柴油机喷油器检测的重要性及核心项目
作为柴油发动机燃油系统的核心部件,喷油器承担着精准供油、雾化燃油和优化燃烧的关键职责。其性能直接影响发动机动力输出、燃油经济性和尾气排放质量。据统计,约35%的柴油机故障源于喷油系统异常,而喷油器故障在其中占比高达60%以上。定期专业检测不仅能预防突发故障,还可提升燃油效率8-12%,降低颗粒物排放30%以上,是保障设备长效运行的必要措施。
六大关键检测项目详解
1. 喷射压力测试
使用数字式喷油器测试台测量开启压力,对比原厂标准值(通常180-220Bar)。压力偏差超过±5%需校准,压力不足会导致雾化不良,过高则加速磨损。新型压电式喷油器还需检测多次喷射压力波动曲线。
2. 雾化质量评估
通过观察窗或高速摄像记录喷射形态,优质雾化应呈均匀锥形无滴漏。使用微粒分析仪检测油滴直径(理想值<15μm),雾化不良会使燃烧效率下降6-9%,HC排放增加2-3倍。
3. 密封性检测
采用保压测试法:加压至工作压力1.2倍,观察30秒内压降不超过5%。针阀偶件泄漏会引起二次喷射,导致功率下降10-15%,喷嘴积碳增速300%以上。
4. 流量一致性测试
在标准工况下测量各喷孔流量,偏差应<3%。使用质量流量计进行100次喷射循环测试,流量波动过大会造成气缸工作不均衡,引发异常振动。
5. 电磁阀响应检测
对电控喷油器进行示波器检测,要求开启响应时间<0.5ms,关闭延迟<0.3ms。波形异常可能反映线圈老化或控制电路故障,导致喷油正时误差超过2°曲轴转角。
6. 微观形貌检查
运用50倍工业内窥镜观察喷孔状态,积碳覆盖超过30%需清洗。测量针阀导向部磨损量,超过0.005mm应更换偶件,避免燃油泄漏量超标。
智能检测技术发展趋势
随着工业4.0技术的普及,喷油器检测正向智能化发展。采用AI图像识别系统可自动分析雾化模式,声发射传感器能捕捉针阀运动的细微异常,大数据平台可建立全生命周期性能预测模型。这些技术使检测效率提升40%,故障识别准确率达98%以上,为柴油机健康管理提供可靠保障。
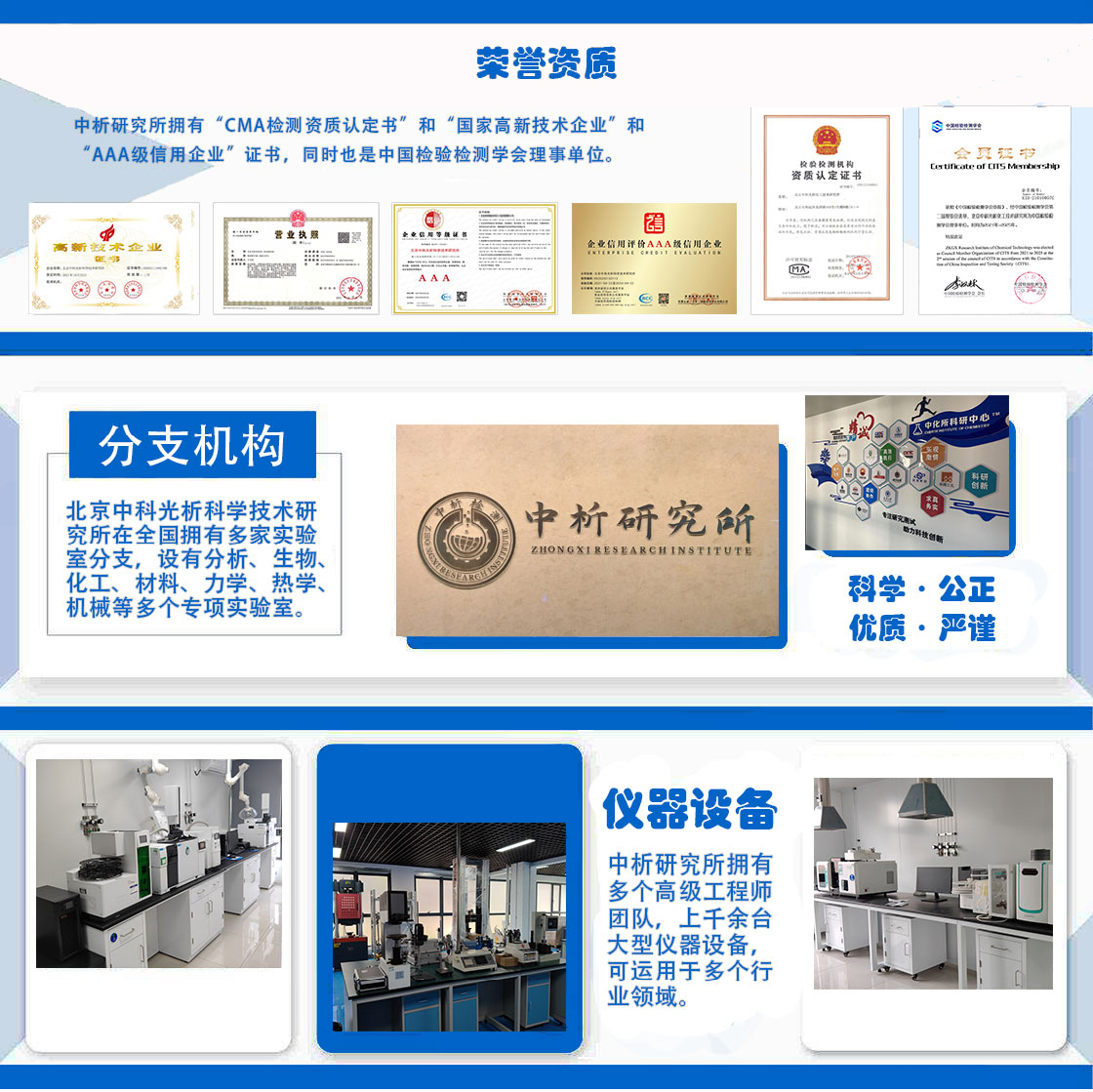
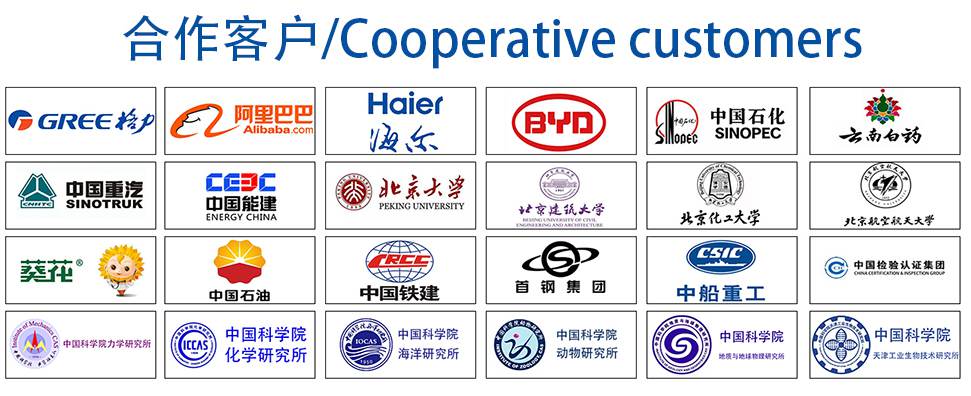