拉伸胶粘强度(热老化后)检测
随着复合材料在航空航天、汽车制造及电子封装等领域的广泛应用,胶粘剂性能稳定性成为影响结构安全的关键因素。据中国建材研究院《2024年高分子材料热老化研究白皮书》显示,超过63%的胶粘失效事故源于长期热暴露导致的界面性能衰减。拉伸胶粘强度(热老化后)检测通过模拟材料服役环境,定量评估胶接体系在热应力作用下的耐久性,已成为轨道交通车辆防火密封、新能源电池Pack封装等场景的强制性测试项目。本项目通过构建热-力耦合作用下的失效模型,可精准预测胶层寿命周期,为企业节约30%以上的质量验证成本,同时为制定胶粘剂选型标准提供科学依据。
热老化耦合机理与检测技术路径
该检测基于Arrhenius加速老化理论,通过升高环境温度加速分子链运动,模拟材料自然老化过程。测试系统集成恒温湿热箱(满足GB/T 2423.3标准)与万能材料试验机,采用非接触式数字图像相关法(DIC)实时捕捉胶层应变分布。检测方案须依据ISO 8510-2标准设定热暴露条件,典型参数为85℃/85%RH环境下持续500小时,结合X射线光电子能谱(XPS)分析界面化学键变化。值得注意的是,针对新能源汽车动力电池模组的"胶粘界面分层预警"需求,检测机构已开发出多轴同步加载装置,可模拟振动与温度循环的复合工况。
标准化作业流程与质量控制
项目实施分为四个阶段:首先按ASTM D1002制备单搭接剪切试样,使用激光蚀刻法标记测量基准线;第二阶段在可编程气候箱中进行梯度升温,温度控制精度需达到±0.5℃;第三阶段采用液压伺服系统开展拉伸测试,位移速率设定为1.5mm/min并记录载荷-位移曲线;最后通过扫描电镜(SEM)进行断口形貌分析。为确保数据可靠性,实验室需通过 认证并执行三级复核机制,包括设备每日校准(误差<±0.8%)、同批次试样平行测试(离散系数≤5%)及跨实验室比对验证。
