滚动轴承标准器检测的重要性与检测项目解析
滚动轴承作为机械设备中不可或缺的核心部件,其性能直接关系到机械系统的运行效率、寿命和安全性。为保障轴承生产质量与使用可靠性,标准器检测成为行业质量控制的核心环节。滚动轴承标准器作为校准测量设备的基准工具,其自身精度直接影响下游产品的检测结果。因此,对标准器的定期检测与维护不仅是ISO质量管理体系的要求,更是确保工业制造精度的重要保障。
关键检测项目体系
1. 几何尺寸精度检测
通过三坐标测量仪(CMM)或激光扫描技术对标准器的内径、外径、宽度等关键尺寸进行微米级测量,检测项目包含:
- 基准直径偏差(DΔmp)
- 单一平面直径变动量(Vdsp)
- 套圈宽度偏差(ΔBs)
- 滚道曲率半径偏差等
2. 表面质量评估
采用白光干涉仪和粗糙度仪进行表面特性检测:
- 表面粗糙度Ra值(0.05-0.4μm)
- 波纹度分析(WCA/WDA指标)
- 表面缺陷检测(划痕、压痕、锈蚀)
- 热处理后的表面硬度(HRC58-62)
3. 材料性能验证
使用金相显微镜和光谱分析仪进行材料完整性检测:
- 微观组织结构(马氏体含量≤3%)
- 材料成分分析(GCr15钢Cr含量1.45-1.65%)
- 残余奥氏体含量(≤8%)
- 非金属夹杂物评级(ASTM E45标准)
4. 动态特性测试
通过专用检测平台模拟实际工况:
- 旋转精度测试(径向跳动≤2μm)
- 摩擦力矩测量(≤0.5N·m)
- 振动加速度级检测(Z组≤45dB)
- 温升试验(ΔT≤35℃)
5. 环境适应性检测
在气候试验箱中进行特殊环境测试:
- 盐雾试验(480h无红锈)
- 高低温循环测试(-40℃~150℃)
- 防尘密封性验证(IP6X等级)
- 润滑脂保持能力测试
检测技术发展趋势
随着智能制造的发展,滚动轴承标准器检测正向着智能化、在线化方向演进。机器视觉系统可实现表面缺陷的实时识别,基于大数据的预测性维护系统能提前发现标准器的精度衰减趋势。同时,新型纳米级测量技术的应用使检测精度达到10nm级别,为高端装备制造提供更精准的质量保障。
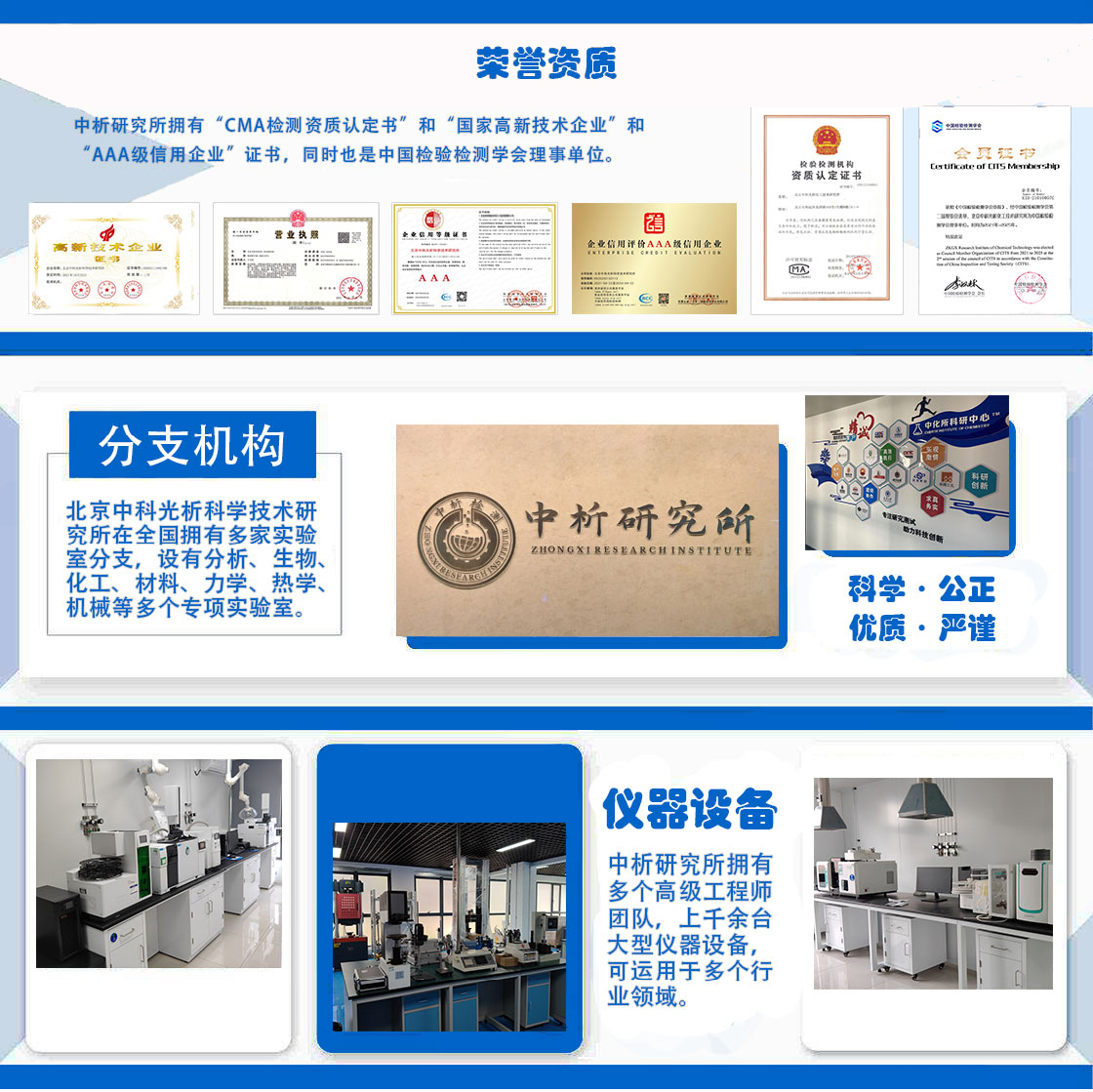
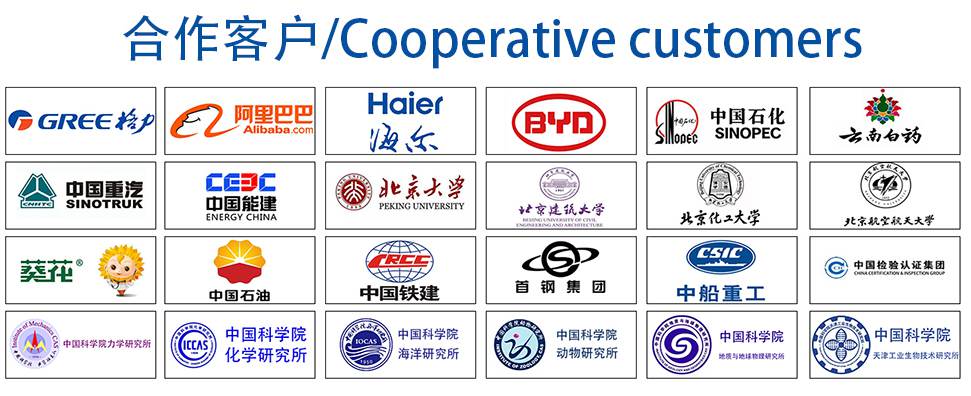