圆锥破碎机检测:保障设备高效运行的关键措施
圆锥破碎机作为矿山、建材、冶金等行业的核心破碎设备,其运行稳定性直接影响生产效率和经济效益。定期开展系统性检测不仅能预防突发性故障,更能通过数据监控优化设备性能,延长使用寿命。检测过程需结合设备运行参数、磨损规律及行业标准,涵盖机械结构、液压系统、润滑装置、电气控制等全方位评估。规范的检测流程可降低30%以上的意外停机风险,并为维修决策提供科学依据。
核心检测项目及实施要点
1. 机械部件完整性检测
重点检查动锥、定锥衬板的磨损量(使用超声波测厚仪),测量偏心套与主轴间隙(标准值通常为0.8-1.2mm),检测锁紧缸压力是否达到设定值(常规范围6-8MPa)。需特别注意液压锁紧系统的密封性,油液泄漏量超过15ml/min时应及时更换密封件。
2. 润滑系统效能检测
采用油液光谱分析技术监测润滑油污染度,铁含量超过150ppm需换油。检测油路通畅性时,应确保供油压力维持在0.15-0.3MPa范围,回油温度不超过55℃。对于稀油站需验证其过滤精度是否达到25μm标准,油泵流量衰减超过15%必须检修。
3. 电气控制系统检测
使用万用表检测电机绝缘电阻(≥5MΩ),PLC模块I/O响应时间偏差不得超过0.2s。过载保护装置需模拟测试跳闸灵敏度,压力传感器误差应控制在±0.5bar以内。特别要检查防尘措施是否有效,电气柜内粉尘沉积量不得影响散热。
