多层瓷介(独石)电容器DPA分析检测的重要性
多层瓷介电容器(MLCC),又称独石电容器,因其体积小、容量大、高频性能优异等特点,广泛应用于通信、医疗、航空航天等高可靠性领域。然而,在复杂工作环境和高频高压条件下,其内部结构缺陷可能导致性能劣化甚至失效。破坏性物理分析(Destructive Physical Analysis, DPA)作为一种系统性检测手段,能够通过解剖、观察和测试,全面评估电容器的材料工艺、结构完整性和潜在失效风险,为产品可靠性提供关键数据支撑。
DPA检测的核心项目与流程
DPA分析通常包括以下关键检测项目:
1. 外观与尺寸检查
通过高倍显微镜观察电容器表面是否存在裂纹、气泡、电极氧化或镀层脱落等缺陷,并使用精密测量工具验证尺寸是否符合设计要求。此阶段需重点关注端电极的焊接质量和介质层的均匀性。
2. 内部结构解剖分析
采用机械切割或聚焦离子束(FIB)技术对电容器进行逐层剖切,利用扫描电子显微镜(SEM)和能谱分析(EDS)观察内部介质层与电极的叠层结构。重点检测层间分层、电极错位、孔隙率及烧结致密性等问题。
3. 电性能验证
