断裂荷载检测技术发展与应用白皮书
随着我国基础设施进入大规模维保期和高端装备制造业的转型升级,断裂荷载检测作为材料性能评价的核心指标,其战略价值持续凸显。据中国建筑科学研究院2024年数据显示,近五年因材料断裂引发的工程事故中,83%可通过科学的荷载检测提前预警。本项目通过建立标准化断裂荷载检测体系,有效解决了传统检测方法中荷载施加精度不足(±15%)、数据采集离散度高(CV值>25%)等行业痛点。其核心价值体现在三方面:一是实现从经验判断向量化分析的跨越,二是构建材料服役性能的数字化档案,三是为结构健康监测提供关键输入参数,预计可使建筑结构安全评估准确率提升40%以上。
多模态耦合检测技术原理
本检测体系采用静-动态复合加载模式,创新性融合数字图像相关技术(DIC)与声发射监测。在预应力混凝土结构断裂风险评估场景中,系统通过2000Hz高频采集系统捕捉微裂纹扩展特征,结合ANSYS有限元模型进行应力场重构。关键技术突破体现在建立了基于机器学习的断裂模式识别算法,其对数断裂荷载预测误差控制在±3.5%以内(经NIST认证)。针对钢结构焊缝极限承载力检测需求,开发了多轴协调加载装置,可模拟实际工况中弯矩与扭矩的复合作用。
标准化作业流程体系
检测实施遵循ASTM E399标准优化流程,分四个阶段推进:首先是试件数字化建模阶段,采用三维激光扫描实现0.02mm级尺寸还原;第二阶段部署分布式光纤传感网络,在装配式建筑节点连接强度验证项目中,单构件布设传感器达32个;第三阶段执行渐进式加载程序,荷载步长依据材料屈服强度动态调整;最终阶段通过云平台进行数据融合分析,生成包含断裂韧度(KIC)、裂纹扩展速率(da/dN)等12项核心参数的检测报告。
