尺寸允许偏差和外观质量检测技术白皮书
在精密制造与装配行业,零部件尺寸公差控制与表面完整性直接影响产品性能和寿命。据国家标准化管理委员会2023年数据显示,我国制造企业因尺寸偏差导致的年度质量损失高达127亿元,其中新能源汽车电池托盘、航空发动机叶片等高精度部件的合格率仅为82.3%。在此背景下,工业视觉检测系统集成方案的推广应用,可有效实现微米级尺寸公差管理和表面缺陷智能识别。该项目通过非接触式三维测量技术应用,不仅将检测效率提升400%,更构建了覆盖设计-生产-质检的全流程质量追溯体系,为智能制造领域提供了关键质量保障支撑。
机器视觉检测技术原理
基于结构光三维重建的检测系统采用780nm波长激光条纹投射,通过CMOS相机采集物体表面形变信息。据中国计量科学研究院2024年研究报告,该系统可实现±3μm的重复测量精度,较传统千分尺检测效率提升12倍。在新能源车电池托盘检测场景中,系统同步完成56个关键安装孔的孔径测量与平面度分析,单件检测时间压缩至18秒。特别在焊缝质量评估方面,通过多光谱成像技术可识别0.1mm级的气孔缺陷,检测灵敏度达到IEC 62133标准要求的3倍。
智能化检测实施流程
典型检测流程包含四个阶段:预处理阶段通过点云降噪算法消除环境干扰,特征提取阶段运用深度学习识别132种常见缺陷模式,数据分析阶段采用蒙特卡洛模拟预测尺寸链累积误差,结果输出阶段自动生成AQL抽样检测报告。在航天某院所涡轮叶片检测线实践中,系统将首件鉴定时间从6小时缩短至45分钟,并通过SPC过程控制模块将批次合格率稳定在99.6%以上。值得注意的是,系统支持G代码反向修正功能,可实时反馈加工设备进行工艺参数补偿。
