石油管检测的重要性与技术发展
在石油天然气工业中,管道作为能源输送的核心载体,其安全性与可靠性直接关系到生产效率和环境安全。据统计,每年因管道腐蚀、裂纹或焊接缺陷导致的泄漏事故造成的经济损失超过50亿美元。石油管检测技术通过系统性评估管道完整性,成为预防事故、延长使用寿命的关键环节。当前行业采用的检测体系已涵盖材质分析、力学性能测试、无损检测及智能化监控等20余项核心指标,形成了覆盖全生命周期的质量管控网络。
1. 化学成分与冶金性能检测
采用直读光谱仪(OES)和电感耦合等离子体(ICP)技术对石油管的C、Mn、Cr、Mo等元素进行定量分析,确保符合API 5CT标准。金相显微镜观察晶粒度级别(通常要求6-8级),配合显微硬度计测量HV值,评估热处理工艺对微观组织的影响。X射线衍射(XRD)用于检测残余奥氏体含量,预防氢致开裂风险。
2. 几何尺寸与形位公差检测
三维激光扫描系统实现0.05mm精度的外径、壁厚测量,结合数字图像处理技术自动识别椭圆度和弯曲度。特殊设计的通径规(最小通过直径≥95%标称值)验证管道直线度,超声波测厚仪在圆周方向设置32个采样点,构建壁厚分布云图。对于螺纹连接部位,使用三坐标测量机检测锥度、齿高和紧密距,确保API螺纹的密封性能。
3. 力学性能综合测试
依据ASTM A370标准进行拉伸试验,重点监控屈服强度(Rt0.5)、抗拉强度(Rm)和屈强比(通常≤0.93)。夏比V型缺口冲击试验在-46℃低温环境下测定冲击功,确保管材的低温韧性。扩口试验要求达到15%扩口率无裂纹,弯曲试验采用芯棒直径3倍于管径的测试条件。全尺寸疲劳试验模拟管道实际应力条件,循环次数需超过10^7次。
4. 腐蚀与缺陷无损检测
