汽车气制动装置用储气筒检测的重要性
储气筒是汽车气制动系统的核心部件之一,主要用于储存压缩空气并为制动装置提供稳定的压力来源。其性能直接关系到车辆制动系统的可靠性和安全性。由于储气筒长期处于高压、振动、温度变化等复杂工况下,若存在泄漏、裂纹或材料老化等问题,可能导致制动失效甚至引发严重事故。因此,在生产制造、定期维护及故障排查中,对储气筒进行系统性检测是保障行车安全的关键环节。
储气筒检测的主要项目
1. 气密性测试
气密性是储气筒的基础性能指标。检测时需将储气筒充入额定工作压力(通常为0.8-1.2MPa)的压缩空气,通过保压试验观察压力下降速率。依据国家标准GB/T 13061-2017,保压时间不低于5分钟,压力降不得超过初始值的5%。检测中需使用高精度压力传感器和专用密封工装,确保结果准确性。
2. 耐压强度测试
为验证储气筒的极限承载能力,需进行爆破压力测试。试验压力通常为工作压力的2-3倍,通过水压试验机逐步增压至试样破裂,记录爆破压力值。合格产品应满足设计要求的爆破安全系数(一般≥3),同时观察筒体是否发生塑性变形或异常开裂。
3. 材料与焊缝检测
储气筒多采用低碳钢或铝合金材料,需通过金相分析、化学成分检测及硬度测试确保材料符合标准。焊缝质量可通过超声波探伤(UT)或X射线检测(RT)进行无损探伤,重点检查焊缝是否存在气孔、夹渣、未熔合等缺陷,避免因焊接问题导致结构失效。
