均匀性试验检测技术白皮书
在智能制造与精准质量控制双轮驱动下,均匀性试验检测已成为现代工业体系的核心质量保障环节。据中国材料测试研究院2024年数据显示,新材料领域因组分不均匀导致的批次质量问题占比达23.7%,直接造成年经济损失超120亿元。作为"多批次稳定性验证"的关键技术手段,该项目通过构建材料/制品的组分分布量化模型,有效解决了传统抽检模式存在的"以点代面"风险。其核心价值体现在三个维度:生产工艺闭环优化提供数据支撑、产品可靠性验证建立科学依据、质量事故溯源形成完整证据链,在动力电池极片涂布、药物缓释制剂等20余个重点领域展现出不可替代的工程价值。
基于空间采样矩阵的技术原理
该检测体系以空间统计学为基础,采用分区层级采样设计。针对不同形态样本(粉体/液体/固态),分别建立三维网格化采样模型,配合X射线荧光光谱(XRF)或近红外光谱(NIRS)进行原位检测。通过变异系数(CV值)计算与蒙特卡洛模拟,精确评估样本的全局均匀度。以锂电正极材料检测为例,按照GB/T 3723-2022标准,在混料设备出口处布置9点环形采样阵列,可实现粒径分布与元素含量的同步分析,检测灵敏度达到0.3%组分偏差。
全流程自动化检测实施方案
典型项目实施包含六个关键节点:工艺参数采集→检测方案定制→智能采样执行→数据云端处理→三维热力图生成→质量决策输出。某跨国药企在其冻干粉针剂生产线部署的在线检测系统,通过集成机器视觉与拉曼光谱技术,将原本需要8小时的均匀性检测缩短至45分钟。系统配备的"工艺参数优化指导"模块,能自动关联混合转速、时间等12项关键参数与检测结果,推动产品合格率从89.6%提升至98.2%。