4. 振动与噪音分析
采用振动频谱仪检测轴承部位振动值,径向振幅超过0.15mm需停机检查。噪声监测点距设备1米处的声压级应≤85dB(A),异常高频噪音往往反映齿轮啮合问题。建议每月建立振动趋势图谱,当振幅月增长率超过20%时应预警。
5. 液压系统性能验证
检测液压站压力稳定性(波动值≤±5%),测试蓄能器充氮压力是否在额定值80%-90%范围。执行液压缸全程动作试验时,要求油缸伸缩时间差不超过标称值10%。系统内泄检测可通过保压试验,10分钟内压降超过15%判定存在泄漏。
智能化检测技术应用
新型在线监测系统可实现轴承温度、振动值、油液状态等20+参数的实时采集,结合AI算法可提前72小时预测85%的机械故障。建议企业建立设备健康档案,将检测数据与生产负荷、物料硬度等参数关联分析,实现预防性维护的精准决策。
通过建立包含上述检测项目的标准化作业流程,企业可显著提升圆锥破碎机的MTBF(平均故障间隔时间),典型应用案例显示年维护成本可降低28%,设备综合效率(OEE)提高15%以上。建议每季度执行全面检测,关键部件检测周期不超过2000运行小时。
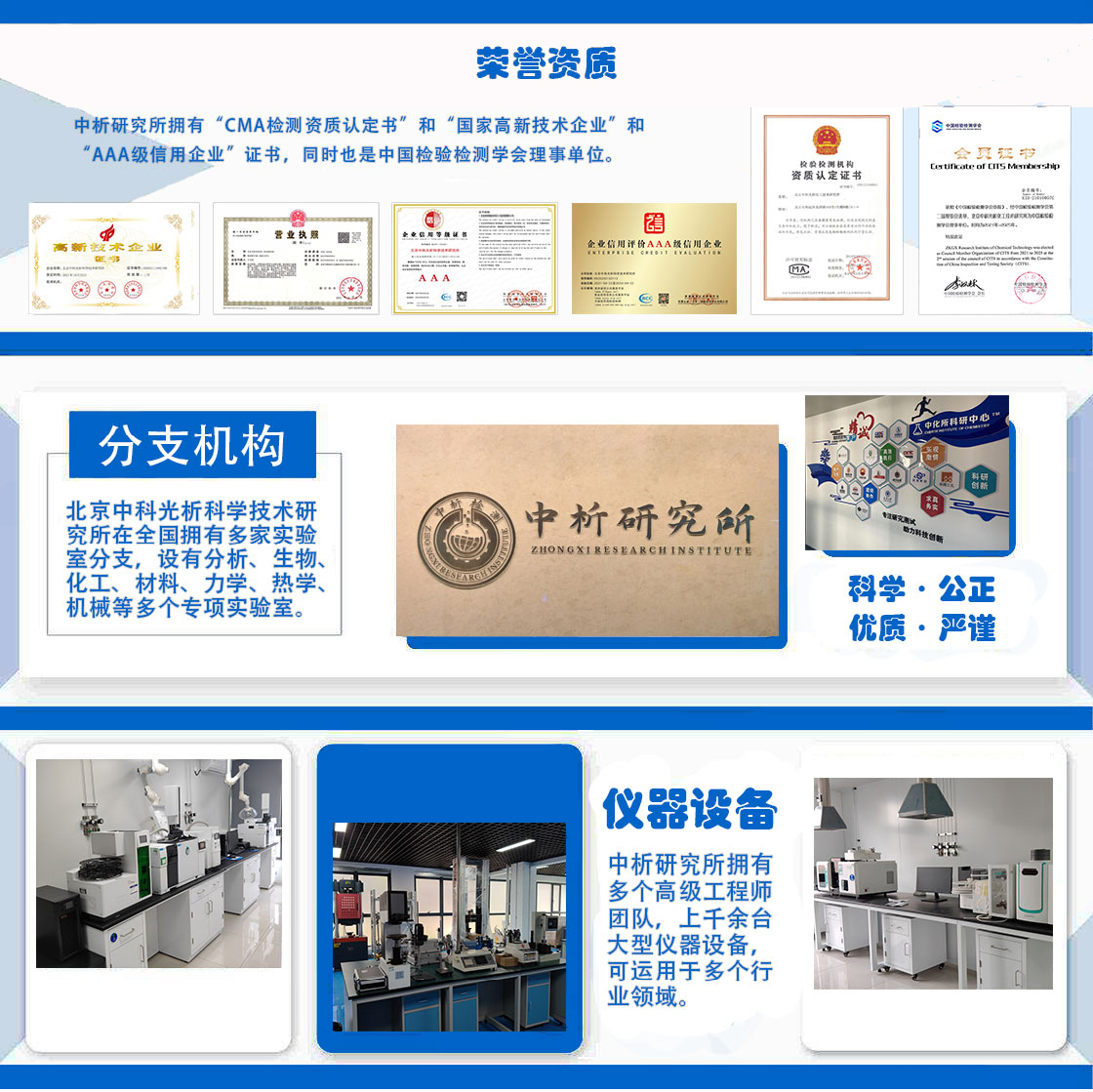
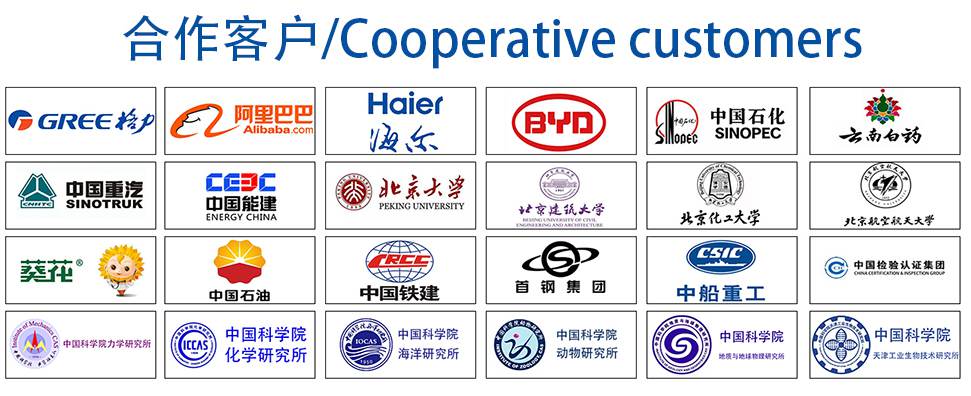