4. 安全阀校验
储气筒配套的安全阀需定期检测其开启压力和回座压力。通过专用校验台模拟超压工况,验证安全阀在设定压力范围内(通常为1.1-1.3倍工作压力)能否及时释放过压气体,并在压力下降后自动复位,确保过载保护功能正常。
5. 环境适应性测试
包括盐雾试验(验证耐腐蚀性)、高低温循环试验(-40℃~120℃)、振动疲劳测试等,模拟极端环境对储气筒的影响。测试后需复测气密性和结构完整性,确保产品在全生命周期内的可靠性。
检测标准与规范
储气筒检测需严格遵循GB/T 13061-2017《汽车用压缩空气储气筒技术条件》、QC/T 200-2015《汽车气制动系统用储气筒性能要求及试验方法》等标准。对于出口产品,还需符合ECE R13、SAE J1402等国际法规要求。
结语
储气筒的检测需综合运用物理试验、化学分析及无损检测技术,从材料性能到结构设计进行全面验证。通过标准化检测流程和齐全设备应用,可有效预防制动系统故障,保障车辆运行安全。生产企业、维修单位及监管部门应高度重视储气筒的定期检测与质量管控,为道路交通安全筑牢技术防线。
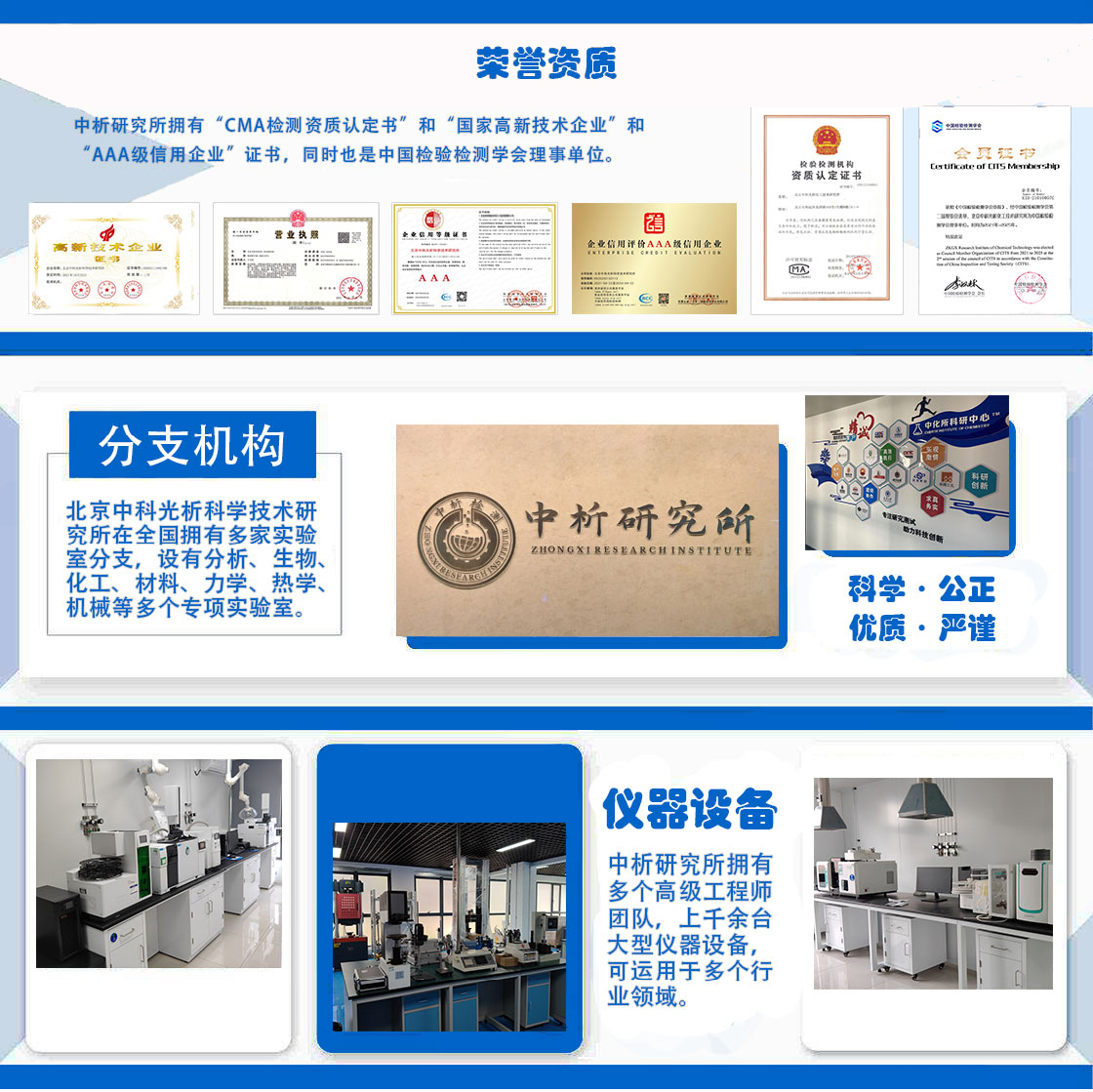
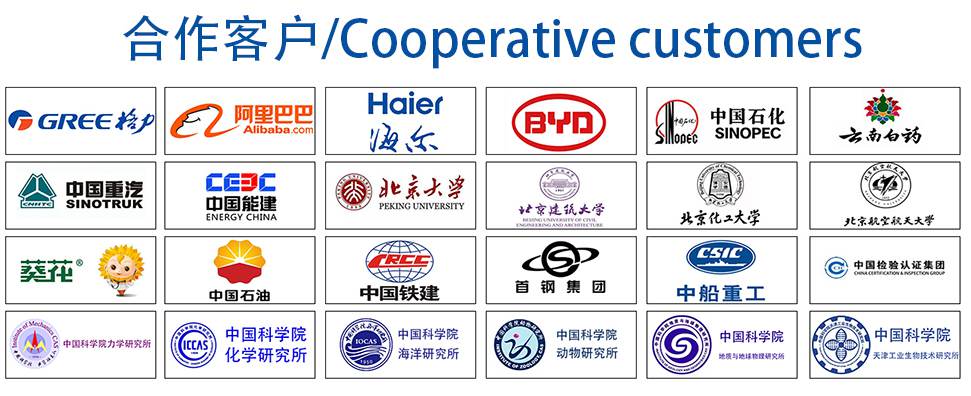