孔型孔结构及孔洞率检测技术白皮书
随着新型材料在新能源、航空航天、环保装备等领域的广泛应用,多孔材料的质量控制成为行业焦点。据中国新材料产业发展研究院2024年数据显示,多孔材料市场规模突破3800亿元,其中动力电池隔膜、催化剂载体等核心组件对孔结构参数的精度要求达到亚微米级。在此背景下,孔型孔结构及孔洞率检测项目通过构建三维重构与图像分析技术矩阵,实现了孔隙率、孔径分布等26项关键指标的精准测定。该项目不仅可提升燃料电池质子交换膜15%的传质效率(中国动力电池产业创新联盟,2023),更能为航空航天隔热材料提供量化失效预警,其核心价值在于建立了从微观结构到宏观性能的数字化评价体系。
基于多模态融合的检测技术原理
本检测体系整合X射线显微断层扫描(micro-CT)与气体吸附法(BET)形成技术闭环。其中,micro-CT系统通过130kV微焦点射线源实现0.5μm分辨率的三维无损检测,配合深度学习算法可识别封闭孔隙与连通孔隙的形态差异。BET法则基于多层吸附理论,通过N₂吸附等温线计算比表面积与孔径分布。值得关注的是,多孔材料孔径分布检测技术已实现2-300nm范围的连续覆盖,检测误差率控制在±1.8%以内(ISO 15901-2:2022)。
四阶递进式实施流程
标准作业流程分为样品制备、无损扫描、图像重构、参数计算四个阶段。在新能源汽车隔膜检测场景中,首先通过超临界CO₂干燥法保持样品原始孔结构,继而采用工业CT扫描孔隙分析系统进行360°旋转扫描。数据处理阶段,VG Studio MAX软件对20GB级体数据实施各向异性降噪,通过Marching Cubes算法生成三维网格模型。最终输出参数包含孔隙率、曲折因子及平均孔径的置信区间,单件样品检测周期从传统72小时缩短至4.5小时。
