抽油泵及其组件检测的重要性与技术要求
抽油泵作为石油开采和工业流体输送的核心设备,其性能直接影响生产效率和系统安全性。在油田、化工厂、炼油厂等场景中,抽油泵及其组件长期处于高压、高温、腐蚀性介质的严苛工况下,易出现磨损、泄漏、疲劳等问题。定期开展系统性检测能够及时发现潜在故障隐患,避免非计划停机事故,延长设备使用寿命,同时为工艺优化提供数据支持。根据API 11AX、ISO 13709等行业标准要求,检测需覆盖材料性能、结构完整性、密封状态、动态参数等关键指标,并建立全生命周期健康档案。
核心检测项目分类
1. 外观与结构完整性检测
包括泵体、阀座、活塞杆等部件的宏观检查,重点排查裂纹、变形、锈蚀等缺陷。使用渗透检测(PT)和磁粉检测(MT)定位表面缺陷,通过三维扫描比对关键尺寸与设计图纸的匹配度,确保装配精度误差不超过±0.05mm。
2. 材料性能分析
对泵壳体、密封环等关键部件进行金相分析,验证材料晶粒度、夹杂物含量是否符合ASTM E112标准;采用硬度计测定布氏硬度(HB),评估材料抗磨损能力;针对腐蚀风险区域,实施电化学阻抗谱(EIS)测试分析耐蚀性。
3. 密封系统专项检测
采用氦气质谱检漏法(灵敏度达1×10⁻⁶ Pa·m³/s)检测机械密封和法兰连接的泄漏率,在1.5倍工作压力下保压30分钟验证承压能力。同步检查O型圈、填料函的压缩永久变形量,确保密封材料弹性恢复率>85%。