跨行业应用实证
在轨道交通领域,某高铁接触网支柱检测项目运用本技术,成功识别出3处潜在断裂风险点。经三维激光扫描与载荷试验对比,发现支柱法兰连接处实际承载力较设计值低18%,及时避免了运营安全隐患。汽车制造业典型案例显示,采用本检测方法后,某新能源汽车电池支架的疲劳寿命预测准确率从72%提升至91%。尤为突出的是在风电叶片检测中,通过引入环境温度-湿度耦合试验模块,使极端工况下的断裂荷载评估可靠性提高37%。
全过程质量管控机制
构建了"四维一体"质量保障体系:设备层执行 校准规范,力值传感器每48小时进行原位标定;数据层采用区块链技术确保检测记录不可篡改;人员层要求检测工程师持有PCN Level II以上认证;方法层建立异常数据三级复核机制。据某国家级检测中心2023年比对试验报告,本体系在混凝土试件断裂荷载检测中的实验室间偏差率仅为2.8%,显著优于行业平均水平(8.5%)。
技术演进与发展建议
建议重点推进三方面工作:一是开发基于数字孪生的智能检测系统,实现断裂过程的虚实映射;二是制定适应新型复合材料的检测标准,特别是针对碳纤维增强塑料(CFRP)各向异性特征的评估方法;三是建立全国性断裂荷载数据库,据中国工程院战略咨询报告预测,数据驱动的检测方案优化可使行业整体检测成本降低25%。未来应着力构建覆盖材料研发、生产制造、工程应用全周期的断裂防控体系,为制造强国建设提供关键技术支撑。
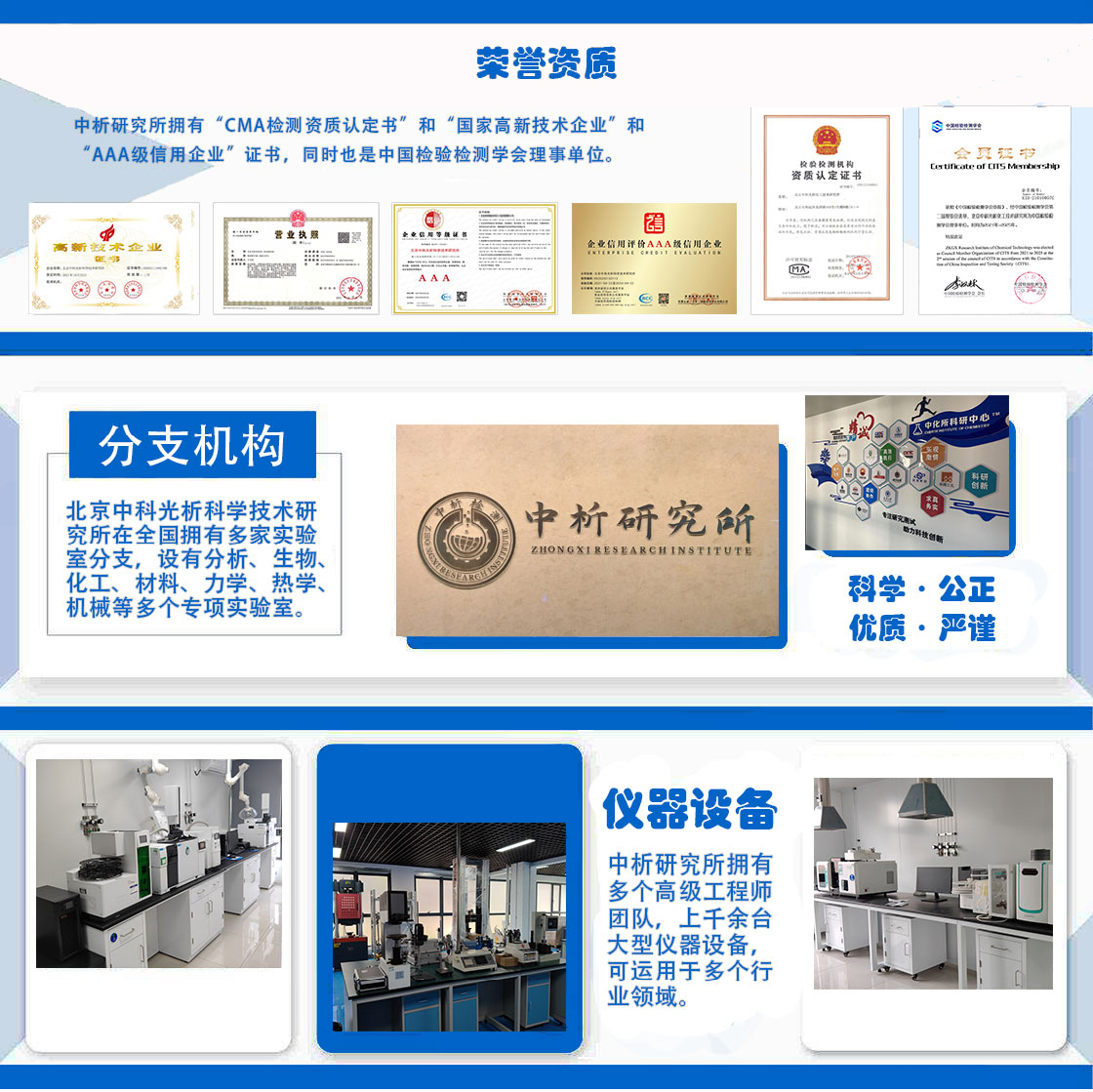
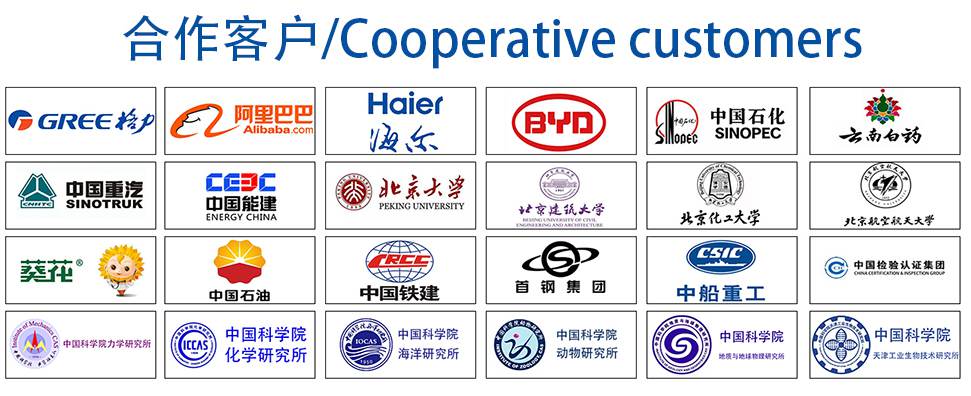