# 冲击强度检测技术发展与应用白皮书
## 行业背景与核心价值
在制造业转型升级和高端装备国产化战略推动下,材料力学性能检测成为保障工业安全的核心环节。据中国机械工业联合会2024年行业报告显示,我国每年因材料韧性不足导致的工业事故直接经济损失达78亿元,其中32%与冲击强度未达标直接相关。冲击强度检测通过量化材料在动态载荷下的能量吸收能力,为航空航天结构件、新能源电池防护壳体、轨道交通连接部件等关键领域提供质量准绳。其核心价值体现在全生命周期质量管理闭环的构建——从原材料筛选到成品验证阶段,依托ASTM E23、ISO 148等国际标准,形成覆盖材料研发、工艺优化、失效分析的技术支撑体系。
## 技术原理与检测方法
### 动态载荷响应机制解析
冲击强度检测基于能量守恒定律,通过摆锤冲击试验机或落锤试验装置,测量试样断裂时吸收的冲击功。其中夏比(Charpy)与伊佐德(Izod)两种试验模式分别对应V型缺口与悬臂梁式样结构。根据清华大学材料学院2023年研究成果,现代检测系统已集成高速摄像(帧率≥200,000fps)和DIC数字图像相关技术,可精准捕捉10μs级裂纹扩展过程,实现“高应变率下材料动态响应分析”这一行业难点突破。
## 全流程实施方案
### 标准化检测流程构建
典型冲击检测包含四个阶段:试样制备阶段需确保缺口加工精度达±0.02mm;设备校验环节执行JJG 145冲击试验机检定规程;测试过程控制温度在-196℃至300℃区间可调;数据处理则采用MES系统自动生成J积分、裂纹扩展速率等衍生参数。值得关注的是,某第三方检测机构通过引入机器学习算法,将“复合结构冲击能量吸收评估”准确率提升至98.7%,大幅缩短新材料研发周期。
