管路及连接件检测的重要性与实施方法
在现代工业生产和工程系统中,管路及连接件的安全性与可靠性直接关系到设备运行效率、能源传输稳定性以及人员安全。管路系统广泛应用于石油化工、电力能源、给排水工程、航空航天等领域,其检测工作需覆盖材料完整性、密封性能、耐压能力等多个维度。通过科学的检测手段,能够提前发现潜在缺陷,避免因泄漏、爆裂或腐蚀引发的安全事故,同时延长设备使用寿命。
管路及连接件核心检测项目
1. 外观与几何尺寸检测 通过目视检查、超声波测厚仪或卡尺等工具,检查管路表面是否存在裂纹、变形、锈蚀等问题,同时验证管径、壁厚、椭圆度等参数是否符合设计规范(如GB/T 20801、ASME B31.3)。
2. 密封性测试 采用气压试验或水压试验评估连接件的密封性能。例如对法兰、螺纹接头等部位进行保压测试,观察压力表变化或使用检漏液(如肥皂水)定位泄漏点,确保系统在额定压力下无渗漏。
3. 材料成分与力学性能分析 通过光谱分析仪、硬度计、拉伸试验机等设备,验证管路材质是否符合标准(如304不锈钢、碳钢Q235B),并检测抗拉强度、屈服强度等力学指标,防止材料错用或劣化问题。
