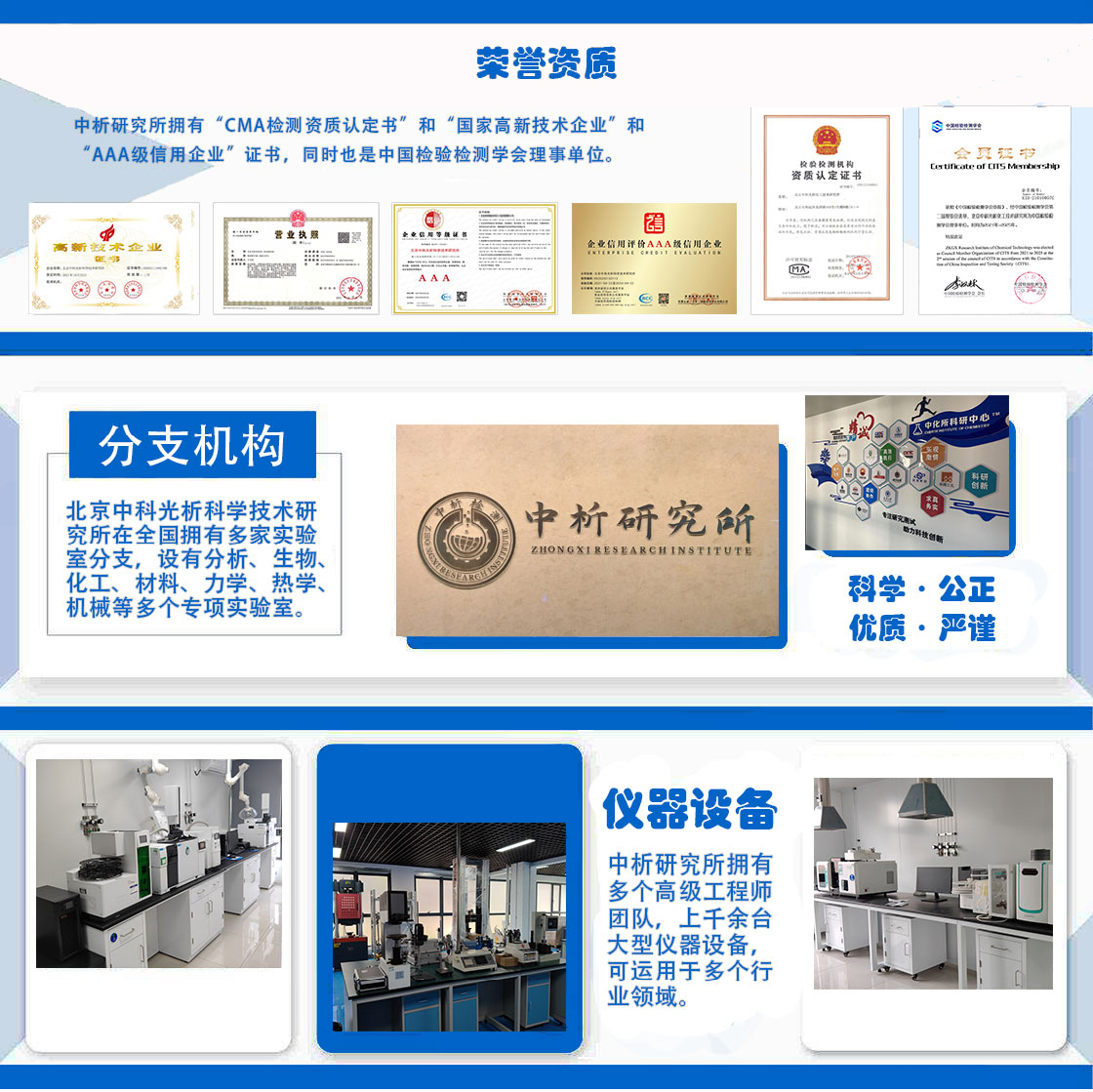
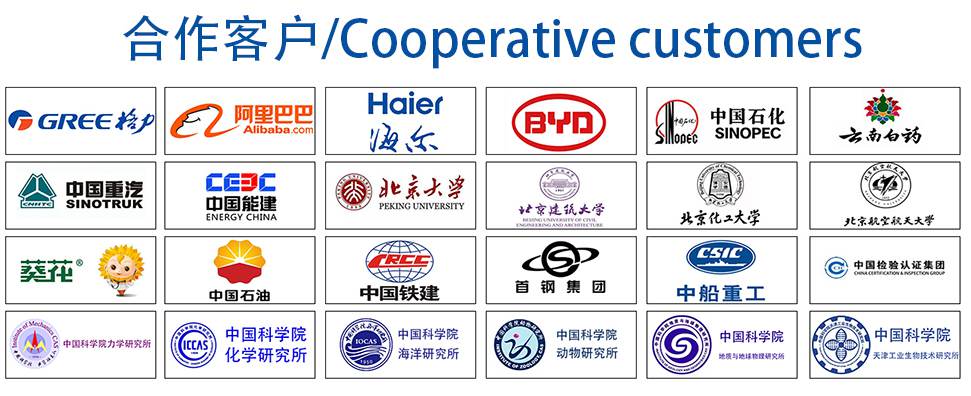