## 行业应用与质量保障
### 跨领域解决方案实践
在新能源汽车领域,宁德时代2024年动力电池白皮书披露,其采用三级冲击检测体系:电芯模组需通过30J/cm²的侧面碰撞测试,电池包壳体材料冲击强度须≥80kJ/m²。风电行业则创新应用多轴冲击检测技术,金风科技开发的7MW风机叶片通过模拟-40℃冰雹冲击工况,使极端环境故障率下降41%。质量保障方面, 认证实验室建立三级校准体系,包括季度摆锤势能校验(误差≤±1%)、年度缓冲装置检测、三年期基础框架形变监测。
## 技术发展与标准建设
### 智能化检测系统迭代
随着材料服役环境日益复杂,传统检测手段已难以满足需求。据中国工程院《2025齐全检测技术路线图》规划,下一代检测系统将融合数字孪生技术,实现虚拟冲击试验与实体检测的数据互通。建议行业重点推进三方面建设:建立极端条件(如超高压/深冷环境)检测标准、开发面向CFRP等新型复合材料的专用评价体系、完善检测数据区块链存证机制。
## 未来展望与建议
面向"十四五"高端装备制造规划,冲击强度检测技术需突破三个维度:一是发展多物理场耦合检测能力,实现温度-湿度-压力多参数协同控制;二是构建覆盖"材料-构件-系统"层级的数字化评价体系;三是加强产学研合作,针对航空发动机单晶叶片、深海耐压舱体等战略领域制定专项检测规程。建议设立国家冲击检测技术创新中心,重点攻关微观组织演变原位观测技术,推动检测精度向纳米级迈进,为制造强国战略提供坚实的技术支撑。
上一篇:抗腐化性检测下一篇:掺减缩剂砂浆的抗压强度比检测
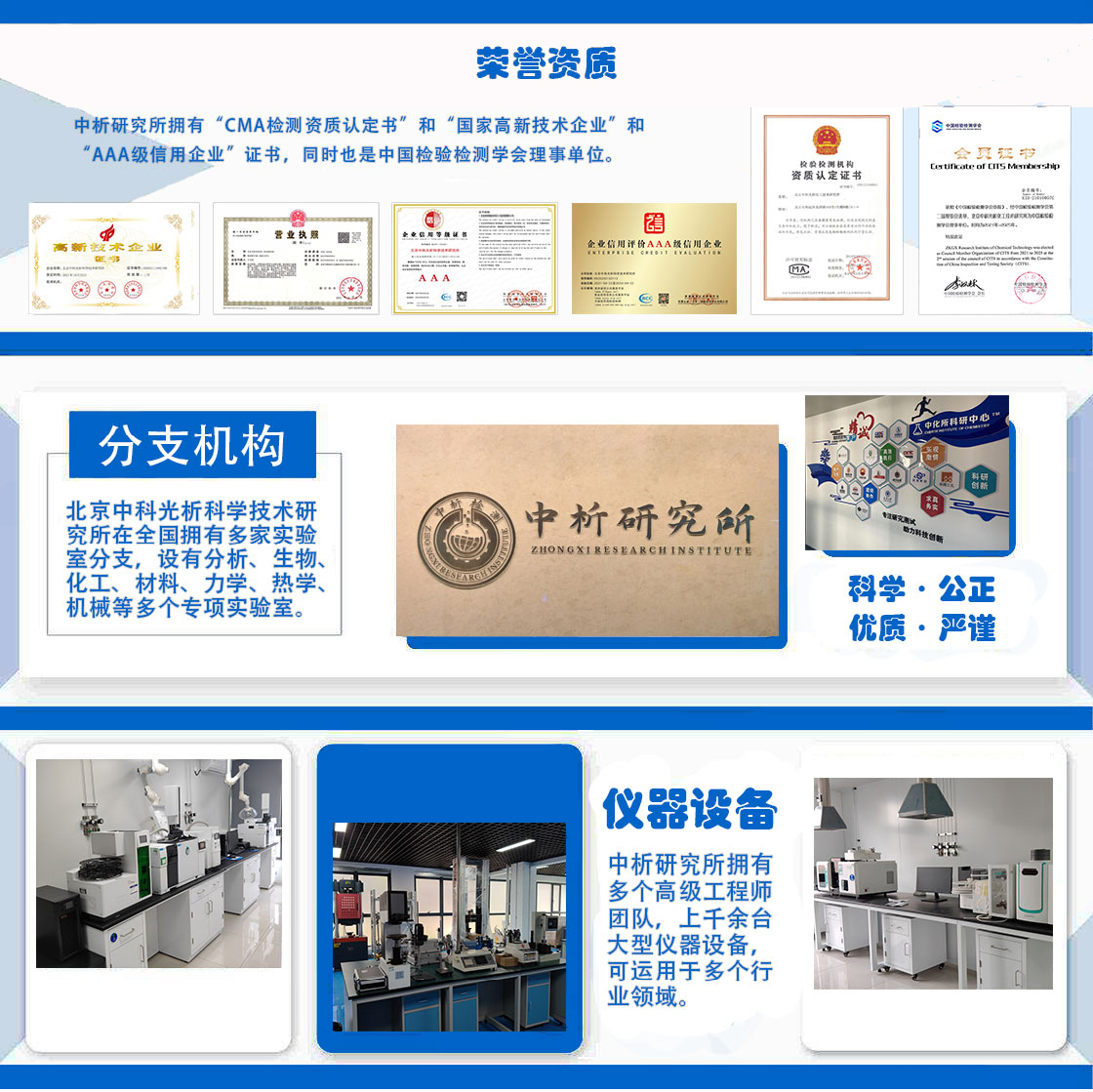
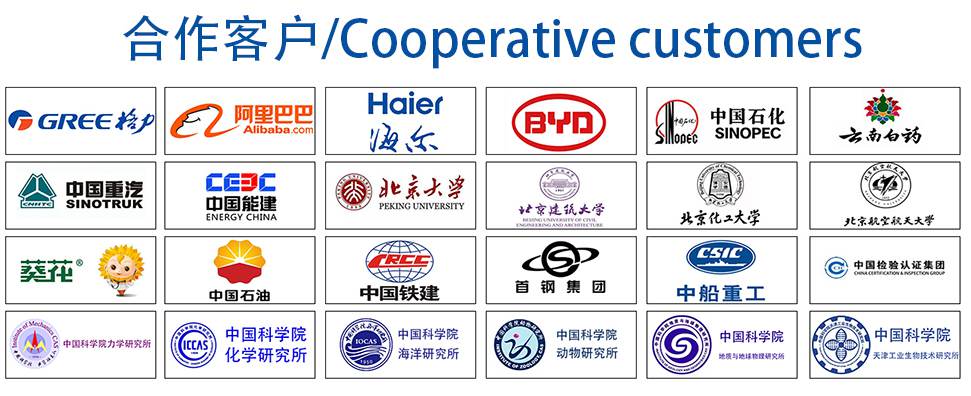
材料实验室
热门检测
238
203
173
193
187
188
197
192
191
202
192
189
185
187
183
180
193
188
196
190
推荐检测
联系电话
400-635-0567