4. 腐蚀与结垢评估 针对高温、高压或腐蚀性介质环境,使用内窥镜检查管路内壁腐蚀状况,或通过无损检测技术(如涡流检测、磁粉探伤)发现隐蔽缺陷。对结垢严重的管路需进行清洗后二次检测。
5. 连接强度测试 对焊接接头进行X射线探伤(RT)或超声波探伤(UT),确保焊缝无气孔、夹渣等缺陷;对卡箍、快装接头等可拆卸连接件,需进行反复拆装后的密封性和紧固力测试。
检测流程与标准规范
典型检测流程包括:初步外观检查→清洁与预处理→无损检测→压力测试→数据记录与分析→出具报告。需严格遵循行业标准,如《压力管道安全技术监察规程》(TSG D0001)、ISO 15649(工业管道系统)等,并根据介质特性(如易燃易爆、有毒)增加专项检测项目。
检测注意事项
检测前需确认管路系统已泄压、排空介质;针对高风险场景应使用防爆型检测设备;长期服役的管路需结合历史运行数据(如压力波动频率、介质腐蚀性)制定检测周期。检测机构需具备CMA/ 资质,确保检测结果的权威性与法律效力。
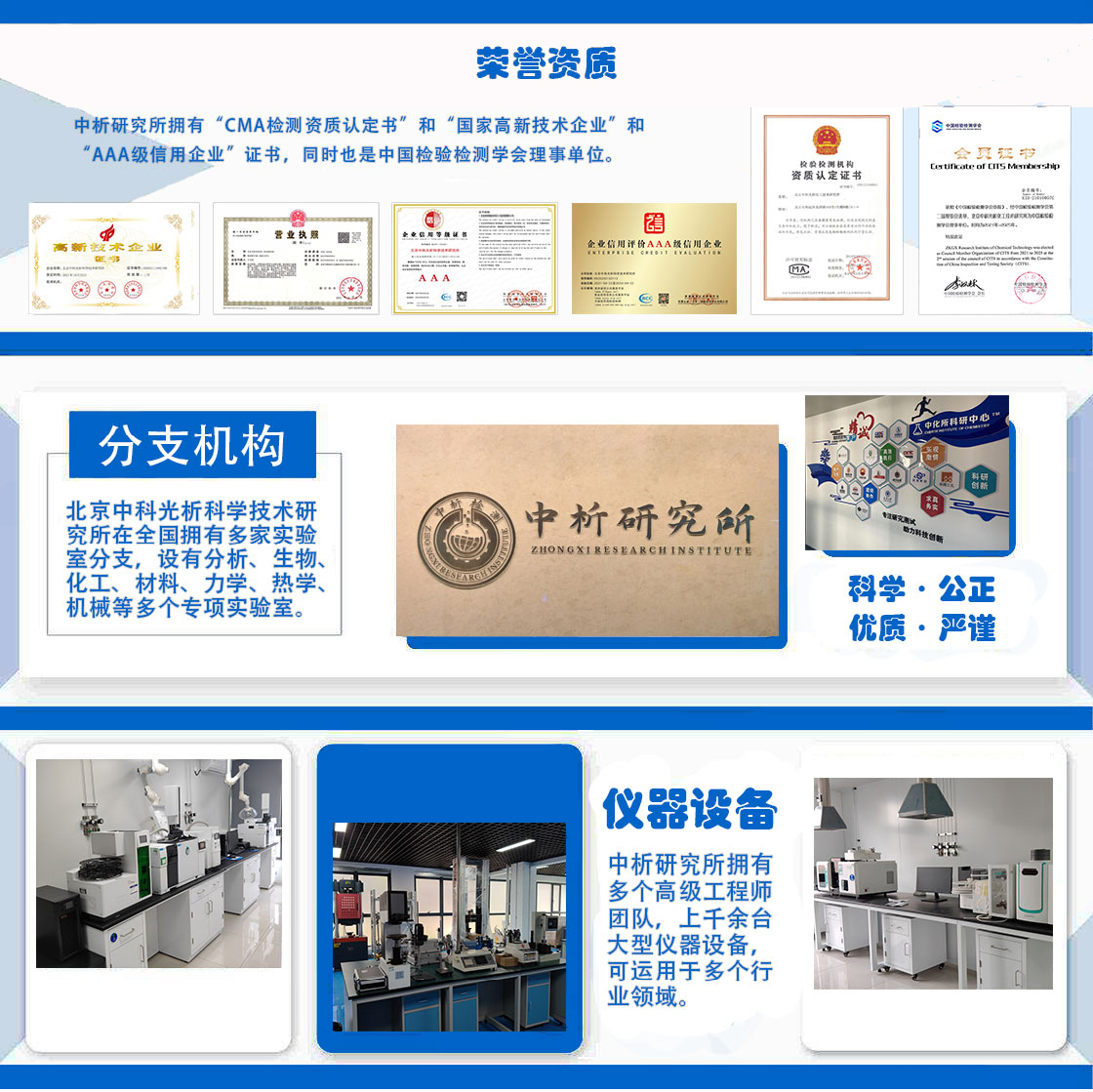
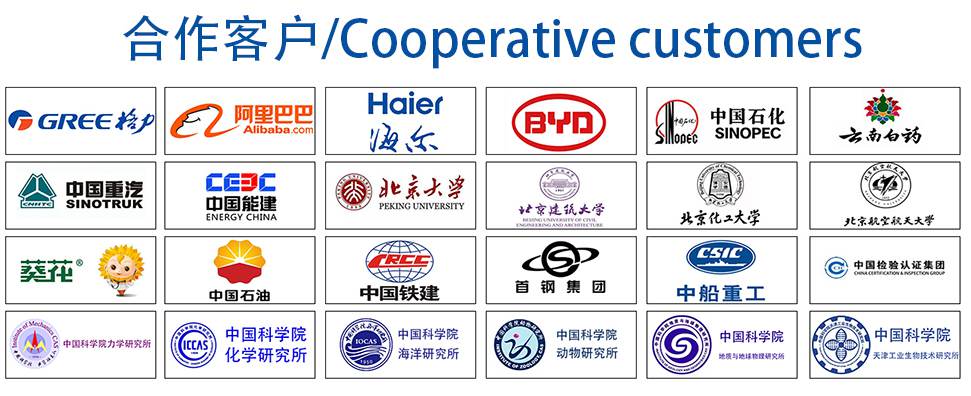