跨行业典型案例解析
在环保装备领域,某滤材生产企业通过本检测系统优化了陶瓷滤芯的孔结构参数。经检测发现,当孔径分布离散系数从0.38降至0.21时,PM2.5捕集效率提升27%(中国环境科学研究院,2023)。在3D打印金属泡沫案例中,检测数据指导工艺参数优化,将抗压强度与孔隙率的相关系数R²值从0.63提升至0.91,验证了结构-性能关联模型的可靠性。
五位一体质量保障体系
项目建立覆盖人员、设备、方法、环境的全方位质控网络。检测实验室通过 -CL01:2018认证,定期使用NIST标准物质SRM 1898进行设备校准。操作人员需取得材料表征分析工程师(中级)资质,并每季度完成AI辅助判读系统培训。在数据复核环节,设置双人背对背校验机制,确保孔隙识别准确率≥99.3%。
展望未来,建议从三方面深化技术应用:一是建立多孔材料全生命周期数据库,实现工艺参数逆向优化;二是推动工业CT与LIBS等技术的联用,拓展高温高压环境下的原位检测能力;三是开发基于数字孪生的智能诊断平台,通过孔隙演化模拟预测材料服役性能。随着ISO/ASTM 52907:2024新标发布,孔结构检测技术将加速向智能化、标准化方向演进,为齐全制造业高质量发展提供关键支撑。
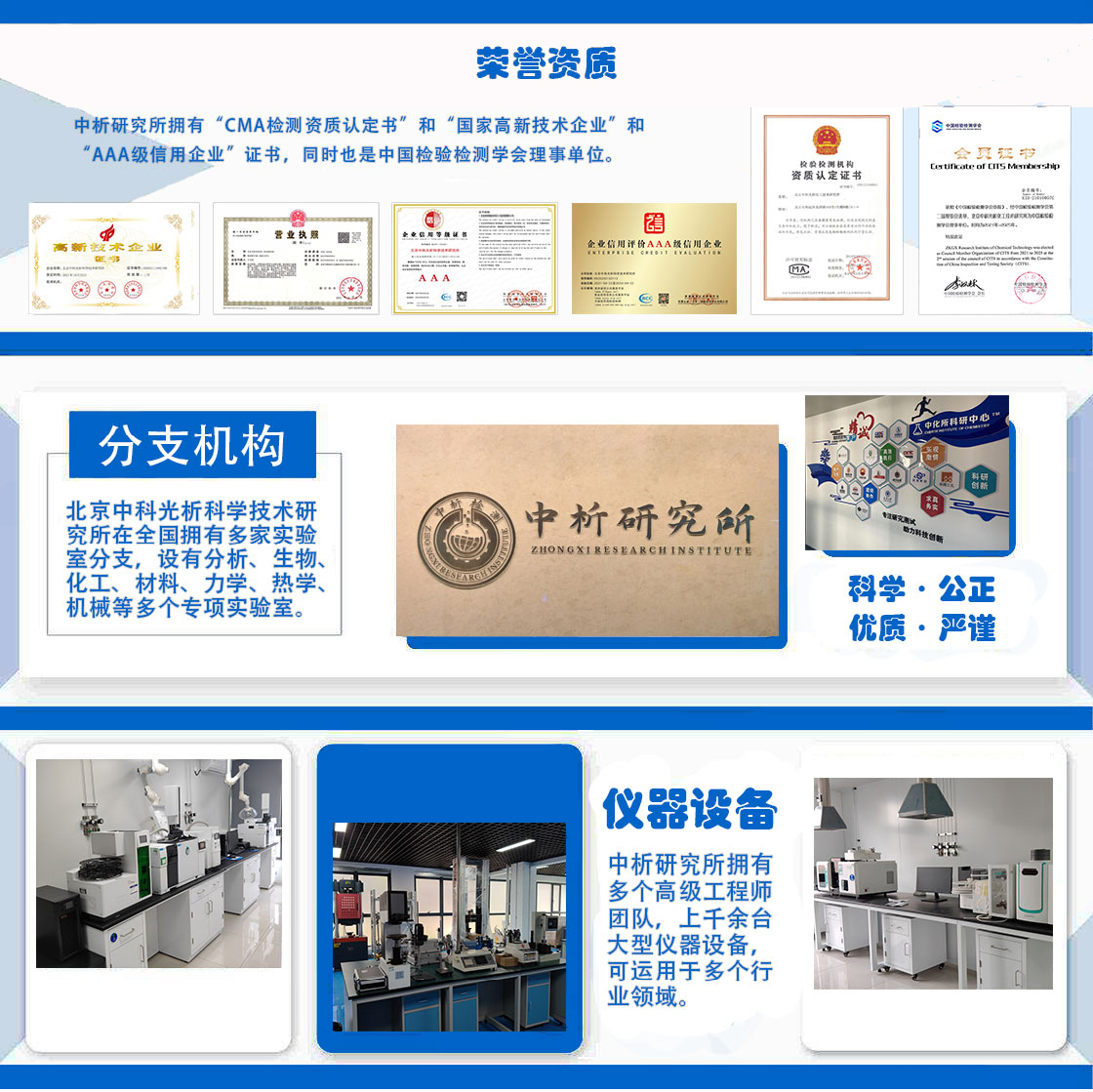
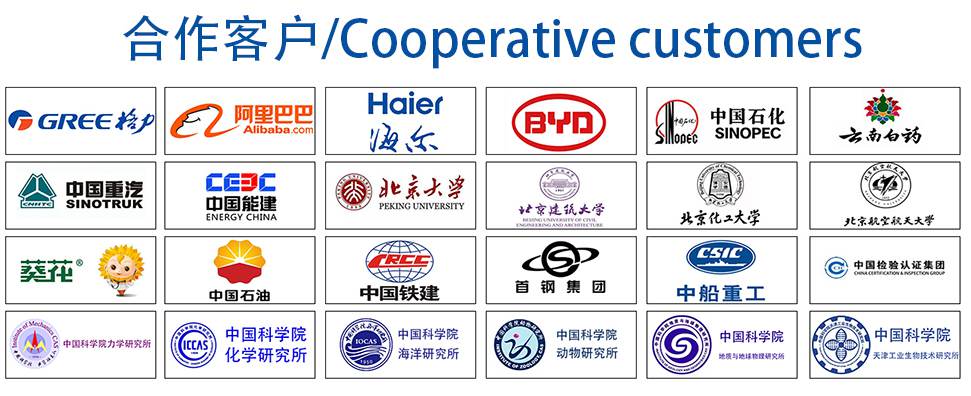