连续采煤机检测的重要性与核心项目
连续采煤机作为现代化煤矿开采的核心装备,其性能稳定性直接关系矿井生产效率与作业安全。在复杂的地下环境中,设备长期承受高载荷、强振动及粉尘侵蚀,可能导致机械结构磨损、电气系统故障或液压泄漏等问题。因此,定期开展系统性检测是确保设备高效运行、延长使用寿命和预防重大事故的必要手段。行业规范(如GB/T 25709-2010《连续采煤机》)明确要求建立完善的检测体系,通过科学评估设备状态,实现从“事后维修”向“预防性维护”的转变。
机械结构完整性检测
重点检查截割机构、行走机构与传动系统的磨损变形情况。采用三维激光扫描技术评估截割滚筒齿座磨损量,通过扭矩传感器测试传动轴载荷分布,同时对履带链节间隙、导向轮磨损进行量化分析。针对关键焊缝部位,需使用磁粉探伤或超声波检测法排查裂纹缺陷。
电气系统安全检测
涵盖电机绝缘性能测试、控制回路响应时间测定及防爆结构密封性验证。使用兆欧表检测电动机绕组绝缘电阻(要求≥100MΩ),通过PLC模拟信号验证急停保护装置的触发延迟(应≤0.5s),并采用气压试验法检验隔爆接合面气密性(保压时间≥10min)。
液压系统效能检测
