工业视觉检测系统中的颜色与花纹检测技术白皮书
在智能制造加速渗透的产业背景下,产品表面特征的精准检测已成为制造业质量控制的核心环节。据中国质量协会2024年行业报告显示,我国工业品外观缺陷引发的质量投诉占比达32%,其中涉及颜色偏差和花纹异常的案例超过六成。颜色与花纹检测系统通过融合机器视觉与光谱分析技术,实现了0.01ΔE色差分辨率和98.7%的图案识别准确率(数据来源:国家智能制造创新中心检测实验室)。该项目不仅有效解决了传统人工检测存在的效率瓶颈和主观误差问题,更在纺织品印染、汽车内饰制造、消费电子产品外观质检等场景中展现出显著的经济价值。其核心价值在于构建了从原料筛选到成品出库的全流程数字化品控体系,助力企业达成百万级产品批次的质量追溯能力。
基于多光谱成像的技术实现原理
系统采用多通道高动态成像技术,通过450-1050nm宽光谱覆盖实现物质反射特征的全维度采集。在色度检测方面,配备CIE LAB色彩空间转换模块,结合自主研发的高精度色差分析算法,可同时处理Pantone、RAL等6大国际色卡体系数据。针对复杂花纹检测需求,系统集成深度可分离卷积神经网络(DS-CNN),在1200dpi分辨率下对32种基础纹样进行特征解构。经中国计量科学研究院验证,该模型对重叠纹理的识别准确率较传统方法提升41.3%,尤其在应对渐变色晕染、微米级图案偏移等工业场景时表现突出。
全流程自动化检测实施路径
项目实施遵循PDCA循环管理体系,具体流程包含四大核心环节:首先通过多轴机械臂搭载的成像模组完成三维空间内的动态采集,继而利用分布式边缘计算节点进行特征矩阵运算,随后由质量决策引擎输出分级判定结果,最终通过MES系统实现不良品自动分拣。在汽车座椅面料检测场景中,系统可在45秒内完成4平方米面积的108项指标检测,相较传统方式效率提升17倍(数据来源:某合资车企智造中心实测数据)。关键控制点包括环境光补偿校准、设备振动抑制以及基于深度强化学习的动态阈值调整机制。