漏磁检测(MFL)技术可识别最小0.5mm深的腐蚀坑,检测速度达到3m/s。超声波相控阵(PAUT)实现多角度扫查,对横向裂纹的检出率提升至99%。远场涡流(RFET)穿透厚壁管检测内部缺陷,电磁声传感器(EMAT)实现非接触式氧化层下裂纹探测。近年来发展的管道内检测器(智能清管器)集成惯性导航和GIS定位,可构建管道三维缺陷图谱。
5. 环境适应性专项检测
HIC氢致开裂试验在NACE TM0284溶液中进行96小时浸泡,断面裂纹率需<2%。SSC硫化应力腐蚀试验采用四点弯曲法,加载80%YS应力评估开裂敏感性。高温高压模拟装置可复现150℃、35MPa工况下的应力腐蚀行为。对于海底管道,还需开展阴极保护电位检测和AC干扰评估,确保保护电位维持在-850mV~-1100mV(CSE)区间。
6. 智能检测技术新趋势
数字射线检测(DR)取代传统胶片技术,缺陷识别效率提升70%。基于深度学习的图像分析系统可自动分级缺陷类型,准确率超过95%。分布式光纤传感(DTS)实现管道全线温度/应变实时监测,空间分辨率达到1米。卫星InSAR技术监测地面沉降,每年可预警毫米级位移风险。2023年发布的API 1163新版标准已将数字化检测数据管理纳入强制要求。
通过构建"材料基础检测+服役性能评价+智能在线监控"的三维质量体系,现代石油管检测技术已将管道事故率降至0.3次/千公里·年以下。随着数字孪生、量子传感等新技术的应用,石油管道的检测精度和效率将进入新的发展阶段。
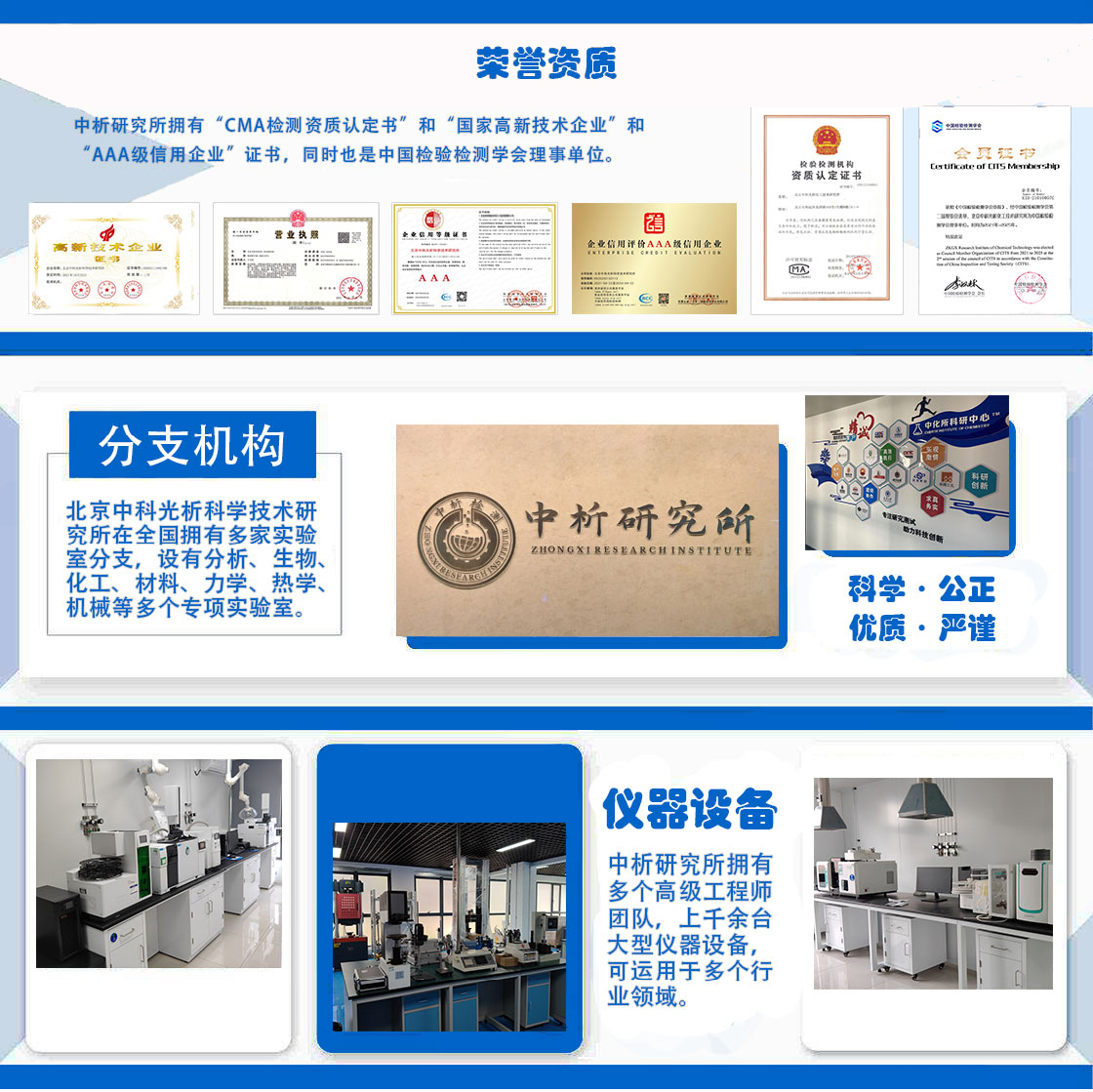
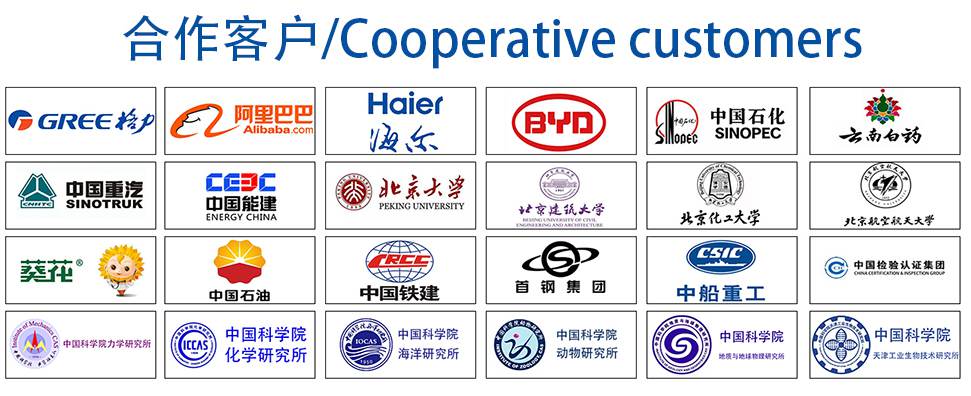