在解剖前后分别测试电容器的容量、损耗角正切(tanδ)、绝缘电阻(IR)及耐压特性,对比数据差异以评估内部缺陷对电气性能的影响。同时需进行温度循环、湿度老化等加速寿命试验,模拟实际应用中的应力条件。
4. 材料成分与杂质分析
通过X射线荧光光谱(XRF)和拉曼光谱等技术,分析介质材料(如BaTiO₃基陶瓷)的晶体结构、掺杂元素含量及杂质分布,确保材料参数符合设计标准,避免因成分偏差导致的介电性能下降。
5. 失效模式定位
结合热成像和局部放电检测技术,定位电容器内部的短路点或热点区域,并通过显微切片确定失效机理(如电迁移、介质击穿或热应力开裂)。
DPA检测的意义与挑战
DPA分析不仅能发现现有缺陷,还可通过数据回溯优化生产工艺。例如,检测到层间孔隙率过高可能指向烧结工艺参数不当;电极断线则需改进印刷或叠层精度。然而,该过程需平衡破坏性检测的成本与样本代表性,同时需依赖高精度设备与专业分析人员,对检测机构的综合能力提出较高要求。
随着MLCC向微型化、高容化方向发展,DPA检测技术需进一步融合AI图像识别和大数据分析,以提升缺陷判读效率,为高可靠电子系统的设计与维护提供更精准的保障。
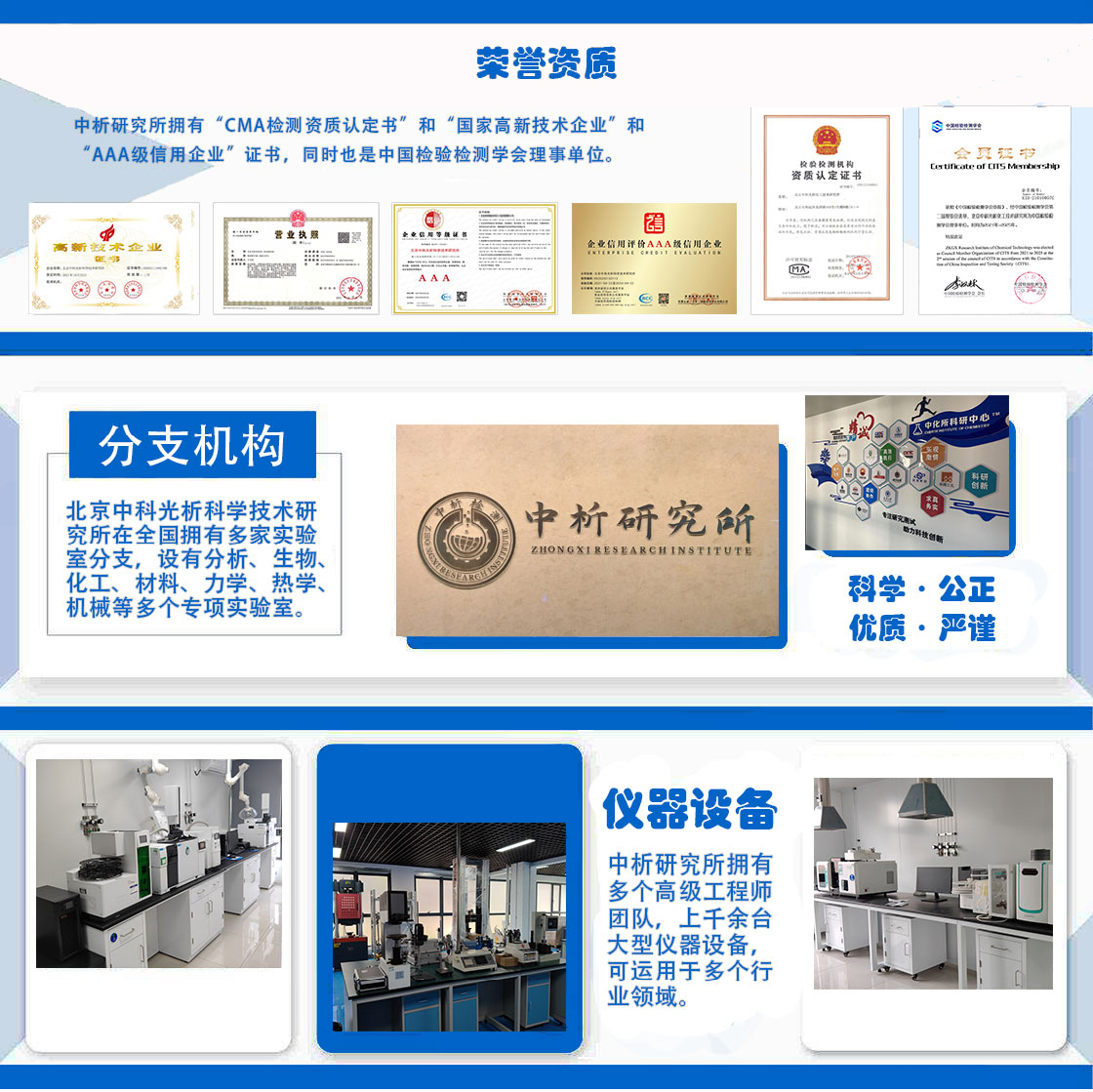
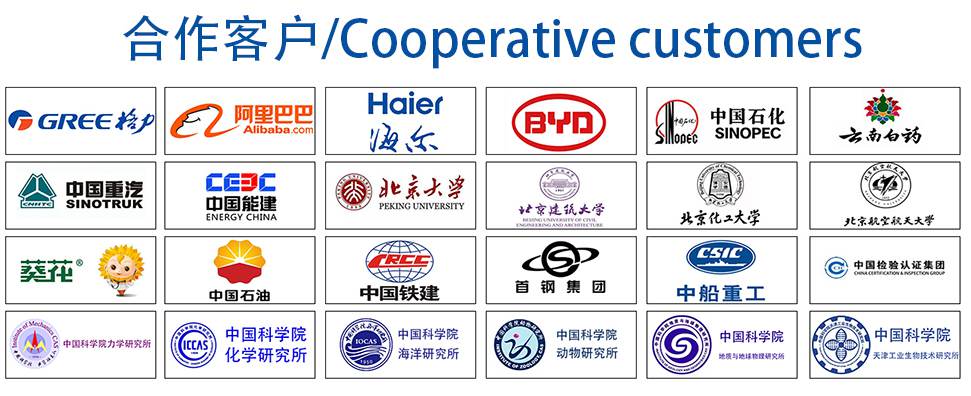