高速摆动自润滑向心关节轴承检测的重要性与挑战
高速摆动自润滑向心关节轴承是航空航天、工业机器人、精密仪器等领域中的核心运动部件,其性能直接影响设备运行的稳定性、寿命及安全性。该轴承通过内置固体润滑材料实现自润滑功能,可在高速摆动、高载荷及极端温度等复杂工况下长期工作。然而,由于其在运动过程中承受交变载荷和频繁摩擦,润滑层损耗、材料疲劳、摩擦副配合精度下降等问题可能引发失效风险。因此,系统性检测项目成为保障轴承可靠性、优化设计参数及延长使用寿命的关键环节。
核心检测项目及技术要点
1. 动态性能测试
通过高频摆动试验台模拟实际工况,记录轴承在不同摆动频率(0-50Hz)、载荷(径向/轴向)和温度(-60℃至200℃)下的运动特性。重点监测扭矩波动、振动频谱及温升曲线,评价轴承的动态稳定性与能量损耗特性(参考GB/T 3944-2020标准)。
2. 摩擦磨损性能评估
采用球盘式摩擦试验机或专用轴承测试装置,测量摩擦系数、磨损量及润滑膜厚度变化。结合SEM电镜分析磨损表面形貌,验证固体润滑剂转移膜的均匀性和抗磨持久性(符合ISO 7148-2规范)。
3. 润滑层性能分析
利用X射线光电子能谱(XPS)和拉曼光谱,检测润滑层化学成分随摆动次数的演变规律。通过纳米压痕仪测定润滑膜硬度与弹性模量,建立润滑性能退化模型。
4. 结构完整性检测
采用显微CT无损扫描技术重构轴承内部结构,识别基体材料裂纹、润滑层剥离等缺陷。结合有限元仿真分析应力分布,验证设计载荷下的结构可靠性。
5. 环境适应性测试
开展真空、高湿度、盐雾等特殊环境验证,评估轴承抗氧化、抗腐蚀能力及极端工况下的性能衰减规律(参照HB 7269-2017航空标准)。
典型失效模式与检测优化方向
实际应用中,润滑膜局部失效(占比37%)、接触面微动磨损(28%)和材料疲劳断裂(19%)是主要失效形式。建议通过多参数耦合检测技术,建立载荷-频率-温度-磨损量的多维关联模型,推动轴承向长寿命、低能耗方向迭代。
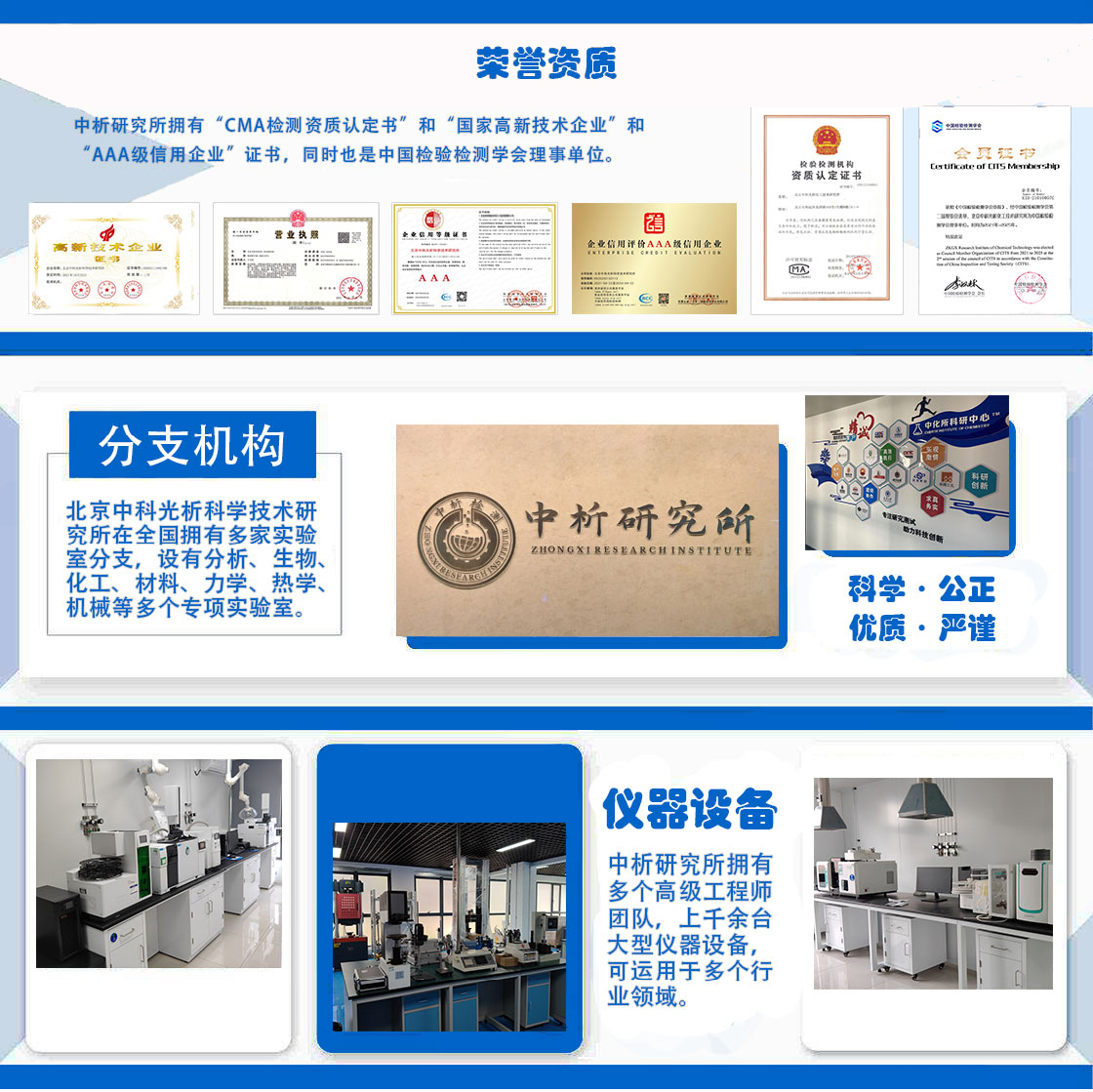
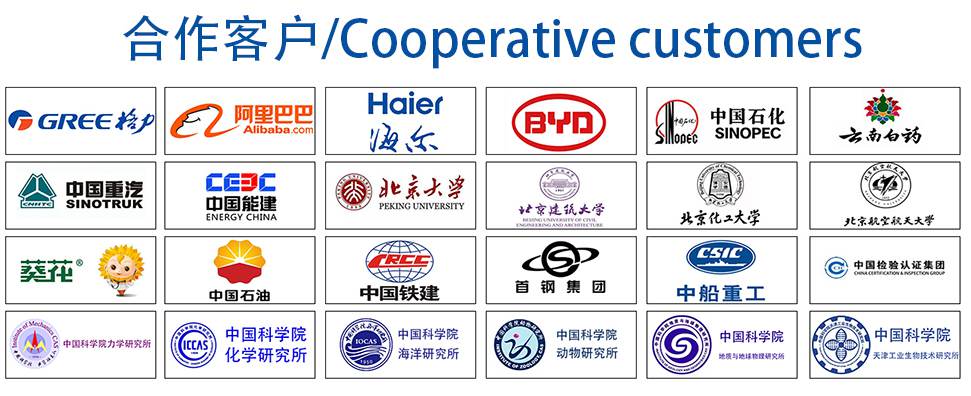