在工业制造与基础设施建设领域,材料抗腐化性检测已成为保障设备长效运行的核心环节。据中国腐蚀与防护学会2023年研究报告显示,我国每年因腐蚀造成的经济损失达2.5万亿元,约占GDP的3.34%。在此背景下,抗腐化性检测项目通过精准评估材料在特定环境中的耐蚀性能,为装备制造、海洋工程、能源化工等行业提供关键质量控制依据。其核心价值不仅体现在延长设备服役周期(平均提升30%使用寿命),更通过预防性检测降低突发性腐蚀事故风险,仅石化行业每年可减少数百亿元非计划停机损失。
多维度检测技术原理体系
抗腐化性检测融合了电化学阻抗谱(EIS)、盐雾加速腐蚀试验与微观形貌分析三重技术路径。其中,ASTM B117标准下的中性盐雾试验可模拟海洋大气环境,通过72-2000小时连续喷雾量化材料失重率。电化学工作站则通过极化曲线测定腐蚀电流密度,精准度可达微安级。在高端装备领域,同步辐射X射线断层扫描技术可三维重构材料亚表面腐蚀形貌,检测分辨率突破0.1μm。此类技术组合已形成完整的“宏-介-微观”长效防腐材料评估标准体系。
全周期质量控制实施流程
项目实施遵循ASTM G193多级递进式流程:前期基于服役环境大数据建立腐蚀图谱数据库,中期采用循环腐蚀试验箱模拟温湿度交变工况,后期结合工业CT进行关键部件无损检测。某海上风电运维企业应用该流程后,塔筒法兰连接件的腐蚀失效预警准确率提升至98.6%,据国际材料测试协会2024年报告,该数据较传统方法提高42%。特别在深海油气管道检测中,通过植入式光纤传感器实现了365天/24小时的实时腐蚀监测解决方案。