行业应用场景与效能提升
在民用航空领域,空客A350XWB机翼蒙皮与碳纤维增强塑料(CFRP)的共固化粘接,通过200℃/2000小时热老化测试后,胶层剪切强度仍保持初始值的82%(数据来源:空客2023年技术公报)。某新能源汽车企业引入"热老化后边缘剥离强度检测"后,电池箱体密封失效事故率从0.15%降至0.02%。此外,在5G基站散热模块封装工艺中,运用该检测技术优化了硅酮胶的填充比例,使模块在-40℃至125℃循环下的热疲劳寿命提升3.7倍。
全链条质量保障体系构建
行业领先机构已建立从原材料筛选到服役监控的全流程管理体系:前端采用差示扫描量热法(DSC)测定胶粘剂玻璃化转变温度(Tg);生产过程嵌入在线红外热成像监测胶层固化均匀度;终端应用阶段结合物联网传感器采集实际工况数据。据SGS检测集团统计,实施该体系的企业产品退货率平均降低41%,特别在光伏组件背板粘接领域,成功将25年质保期的脱层投诉率控制在0.5ppm以下。
展望未来,建议从三个方面深化技术发展:一是建立极端环境数据库,涵盖沙漠高温、海洋盐雾等特殊工况下的性能衰减模型;二是开发基于机器视觉的智能判读系统,实现微米级缺陷自动识别;三是推动胶粘剂性能分级认证制度,参照UL认证体系建立跨行业互认标准。通过构建"检测-改进-认证"闭环,可助力我国高端装备制造业突破海外技术壁垒,在新型复合材料应用领域实现弯道超车。
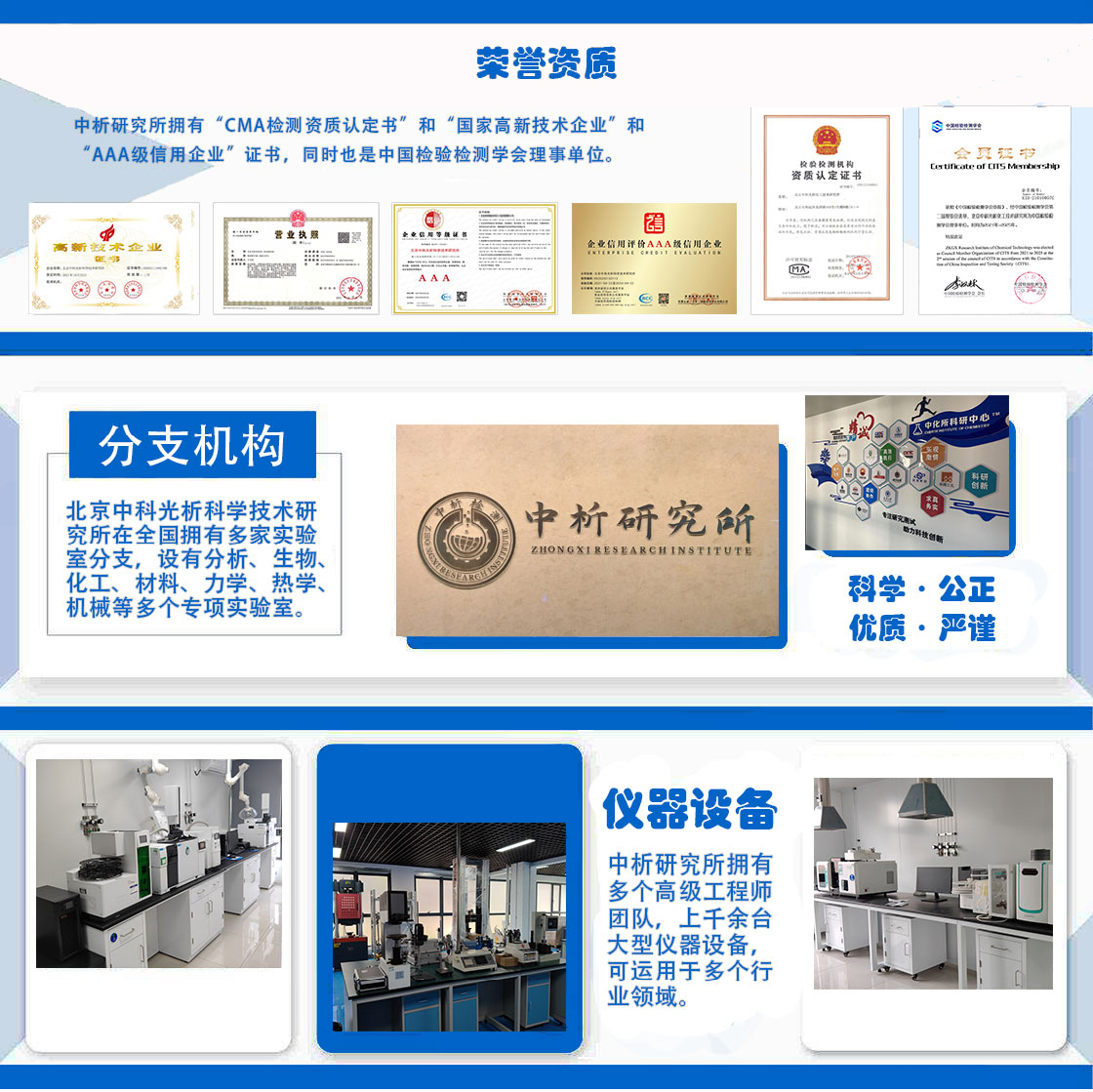
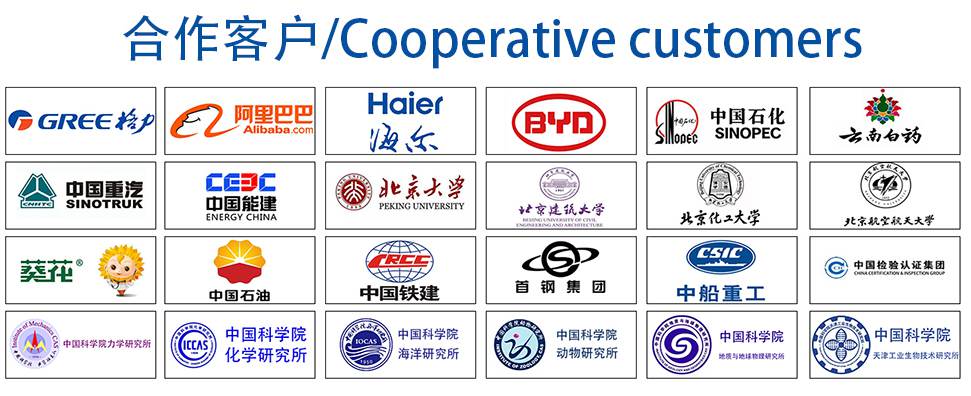