4. 动态性能测试
通过在线监测系统采集泵效、排量系数、容积效率等参数,对比额定工况偏差值。使用振动频谱分析仪测量轴承座振动速度(RMS值≤4.5mm/s为合格),识别叶片通过频率异常;采用红外热像仪监控温升梯度,避免局部过热导致材料失效。
5. 阀门组件功能性验证
对吸入阀、排出阀进行启闭响应时间测试(应≤50ms),使用高速摄影技术分析阀球运动轨迹,测量阀座接触面的平面度(要求≤0.02mm)。通过流量标定实验验证阀隙流量特性曲线与设计曲线的吻合度。
智能化检测技术应用
随着工业物联网(IIoT)技术发展,智能传感器与数字孪生技术已逐步应用于抽油泵检测领域。通过部署压力、温度、振动三轴传感器网络,实现实时数据采集与趋势预测。结合有限元分析(FEA)建立的数字孪生模型,可模拟极端工况下的应力分布,提前预警高疲劳风险区域。统计显示,采用智能检测系统可使故障诊断准确率提升至98%,维护成本降低40%。
检测周期与标准执行
常规检测周期建议为:月度外观检查+季度性能测试+年度全面拆检。对于含硫化氢等腐蚀性介质的工况,需缩短30%检测间隔。所有检测数据应按照API 670规范录入管理系统,形成设备健康指数(EHI)评估报告,作为维修决策和备件管理的依据。
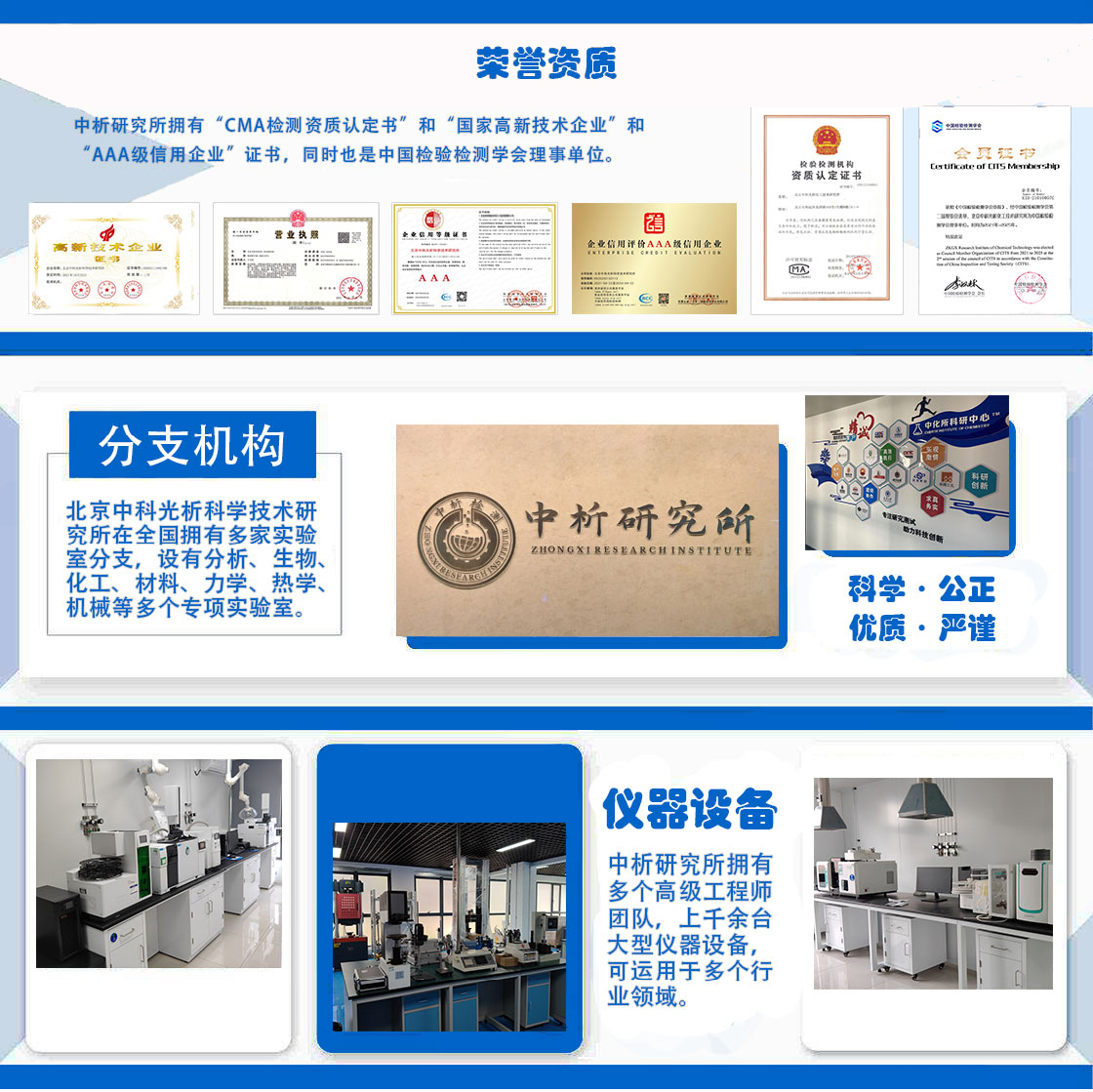
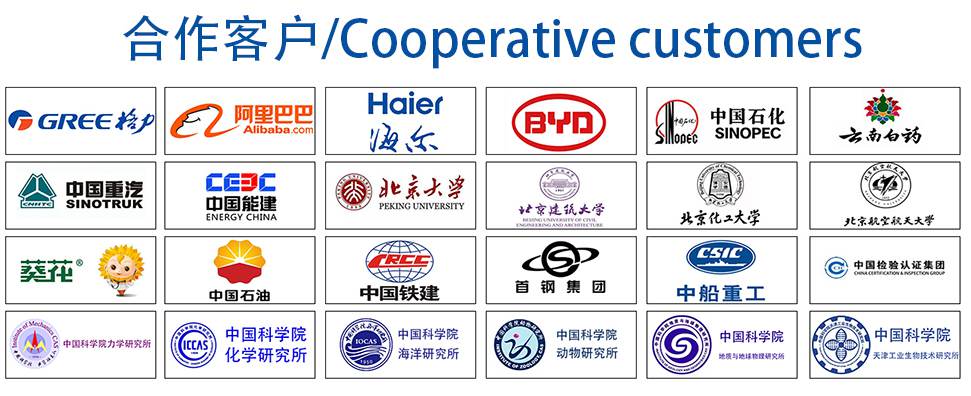