跨行业应用场景实践
在港珠澳大桥工程中,项目团队采用梯度盐雾-干湿循环复合试验法,成功筛选出氯离子渗透率低于0.25%的混凝土配方。轨道交通领域,基于机器视觉的钢轨腐蚀智能检测系统已在京沪高铁部署,单日检测里程突破800公里,误报率控制在0.3%以下。值得注意的是,新型氢能储运设备制造商通过引入高温高压H₂S应力腐蚀试验方案,使储罐设计寿命从15年延长至25年,该项突破被纳入2024年国家氢能产业白皮书推荐技术。
标准化质量保障体系构建
项目执行严格遵循ISO 17025实验室管理体系,建立从试剂标定到数据溯源的12级质控节点。检测设备均配备NIST可追溯校准证书,关键试验箱温度波动度控制在±0.5℃。人员资质方面,要求腐蚀检测工程师持有NACE CIP三级认证,并定期参与ASM International组织的失效分析培训。第三方比对试验显示,该体系下检测结果的实验室间差异从7.8%降至1.2%,达到航空级质量控制标准。
面对新型复合材料的广泛应用,建议行业重点发展基于人工智能的腐蚀预测模型,整合材料基因组数据库与服役环境大数据。同时需要加强极端环境(如深地、深空)腐蚀检测标准研究,推动建立跨境检测结果互认机制。据腐蚀联合会预测,至2030年智能腐蚀监测解决方案市场规模将突破900亿元,这要求检测机构加快数字化转型,构建覆盖“检测-诊断-防护”的全产业链服务体系。
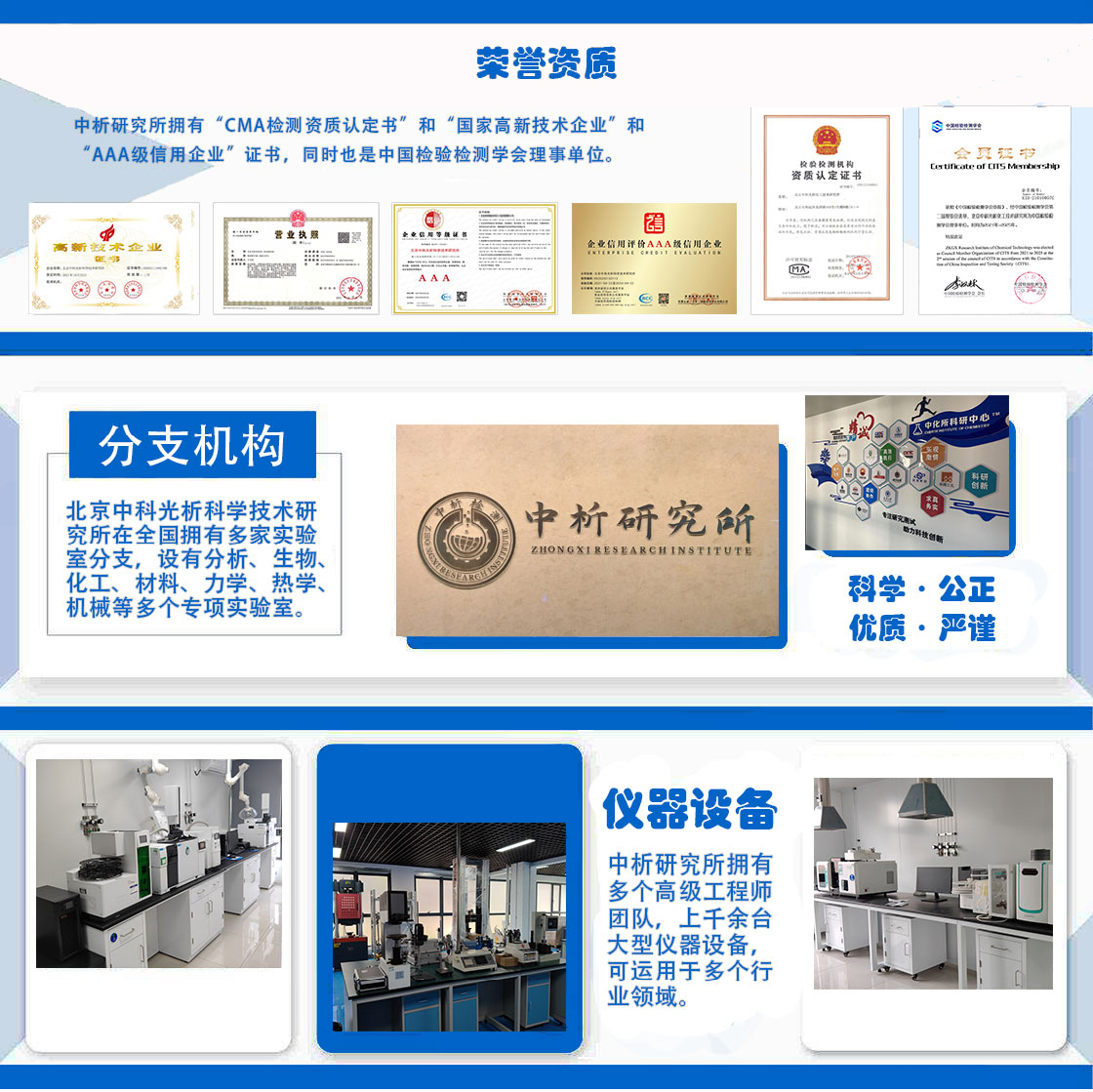
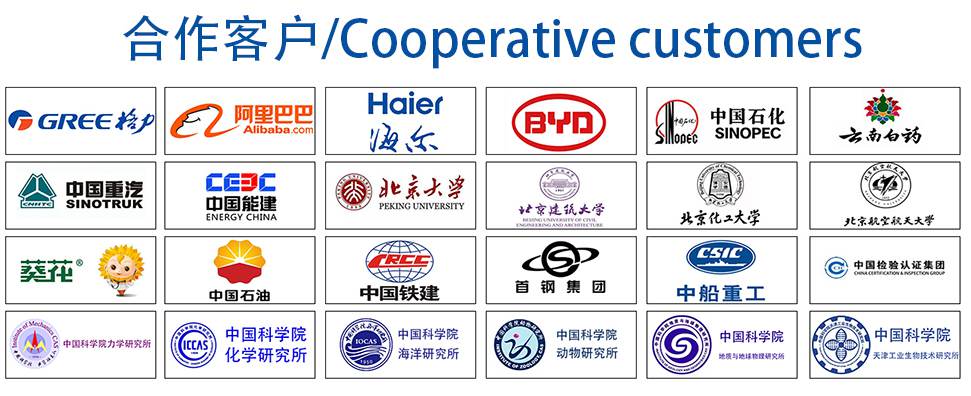