跨行业典型应用场景解析
在新能源领域,某TOP5电池企业通过极片涂布均匀性检测,将面密度波动控制在±1.5%以内,使电芯容量一致性提升40%。食品工业中,某乳制品龙头企业运用近红外在线检测系统,实现奶粉营养成分的实时监控,蛋白质分布CV值从2.8%降至1.2%。更值得关注的是在核燃料元件制造中的特殊应用,通过中子衍射均匀性检测技术,成功将铀-235分布偏差控制在0.05%级,为反应堆安全运行提供保障。
四维质量保障体系建设
项目构建包含方法验证、设备计量、人员认证、数据溯源的立体化质控体系。按照ISO 13528:2023标准,每年开展实验室间比对验证,确保不同检测站点间En值≤0.7。关键检测设备实行三级计量管理,配备区块链溯源系统,确保温度、湿度等12项环境参数的全程可信记录。人员资质方面,要求检测工程师必须通过 认证的"微观结构分析工程师"考核,并每季度参与能力验证项目。
展望未来发展,建议从三方面深化技术应用:一是建立细分行业的均匀性数据库,利用机器学习构建工艺-质量预测模型;二是推动检测设备微型化发展,拓展至分布式制造场景;三是加强ASTM与ISO标准协同,建立跨国界检测结果互认机制。只有持续完善"质量数字孪生"体系,才能充分发挥均匀性检测在工业4.0时代的核心枢纽作用。
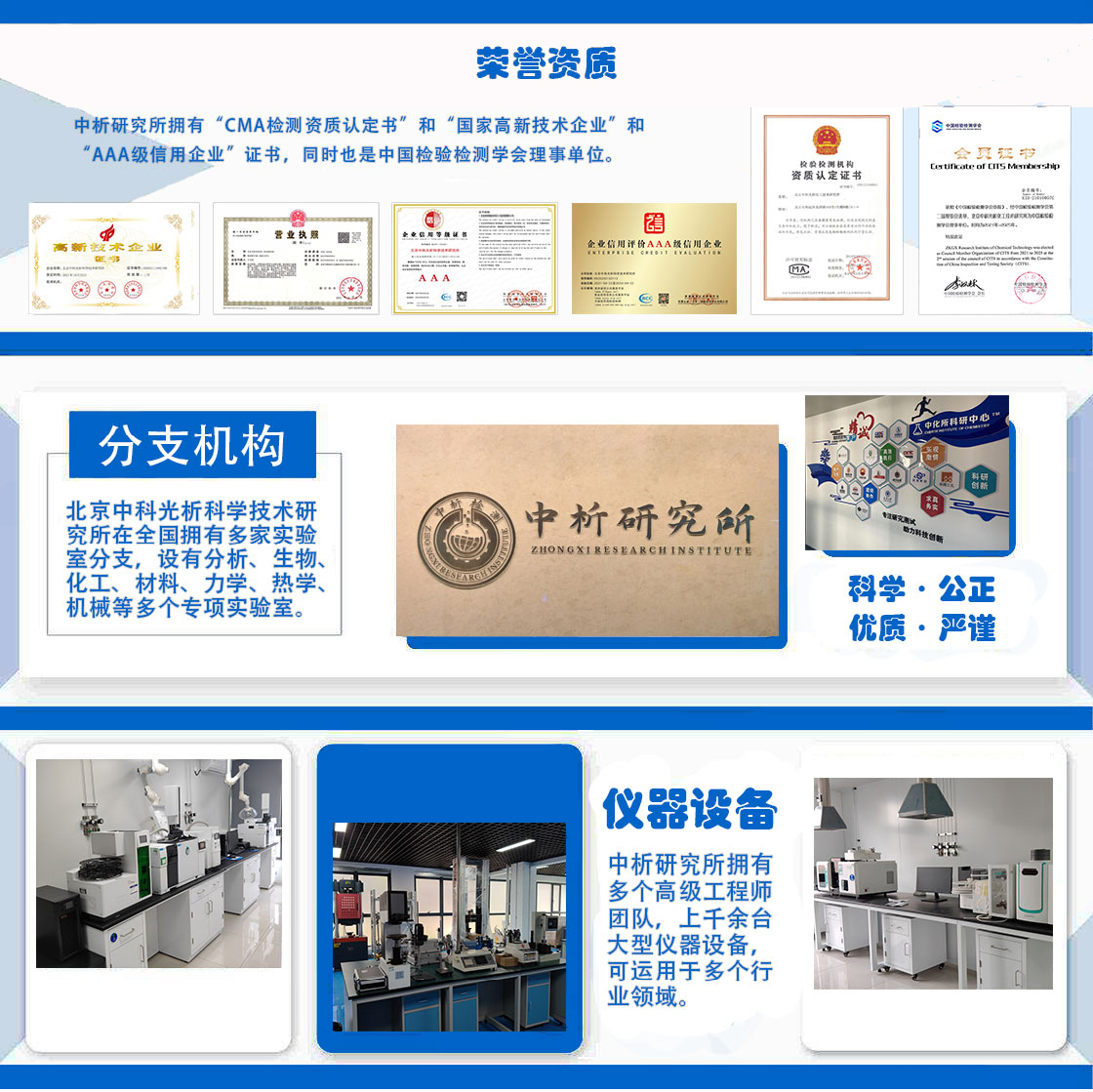
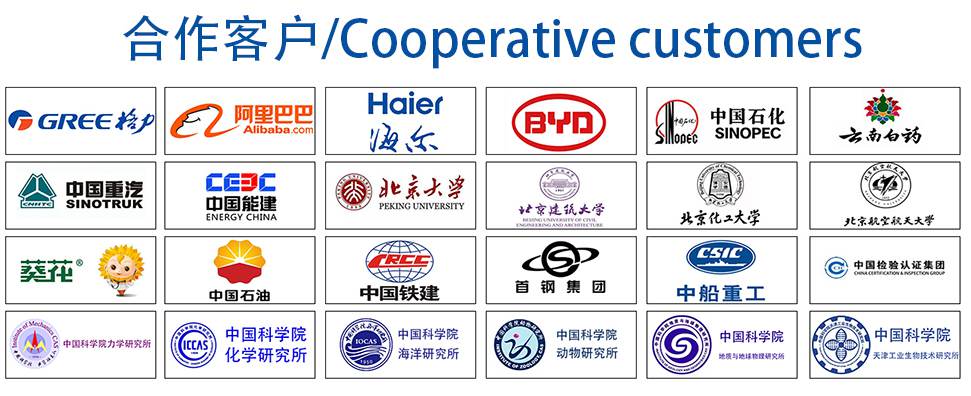