包括泵站输出压力稳定性测试、阀组响应精度校验和管路泄漏监测。运用动态压力传感器记录截割升降油缸的工作压力波动(允许偏差≤额定值±5%),采用红外热成像技术定位异常温升点,并对液压油清洁度进行实验室颗粒度分析(NAS等级需≤8级)。
安全防护装置功能性验证
强制检测甲烷断电闭锁装置、急停系统与人员接近预警功能。在模拟工况下测试甲烷浓度超限时设备断电响应时间(≤2s),验证遥控急停按钮的有效作用距离(≥15m),并通过激光扫描装置检查防碰撞系统的探测盲区(应<0.5m)。
智能监测系统校准
针对设备配备的在线监测模块(如振动传感器、温度监测单元),需采用标准信号源进行计量校准,确保数据采集误差率≤1.5%。同时验证数据无线传输系统的丢包率(需<0.3%)和延时特性(≤200ms),保障远程监控的可靠性。
与建议
完整的连续采煤机检测应形成包含200+项参数的评估报告,结合设备运行大数据建立寿命预测模型。建议每500工作小时进行常规检测,大修周期不超过12000小时,特别在高强度开采阶段应缩短30%检测间隔。通过标准化检测流程,可将设备故障率降低40%,显著提升矿井综合效益。
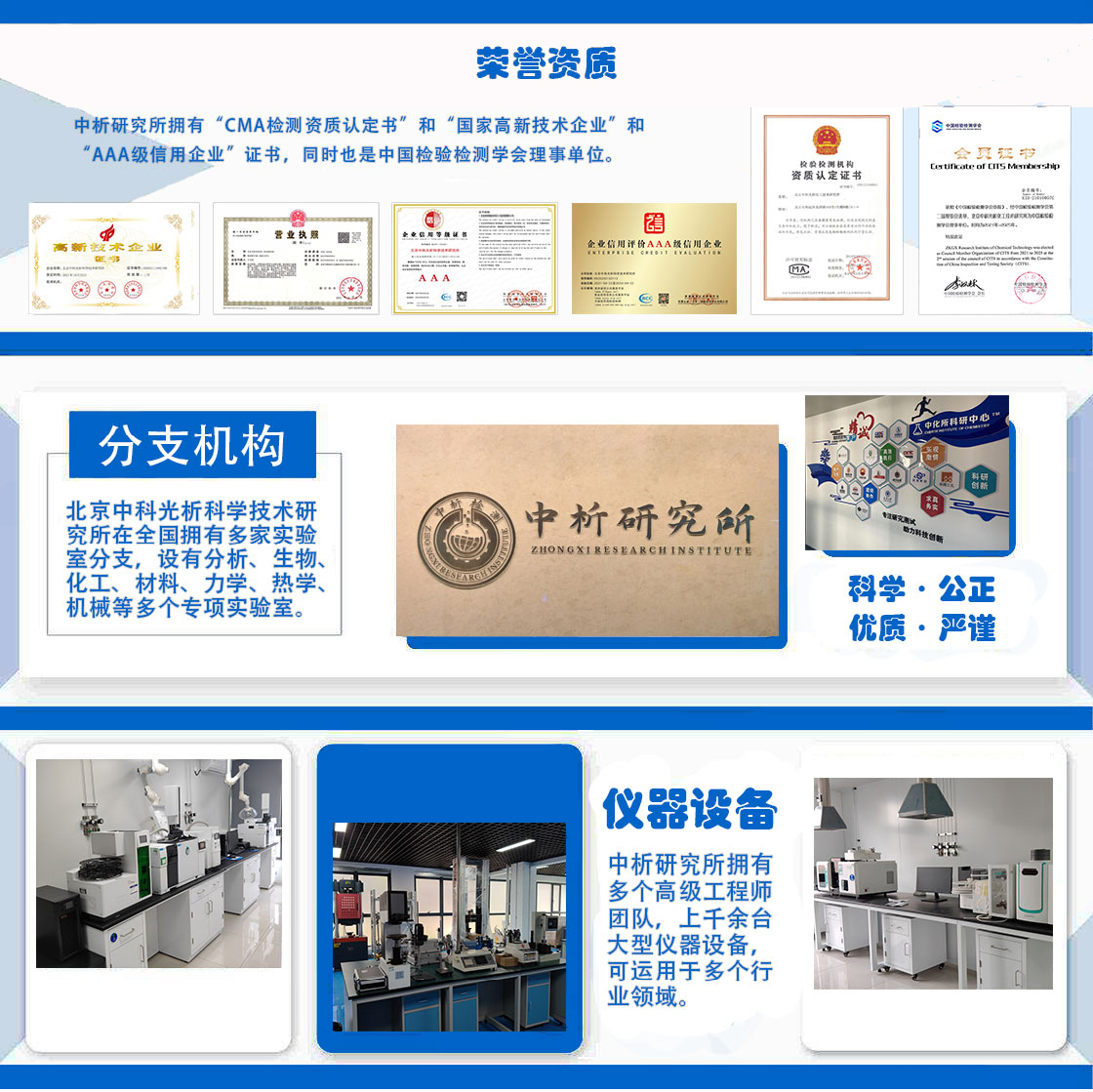
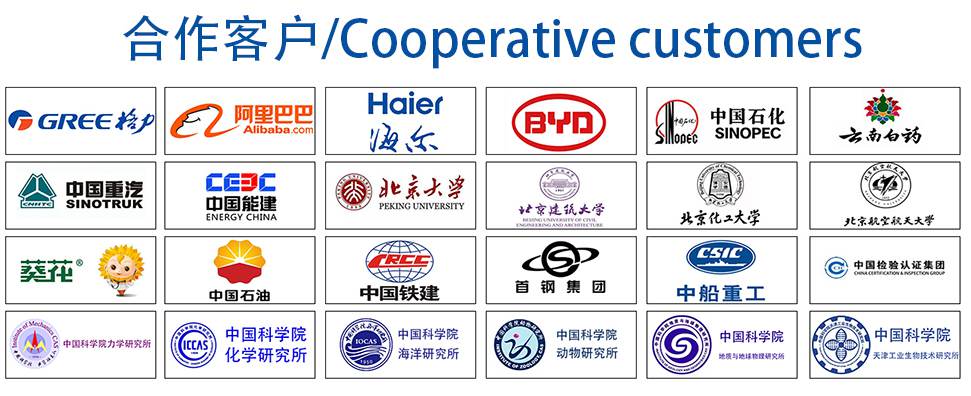