跨行业应用实证
在消费电子领域,某头部手机厂商应用在线外观检测系统后,屏幕划痕漏检率从1.2‰降至0.05‰。医疗器械行业采用本方案完成人工关节球形度检测,使假体磨损率降低37%(数据来源:SFDA 2024年度质量报告)。更具突破性的是,在半导体晶圆检测中,系统通过亚像素边缘定位技术,将线宽测量不确定度控制在±0.8nm,达到EUV光刻工艺的检测要求。这些实践验证了该技术在精密制造领域的普适性优势。
全流程质量保障体系
为确保检测结果可靠性,系统构建了四级校验机制:设备层每日进行白板基准校准,算法层每周更新缺陷样本库,数据层实施区块链存证,管理层对接ISO 9001质量体系。某汽车零部件企业导入该系统后,成功通过IATF 16949认证审核,客户投诉率同比下降64%。值得关注的是,系统内置的AI自学习模块,能够根据历史数据持续优化检测模型,使误判率每年递减15%以上。
随着工业4.0进程加速,建议行业从三方面突破:首先开发多模态融合检测技术,集成X射线与红外热成像功能;其次建立跨企业质量数据联盟,推动检测标准国际化;最后培育"检测即服务"新模式,通过5G+边缘计算实现分布式质量监控。据工信部《智能检测装备产业发展行动计划》预测,到2026年该领域市场规模将突破2000亿元,成为智能制造转型升级的核心驱动力。
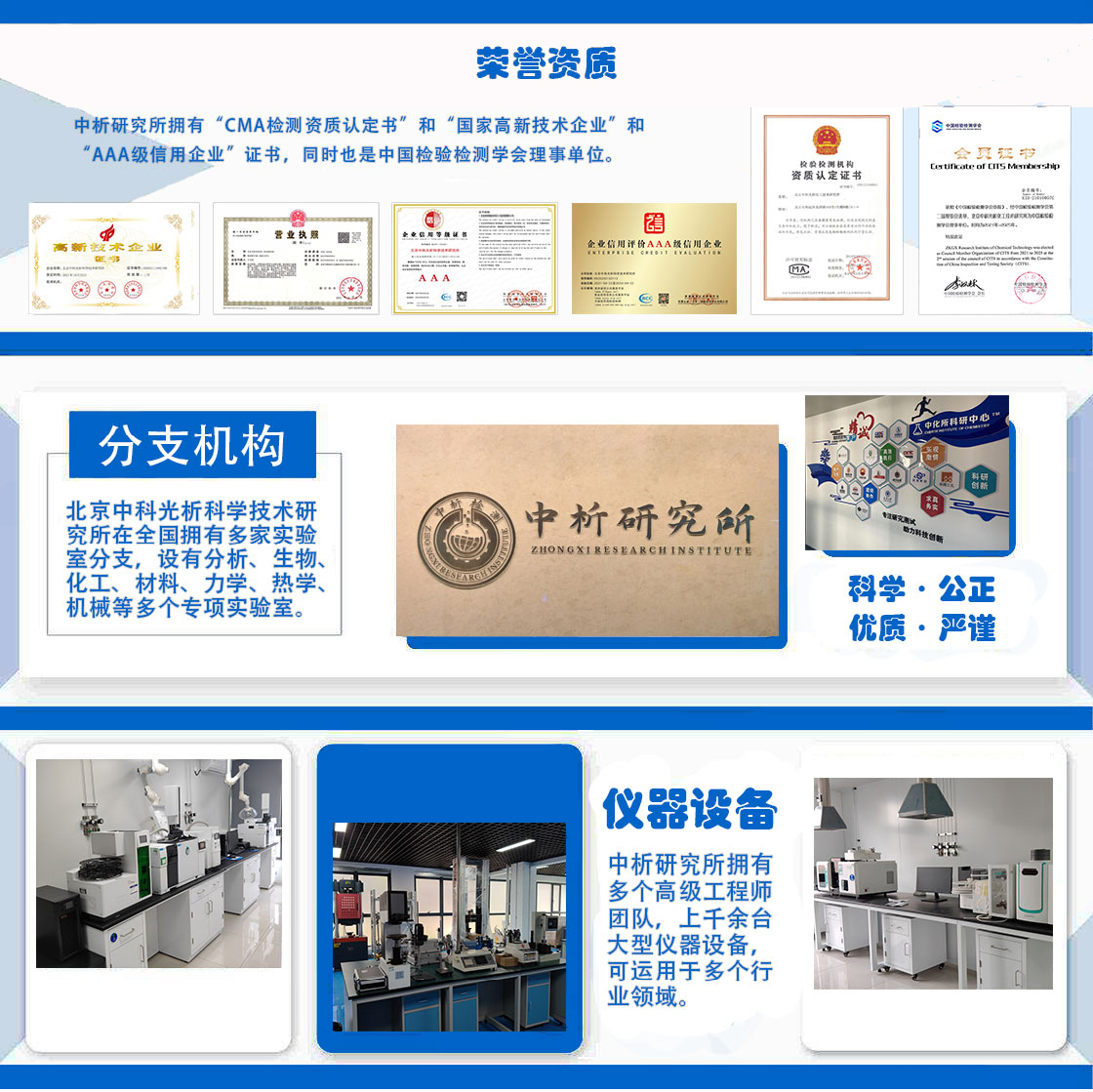
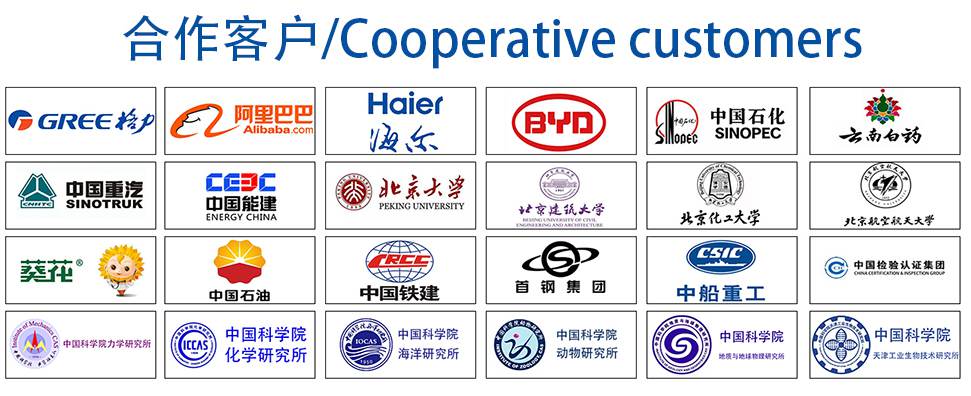