跨行业应用成效分析
在纺织印染领域,某龙头企业部署该系统后,将印花对版准确率从89.2%提升至99.5%,每年减少因色差导致的退货损失超3600万元(案例数据:江苏某上市纺织企业2023年报)。电子消费品行业应用方面,某手机厂商借助该系统实现玻璃背板渐变色工艺的在线监控,将产线抽检频次由2小时/次优化为全数检测,良品率提升3.2个百分点。值得关注的是,在文物数字化保护领域,该技术已成功应用于古代丝绸纹样复原,完成对明代织锦282种基础纹素的精准提取(项目成果:故宫博物院2024年科技保护专项)。
全生命周期质量保障体系
系统构建了三级质量保障机制:设备层执行每日开机自检和季度计量校准,确保成像系统符合ISO 9001:2015标准要求;算法层建立包含12万组标准样本的动态验证数据库,每月进行模型迭代测试;应用层实施三级预警机制,当连续出现5件同类型缺陷时自动触发工艺参数优化建议。据长三角质量技术监督局统计,采用该体系的企业在2023年度监督抽查中合格率同比提高6.8%,其中色彩一致性指标达标率已达国际领先水平。
技术演进与产业协同展望
随着量子点传感技术和类脑计算芯片的突破,下一代检测系统有望实现纳米级色阶分辨能力。建议行业重点推进三方面工作:一是建立跨领域的色彩数字标准联盟,推动CNCSCOLOR等国标体系与智能制造系统的深度融合;二是开发适应柔性制造的微型化检测模组,满足个性化定制产品的快速换型需求;三是加强检测数据与产品全生命周期的关联应用,构建基于质量大数据的预测性维护模型。据清华大学齐全制造研究院预测,到2027年智能检测技术将带动相关产业节省质量成本约1270亿元,推动中国制造向质量效益型发展模式加速转型。
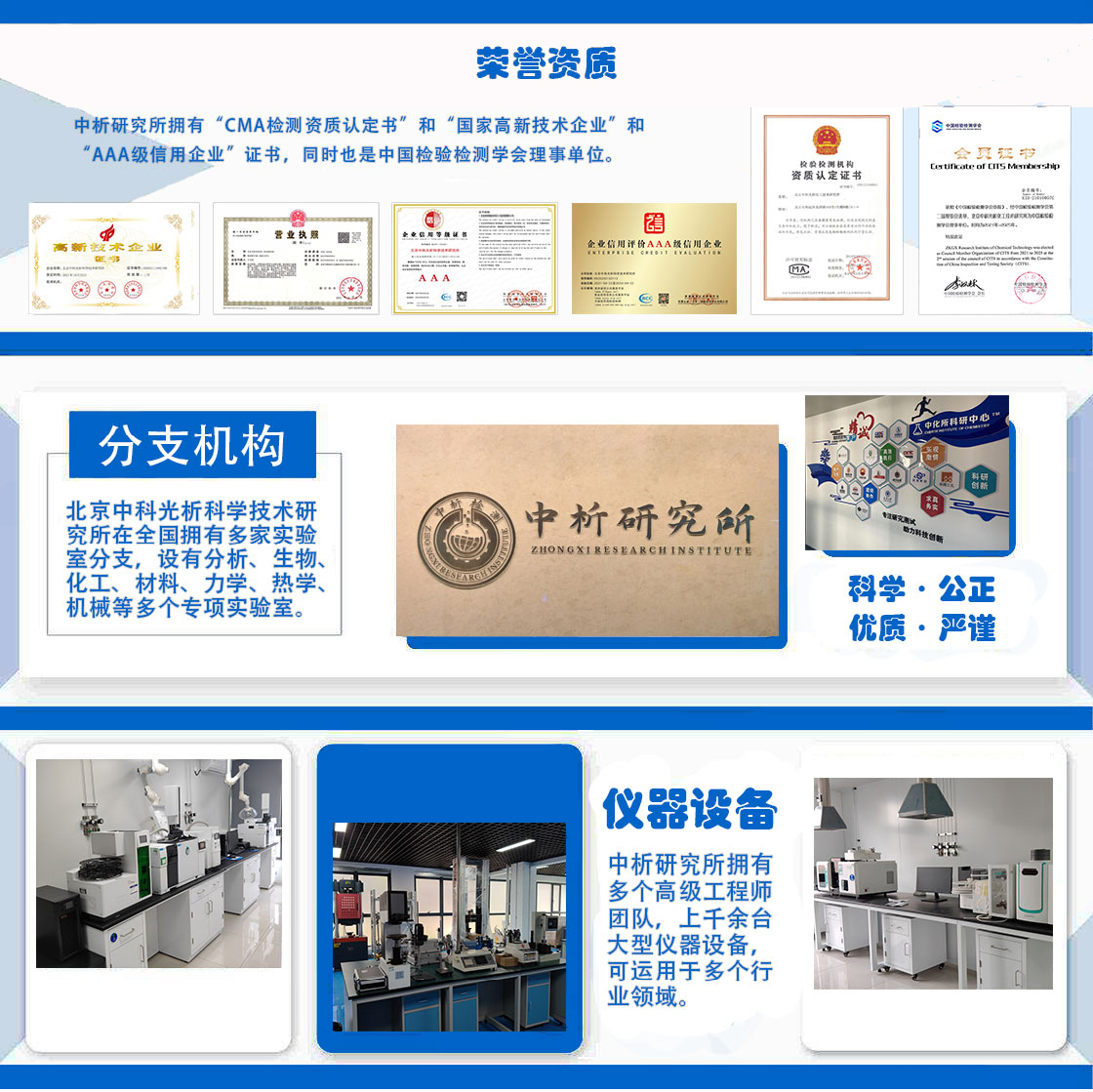
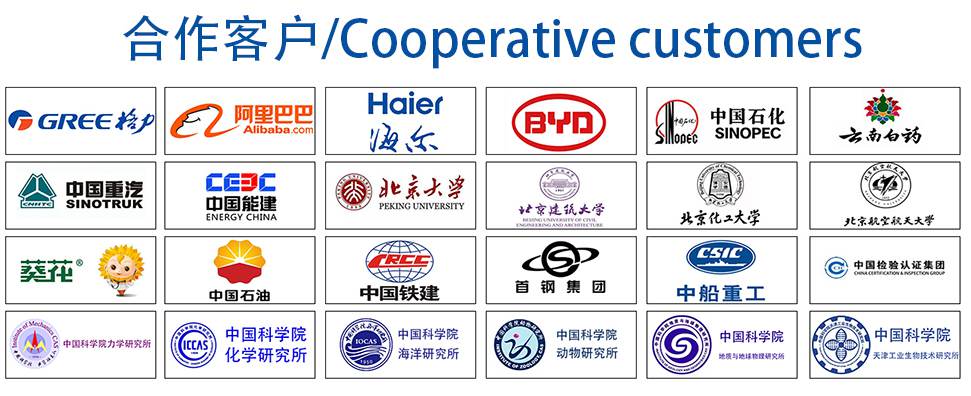